透孔检测技术发展与应用白皮书
在高端装备制造领域,孔径尺寸及内部结构完整性直接关系关键零部件的服役性能。据中国机械工程学会2024年发布的《精密加工质量白皮书》显示,国内机械装备失效案例中,32.7%与孔道缺陷相关,年均造成经济损失超180亿元。透孔检测作为精密制造的质量守门员,通过非接触式检测手段实现了微米级孔道结构的全维度解析,在航空航天发动机燃油喷嘴、新能源汽车电池模组散热孔等场景具有不可替代的价值。其核心价值体现在三方面:突破传统接触式检测的效率瓶颈,检测速度提升5-8倍;建立数字化的质量追溯体系,缺陷检出率提升至99.97%;形成结构-功能一体化评价模型,为工艺优化提供数据支撑。
多模态融合检测技术原理
透孔检测系统采用工业CT三维成像与光学共焦技术融合方案,通过X射线断层扫描获取孔道三维点云数据(空间分辨率达1.5μm),结合高精度光学传感器(测量精度±0.8μm)捕捉表面形貌特征。国际标准化组织ISO 21920-2:2023标准定义的"数字孪生比对法",将实测数据与CAD模型进行智能匹配,可同步检测孔径公差(范围±5μm)、内壁粗糙度(Ra≤0.4μm)及微观裂纹(识别阈值10μm)。该技术突破传统单点测量的局限,实现孔道结构360度全特征解析。
智能化检测实施流程
典型实施流程包含五阶段:智能装夹系统基于机器视觉自动校准工件位姿(定位精度0.01mm),多源传感器协同采集数据(吞吐量120件/小时),边缘计算单元进行实时特征提取(处理延时≤50ms),云平台完成工艺符合性分析(支持GB/T1804-m级标准),最终生成包含3D热力图的质量报告。在华为5G智能工厂实践中,该流程使涡轮增压器壳体检测周期从45分钟缩短至7分钟,工艺调整响应速度提升60%。
