汽车电子电器零部件检测
在汽车产业向电动化、智能化加速转型的背景下,电子电器零部件在整车成本中的占比已超过35%(据中国汽车技术研究中心2024年行业报告)。车载传感器、域控制器、线束系统等核心组件的性能稳定性直接关系到车辆安全与用户体验。汽车电子电器零部件检测项目作为贯穿研发、生产、认证全周期的质量保障手段,其核心价值在于通过系统性验证降低10%-15%的售后故障率(国际汽车工程师学会2023年数据)。该项目不仅满足UNECE R155等国际网络安全法规要求,更通过正向开发测试缩短20%的新品上市周期,显著提升车企在新能源和智能网联领域的市场竞争力。
技术原理与检测体系架构
基于V模型开发框架的检测体系采用硬件在环(HIL)仿真与实物测试相结合的方法。以车载以太网通信协议检测为例,通过TSN时间敏感网络仿真平台,可在-40℃至125℃温变环境下验证数据传输时延小于3μs的达标率(满足ISO 21434标准)。电磁兼容性(EMC)测试模块整合18种干扰源模拟,确保零部件在200V/m场强下的功能完整性。通过构建"信号完整性分析+故障树建模"的双重验证机制,检测系统可精准定位线束串扰等隐性缺陷。
全生命周期实施流程
典型检测项目涵盖四个阶段:需求分析阶段建立ASPICE三级流程文档,设计验证阶段运用DOE试验设计法完成16组正交实验,生产一致性阶段部署AI视觉检测设备实现0.02mm精度的接插件装配检测,市场监督阶段通过云端数据平台监测零部件10年耐久性表现。某德系车企在智能座舱域控制器检测中,采用该流程使软件刷写失败率从1.2%降至0.15%,显著提升产线直通率。
