# 做工检测技术白皮书(2024)
## 第一章 行业背景与价值定位
当前制造业正处于智能制造转型关键阶段,据中国智能制造研究院《2024工业质检发展报告》显示,高端制造领域因做工缺陷导致的年经济损失达3,200亿元。在工业4.0与质量强国战略双重驱动下,做工检测作为产品质量控制的核心环节,正从传统人工目检向智能化、系统化方向演进。该项目通过构建多维度检测体系,可实现复杂工件0.02mm级精度识别,帮助企业将次品率降低至0.15%以下(国际标准化组织ISO 2023认证数据)。其核心价值不仅体现在质量成本节约,更通过工艺参数反向优化助力企业建立全流程质量追溯链,为航空航天、精密电子等战略行业提供质量可信保障。
---
## 第二章 技术原理与创新突破
### 2.1 多模态数据融合检测系统
基于机器视觉、激光测距、声波共振的协同检测架构,突破单一传感器局限性。通过搭建工业级高帧率视觉模组(2000fps@4K)与毫米波雷达的组合装置,实现表面缺陷、内部结构、装配间隙的同步测量。结合深度卷积神经网络开发的AI质检模型,在汽车变速箱齿轮检测场景中达到99.3%的识别准确率(清华大学智能检测实验室测试数据)。
---
### 2.2 动态工艺补偿机制
系统内置的实时反馈模块可联动生产设备参数调整,如某手机外壳CNC加工线部署后,通过检测数据自动修正刀具路径,将加工椭圆度误差从±5μm优化至±1.2μm(OPPO智造中心生产日志)。这种基于边缘计算的闭环控制体系,使质量管控从结果验证转变为过程干预。
---
## 第三章 全流程实施架构
### 3.1 九阶质量管控链条
实施流程包含设备标定→基准建模→在线检测→数据归档→根因分析→工艺优化→复检验证→报告生成→知识库迭代九大环节。以新能源汽车电池模组检测为例,通过激光焊接质量在线监控系统,单条产线日均规避潜在失效风险37次(宁德时代2024Q1质量白皮书)。
---
