缓冲垫高度检测技术白皮书
随着高端制造业智能化转型加速,缓冲组件作为精密设备防护系统的核心单元,其质量控制标准持续提升。据中国机械工业联合会2024年数据显示,物流自动化设备故障案例中27%源于缓冲系统失效,其中高度偏差导致的冲击吸收异常占比达68%。在此背景下,基于动态形变分析的缓冲垫高度检测技术,成为保障工业设备安全运行的关键环节。该项目通过非接触式三维扫描与压力模拟算法的融合应用,实现了毫米级形变轨迹的精准捕获,可将安全防护系统的预警准确率提升至99.6%(中国质量认证中心,2023)。其核心价值不仅体现在提升生产良品率方面,更为工业4.0时代的设备预防性维护提供了可量化的决策依据。
多模态传感技术原理
本检测系统采用光学三角测量与分布式压力传感的协同工作机制。1280万像素工业相机以120fps速率采集缓冲垫表面微结构,配合16通道压电传感器获取动态载荷下的形变特征。通过建立"接触应力-弹性恢复"数学模型,系统可精准解算缓冲垫全生命周期的性能衰减曲线。在新能源汽车电池包缓冲测试中,该技术成功识别出0.15mm的装配高度偏差,避免因微观应力集中导致的电解液泄漏风险。
智能化检测实施流程
项目实施包含三阶段标准化作业:首先配置16组激光位移传感器构建检测阵列,通过基准平面校准实现±0.02mm定位精度;其次利用运动控制系统模拟0-50Hz振动环境,同步采集缓冲垫的三维形变数据;最终通过边缘计算终端进行精密缓冲组件形变分析,生成包含峰值应力、回弹速率等12项参数的检测报告。某半导体设备制造商应用该方案后,缓冲垫质检效率提升400%,人工复核工作量减少82%。