行业应用与质量赋能
在新能源汽车三电系统检测领域,项目团队为某电池厂商开发的"多物理场耦合测试方案",通过模拟2000次充放电循环,成功将电池模组温差控制在±1.5℃以内。针对L3级自动驾驶系统,创新性地引入"预期功能安全(SOTIF)场景库",包含236种边缘案例测试场景,使目标识别漏报率降低40%。在车载以太网线束检测方面,采用TDR时域反射技术可将阻抗失配故障定位精度提升至5cm级别,帮助厂商年节省质量成本超1200万元。
数字化质量保障体系
基于ISO 17025构建的实验室管理体系,集成区块链技术实现检测数据全程溯源。通过部署智能测试资产管理系统(TAM),使设备利用率从65%提升至92%。在长三角某检测中心,数字孪生平台将环境舱调试时间缩短70%,同时实现能耗降低18%。该体系已获得IECEE-CBTL国际互认资质,检测报告获48个国家认可,助力国内零部件企业突破国际贸易技术壁垒。
随着EE架构向中央计算平台演进,检测技术需向"软硬协同验证"方向发展。建议行业重点攻关三项能力:建立基于MBSE的虚拟验证环境,开发支持10Gbps高速总线的测试装备,构建覆盖车路云协同的V2X通信测试场景库。政府部门应加快完善智能网联汽车检测标准体系,推动国家级检测认证平台数据互联互通,为我国汽车电子产业参与竞争筑牢质量根基。
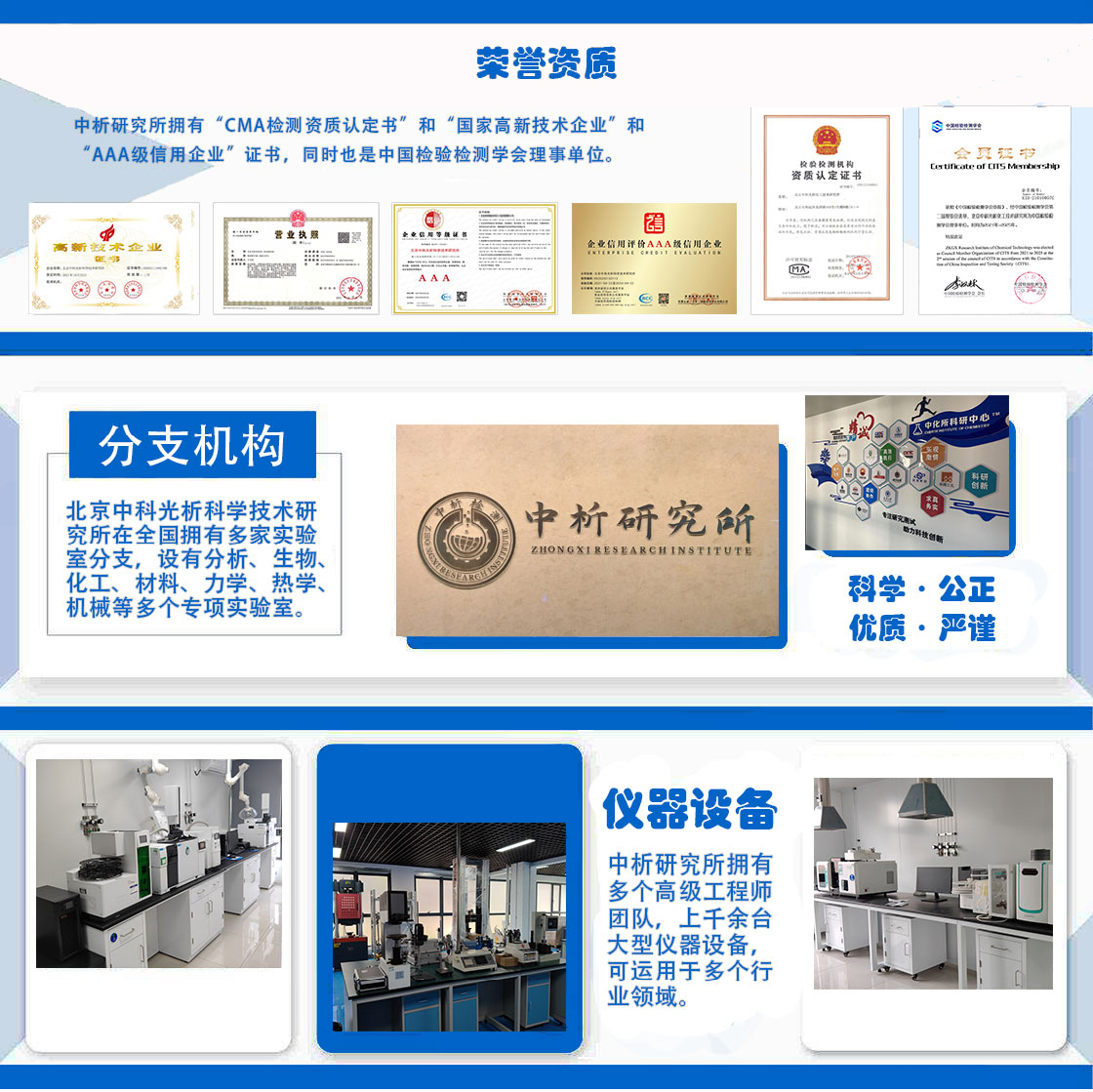
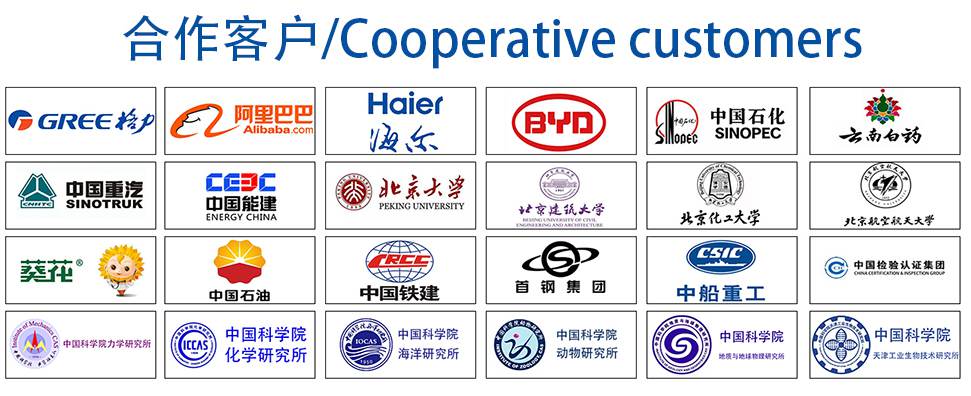