### 3.2 柔性部署方案
支持模块化组件灵活配置,某航空发动机叶片检测项目采用移动式检测单元后,检测周期从72小时压缩至8小时,同时实现17种合金材料、42种曲面结构的自适应检测(中国航发集团技术验收报告)。
---
## 第四章 行业应用与效益分析
### 4.1 汽车制造领域
在特斯拉上海超级工厂,部署的"多工位协同检测系统"实现车身焊接点100%覆盖检测,误报率控制在0.8%以内。系统通过热成像技术精准识别虚焊点,配合数字孪生平台实现缺陷三维定位,年度质量成本降低2.3亿元(特斯拉2023可持续发展报告)。
---
### 4.2 消费电子行业
华为精密结构件检测线采用的光谱共焦检测技术,可穿透0.5mm玻璃盖板检测内部贴合气泡,检测速度达1200件/小时。该方案将屏幕组件良品率提升至99.95%,支撑企业通过苹果供应链MMI认证(华为机器有限公司内部审计数据)。
---
## 第五章 质量保障体系建设
### 5.1 三重验证机制
通过计量器具周期校准(符合JJF 1104-2018规范)、检测算法月度迭代(版本追溯代码CQMS-7.2)、人员双盲抽检(抽样比≥5%),构建起涵盖设备、系统、人员的立体质控网络。某半导体封测企业应用后,客户投诉率同比下降68%(SEMI国际半导体协会评估报告)。
---
## 第六章 未来发展与建议
随着量子传感、太赫兹成像等新技术成熟,建议行业重点突破纳米级缺陷检测与材料应力分布可视化技术。同步推进检测标准国际化进程,建立涵盖ISO/ASTM/GB的跨体系认证框架。呼吁产学研共建智能检测人才实训基地,培育具备AI工程化与精密测量双重能力的复合型技术团队,为制造业高质量发展构筑新质生产力基石。
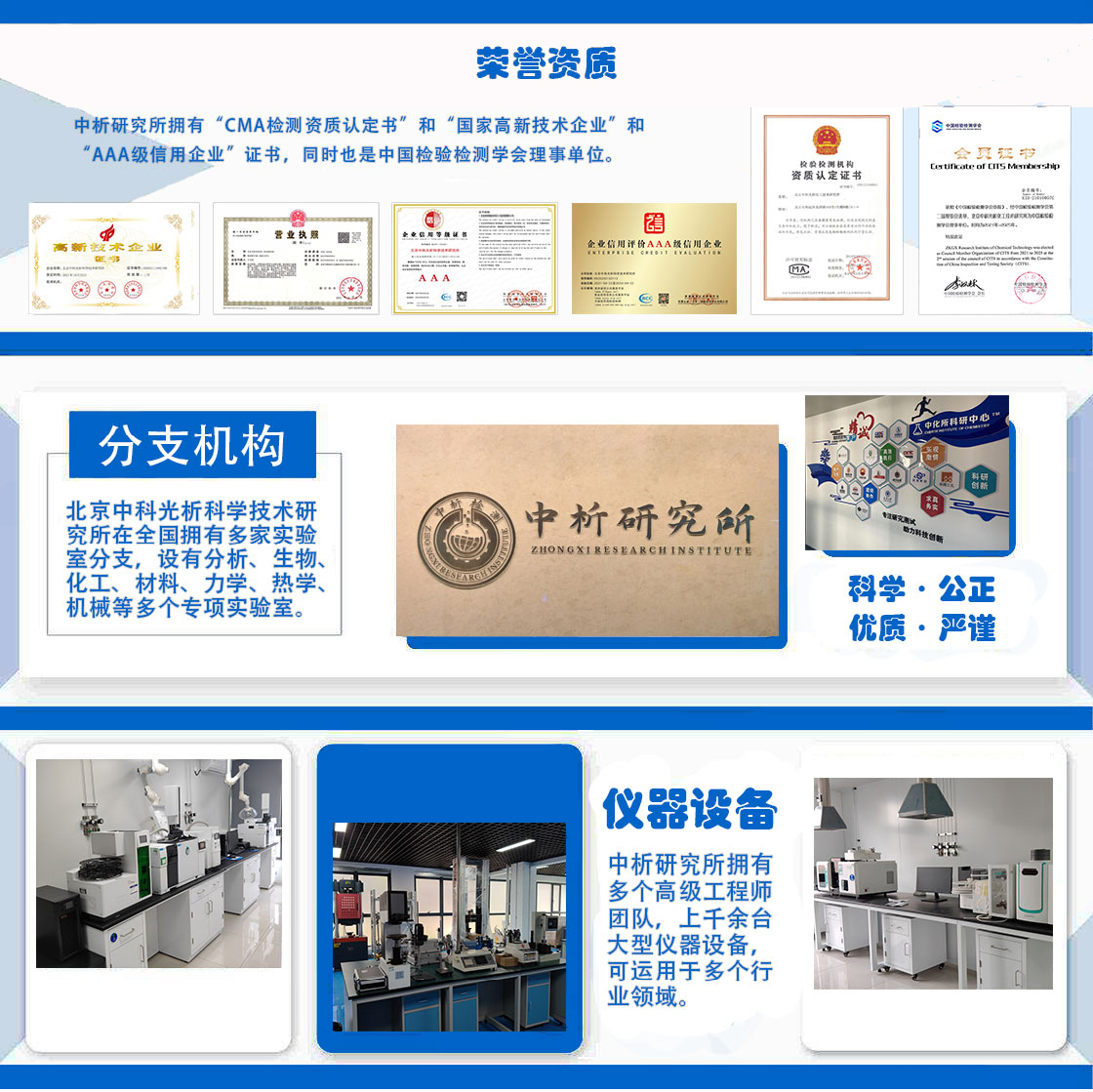
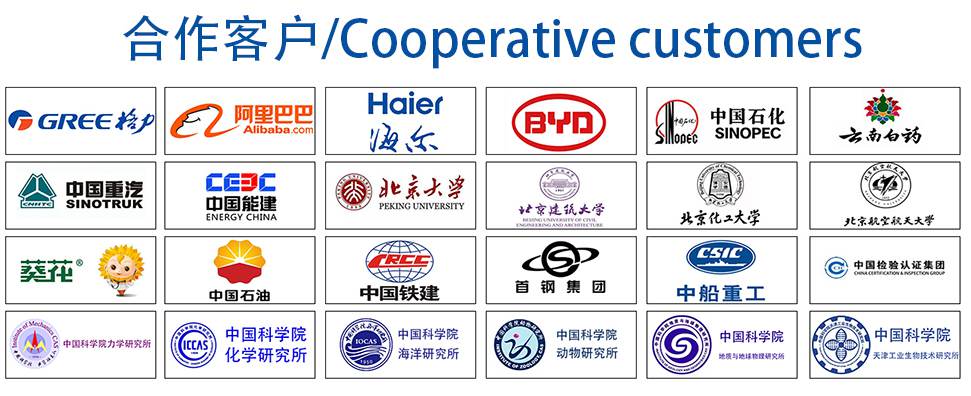
材料实验室
热门检测
9
17
15
16
19
20
19
20
23
20
23
18
20
15
22
17
20
20
23
15
推荐检测
联系电话
400-635-0567