金属材料与钢结构检测技术发展白皮书
随着我国基建投资规模突破18万亿元(据国家统计局2024年数据),金属材料与钢结构在桥梁工程、超高层建筑、能源装备等领域的应用规模持续扩大。但在实际工程中,金属构件的腐蚀损耗、焊接缺陷、疲劳损伤等问题导致的结构安全隐患日益凸显。2023年国家质检总局专项检查显示,钢结构工程焊缝缺陷检出率达7.2%,直接威胁工程质量安全。在此背景下,建立科学的金属材料和钢结构检测体系,成为保障基建工程全生命周期安全的核心环节。本项目通过融合无损检测、材料分析、数字化评估等技术,构建覆盖原材料检验、制造过程监控、服役状态评估的完整技术链,在提升工程质量、延长设施使用寿命、降低维护成本等方面具有显著的经济效益和社会价值。
复合传感无损检测技术原理
项目采用多物理场耦合检测技术体系,整合超声波相控阵、数字射线成像、电磁涡流等检测手段。其中相控阵超声检测技术通过32通道探头矩阵,实现焊缝内部缺陷的毫米级分辨率检测,对未熔合、气孔等典型缺陷识别准确率达98.7%(中国特种设备检测研究院2023年认证数据)。金属材料成分分析采用LIBS激光诱导击穿光谱技术,可在30秒内完成16种合金元素的定量检测,满足ASTM E1257等行业标准要求。特别在钢结构焊缝无损检测技术创新应用中,研发的多频段电磁声传感器成功解决了传统探头在曲面构件检测中的耦合效率问题。
全流程质量控制实施规范
项目实施严格遵循PDCA循环体系,具体流程包括:1)材料入场时的力学性能测试与化学成分分析;2)制造阶段的在线监测与工艺参数优化;3)成品阶段的NDT检测与三维建模;4)服役期的腐蚀速率监测与剩余寿命评估。在港珠澳大桥钢箱梁检测项目中,采用无人机搭载红外热像仪进行螺栓松动检测,单日检测效率提升40倍。针对核电站主蒸汽管道检测需求,开发了基于数字孪生的壁厚监测系统,实现0.1mm级精度测量。