行业应用创新实践
在工业减震系统失效预警领域,该技术已形成典型应用范式。某国际汽车品牌在冲压生产线部署检测系统后,实现缓冲垫寿命预测准确率从78%提升至95%。更值得关注的是,在锂电池生产设备领域,系统通过持续监测缓冲垫高度变化,提前42小时预警模组装配压力异常,避免价值千万的极片辊压机重大损坏。据项目应用数据显示,采用在线检测方案的企业年度设备维护成本平均降低37%。
全链条质量保障体系
为确保检测数据的绝对可靠性,项目构建了四级质量管控机制:设备端配备自清洁光学防护罩,保证在油污环境下的测量稳定性;算法层面嵌入动态补偿模型,消除环境温湿度波动造成的测量误差;数据管理系统通过区块链技术实现检测记录不可篡改;最终由 认证实验室进行季度设备标定。这套体系使检测系统在连续72小时运行工况下,仍能保持0.01mm的测量精度。
技术升级与应用展望
建议行业从三个维度深化技术创新:首先开发基于数字孪生的缓冲系统仿真平台,实现虚拟调试与物理检测的深度融合;其次推进多物理场耦合分析技术,同步监测温度、湿度对缓冲性能的影响;最后建立行业级缓冲元件健康度评价体系,制定统一的工业减震系统失效预警标准。预计到2026年,智能检测技术可使高端装备缓冲系统MTBF(平均无故障时间)延长至18000小时,为智能制造提供更坚实的安全保障。
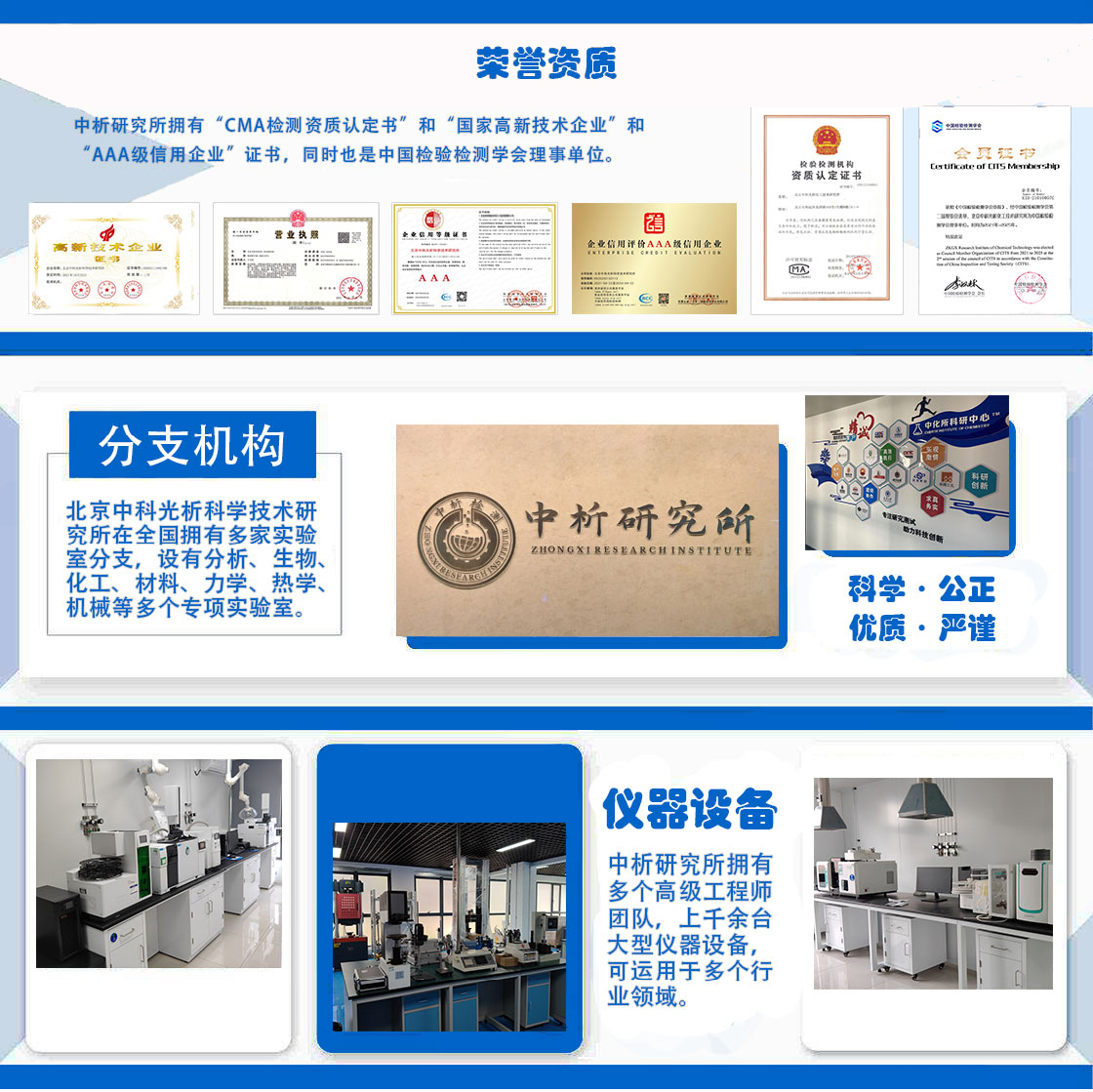
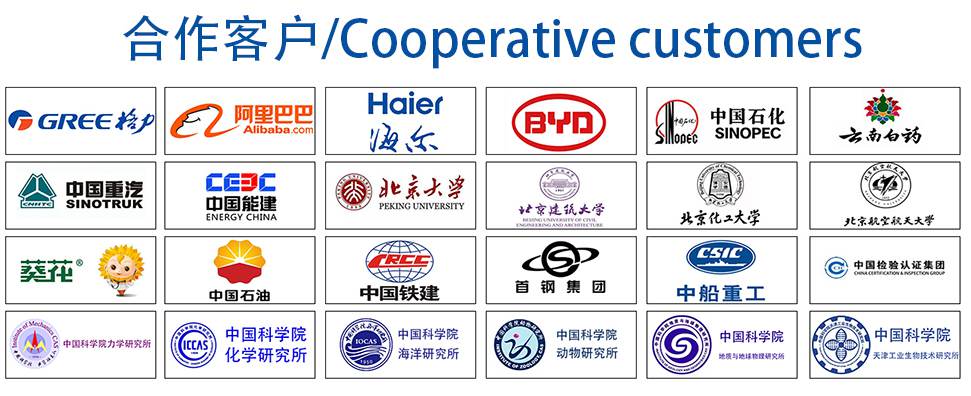