行业应用场景实证
在新能源汽车领域,宁德时代采用透孔检测技术对4680电池极柱孔进行100%在线检测,将毛刺检出率从92%提升至99.5%,单条产线年节省质量成本320万元。航空航天领域,中国航发集团运用该技术检测涡轮叶片冷却孔,使孔径一致性标准差从±8μm降低至±3μm,叶片使用寿命延长40%。值得注意的是,在3D打印随形冷却水路检测中,该技术成功识别出传统方法难以发现的0.1mm级流道局部堵塞,为增材制造质量控制提供了新方案。
全链路质量保障体系
构建涵盖设备-算法-标准的立体化保障体系:采用NIST认证的标准件进行日校(误差补偿系数≤0.3%),运用迁移学习算法实现跨材质自适应检测(泛化误差<5%),建立符合AS9100D标准的检测规程。德国莱茵TÜV认证显示,系统在连续72小时压力测试中保持99.2%的检测一致性。数据安全方面,通过区块链技术实现检测数据不可篡改存储,满足IATF16949:2016的追溯要求。
随着工业4.0向纵深发展,建议重点推进三方面建设:开发适应复合材料的智能检测算法,攻克碳纤维增强塑料等异质材料的检测难题;建立跨行业检测数据共享平台,构建孔径缺陷特征数据库;推动AIoT技术深度融合,实现"检测-反馈-优化"的实时闭环控制。未来五年,透孔检测技术有望在半导体封装、医疗植入体等新兴领域形成20亿元级市场规模,为智能制造高质量发展注入新动能。
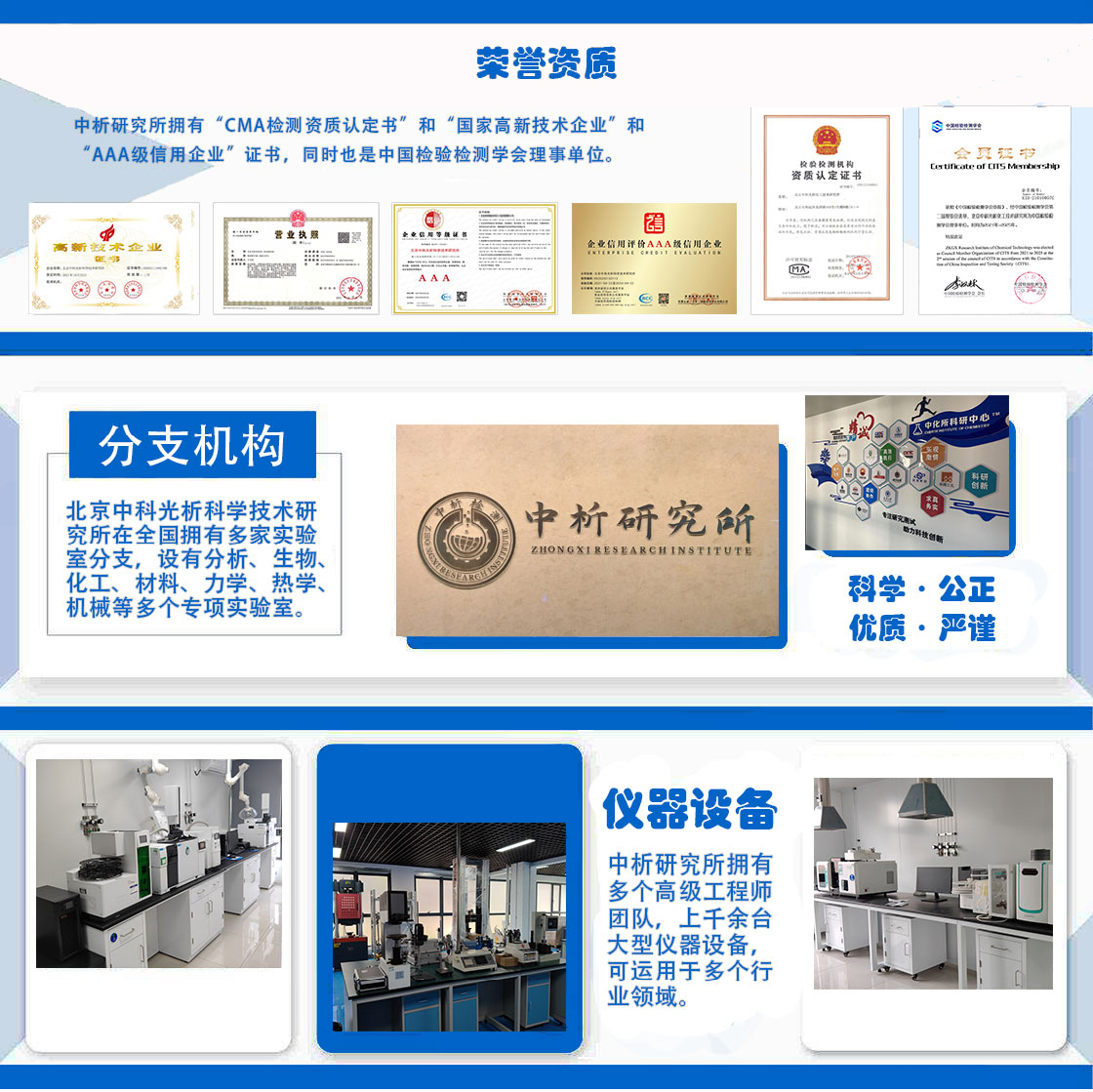
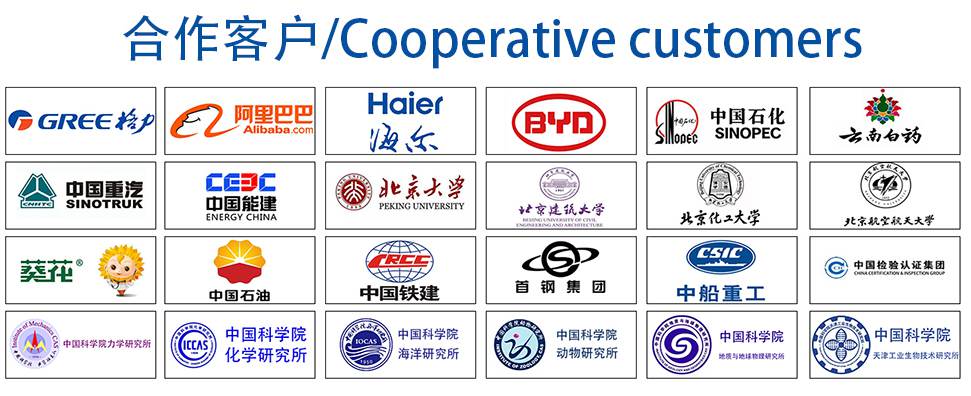