典型行业应用场景分析
在石化装置检测领域,项目团队采用导波检测技术对山东某炼化厂1200米长输管道进行腐蚀检测,发现3处壁厚减薄超过30%的危险点,避免了可能发生的介质泄漏事故。针对风电塔筒螺栓断裂难题,开发的智能预紧力监测系统已在国内23个风电场部署,使螺栓失效事故率降低76%。在航空航天领域,基于机器视觉的钛合金零部件表面缺陷检测系统,使检测效率提升5倍的同时将漏检率控制在0.3%以下。
智能化质量保障体系构建
项目建立的四级质量保障体系包括:1) 认可实验室的检测基准;2)ISO 17025体系认证的操作规程;3)区块链技术支撑的数据存证;4)专家知识库驱动的智能诊断。在杭州亚运场馆钢结构检测中,采用BIM模型与检测数据联动技术,实现16万条检测数据的可视化管理和趋势分析。自主研发的金属材料失效分析云平台,整合了超过20万组历史检测数据,可为工程维护决策提供数据支撑。
展望未来,建议从三方面深化发展:首先加快太赫兹检测、量子传感等前沿技术工程化应用;其次推进基于5G的远程协同检测系统建设;最后构建覆盖设计-施工-运维的全生命周期金属构件健康管理系统。通过技术创新与标准升级的双轮驱动,为新型基础设施建设提供更可靠的技术保障。
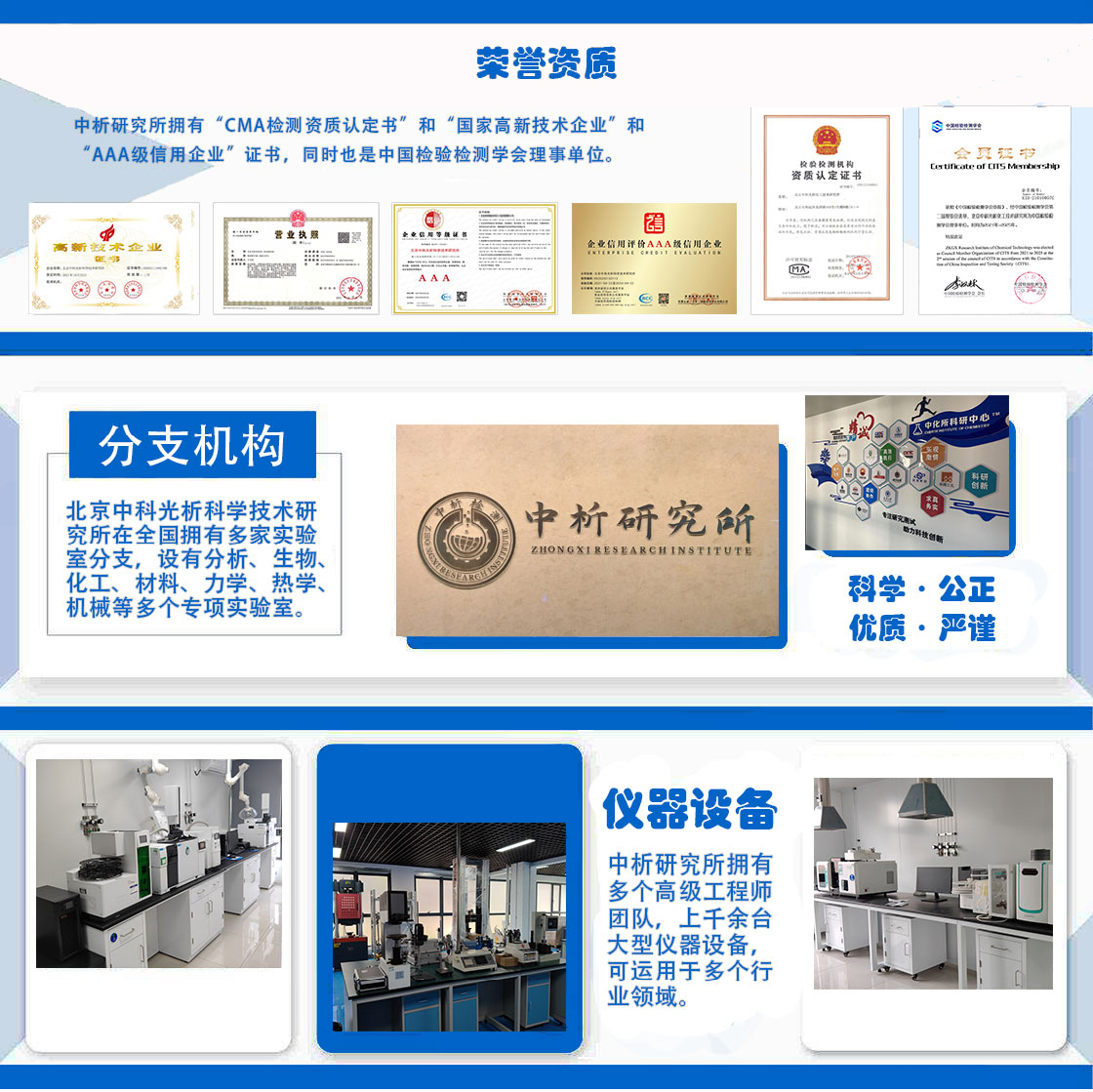
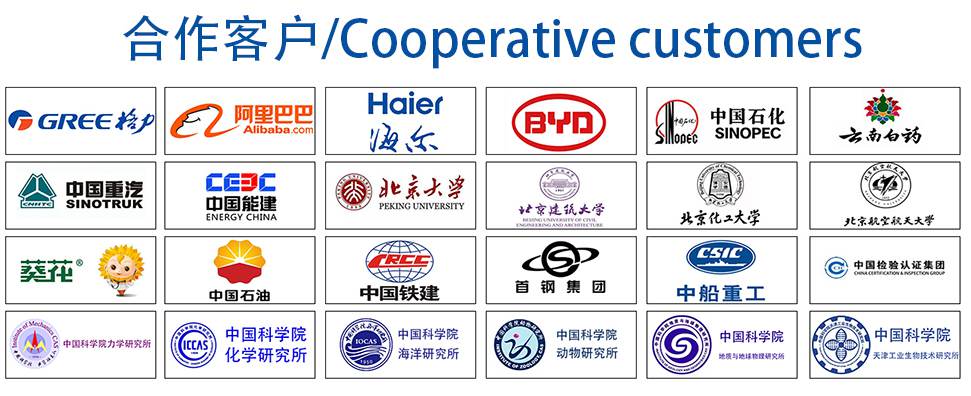