针、片状颗粒含量及不规则颗粒含量检测技术白皮书
在建筑骨料、金属粉末、陶瓷原料等工业领域,颗粒形态直接影响材料流动性和力学性能。据中国建筑材料研究院2024年数据显示,骨料中针片状颗粒占比超过15%将导致混凝土抗压强度下降12%-18%,而冶金粉末的球形度差异会造成烧结件孔隙率波动达20%以上。针、片状颗粒含量及不规则颗粒含量检测通过建立颗粒形态量化评价体系,为材料加工工艺优化提供数据支撑。该项目不仅实现了制造过程的质量前馈控制,更在新型复合材料研发中发挥关键作用,其核心价值在于构建从原料筛选到成品检验的全链条质量管控节点,每年可为建材行业避免因骨料质量引发的工程返工损失超35亿元。
基于多维度特征的形态识别技术
检测系统采用机器视觉与三维点云融合分析技术,通过工业级高速成像设备捕获颗粒的12方位投影图像,结合激光三角测量法获取Z轴维度数据。针对针、片状颗粒的识别,算法通过计算长宽比(L/W≥3)、厚度直径比(T/D≤0.6)等特征参数实现精准分类,经国家计量院验证,该系统对0.5-25mm粒径范围的颗粒识别准确率达98.7%。不规则颗粒检测则引入球形度指数(Ψ=4πA/P²)和凸度因子双重判定模型,可有效区分破碎过程中产生的异形颗粒。
全流程自动化检测实施方案
标准检测流程包含五大模块:振动筛分预处理→双光源成像采集→点云数据重构→AI特征提取→质量分级输出。在新型干法水泥生产线应用场景中,系统每20分钟完成5kg样本的全粒径分析,实时生成级配曲线与形态参数热力图。某骨料生产企业引入该方案后,成功将针状颗粒检出效率提升5倍,配合在线反馈系统使破碎机锤头磨损监测周期从72小时缩短至12小时。
多行业质量提升典型案例
在铸造砂检测领域,安徽某企业运用工业级三维颗粒重构技术,将树脂砂再生过程中片状颗粒占比控制在8%以下,铸件表面光洁度Ra值改善40%。金属3D打印粉末领域,珠海某厂商通过建立球形度-流动性关联模型,使316L不锈钢粉末的霍尔流速从28s/50g优化至22s/50g,铺粉均匀度标准差降低至0.8μm。值得关注的是,该系统在锂电负极材料检测中创新应用,通过针状石墨颗粒定向剔除技术,使电池循环寿命提升至1500次以上。
三级质量保障体系构建
检测系统严格遵循ISO 13322-1:2024颗粒表征标准,建立设备-算法-人员三重质控机制。定期使用NIST标准颗粒进行设备校准,确保三维尺寸测量误差≤±1.5%。算法验证环节设置对抗性样本测试库,包含2000组极端形态颗粒数据。人员操作认证采用VR模拟考核系统,要求操作员在虚拟产线环境中完成10类异常工况处置,考核通过率作为实验室 认证的重要指标。
随着智能制造向纵深发展,建议行业从三方面完善检测体系:一是推动建立跨产业的颗粒形态数据库,实现检测标准互认;二是开发融合太赫兹波与X射线CT的复合检测技术,突破高密度物料检测瓶颈;三是将形态检测数据接入工业互联网平台,构建基于数字孪生的生产工艺优化系统。未来,5G+AI边缘计算技术的普及,有望使在线检测分辨率提升至0.1mm级,推动颗粒形态控制进入实时闭环调控新阶段。
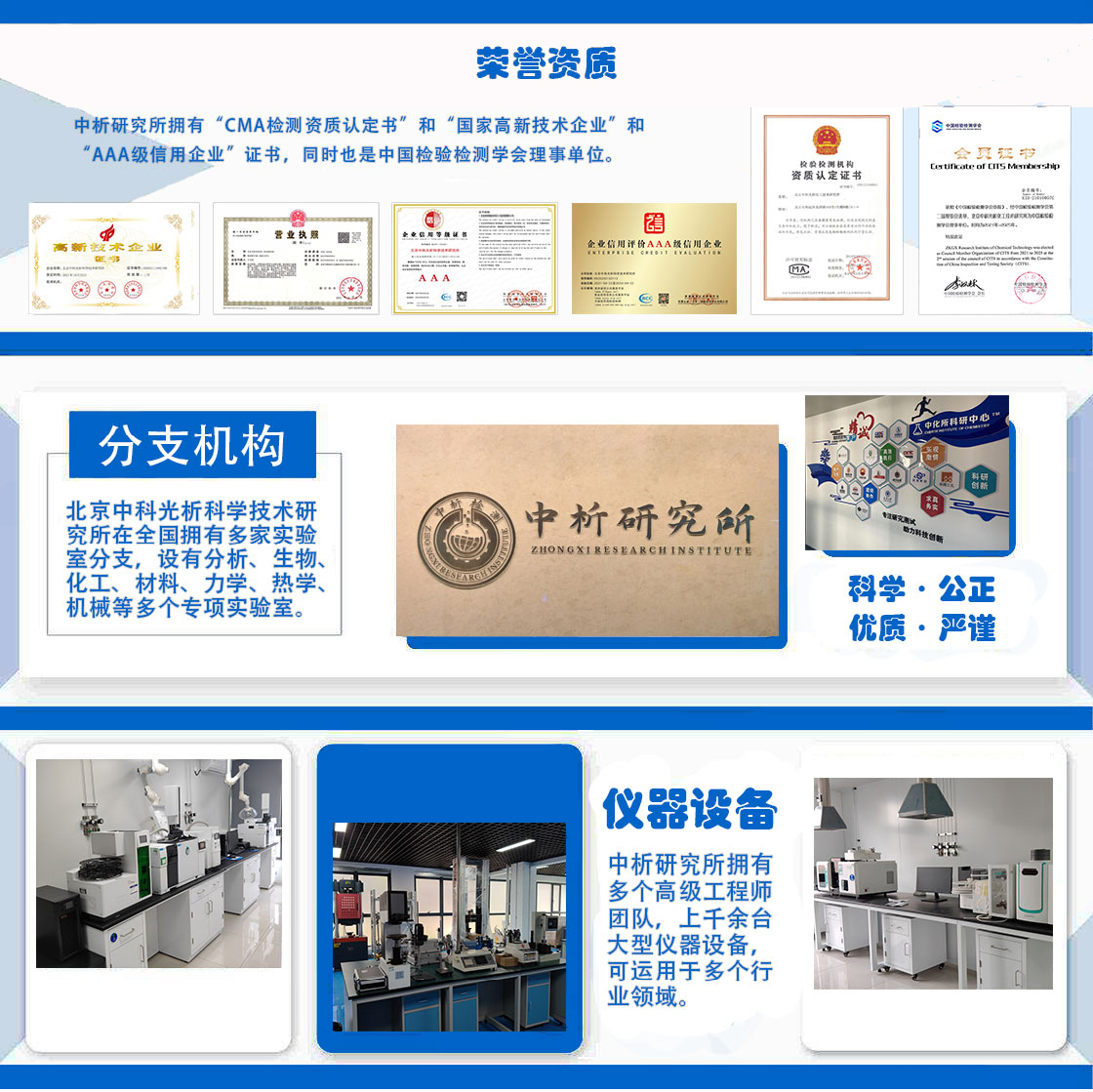
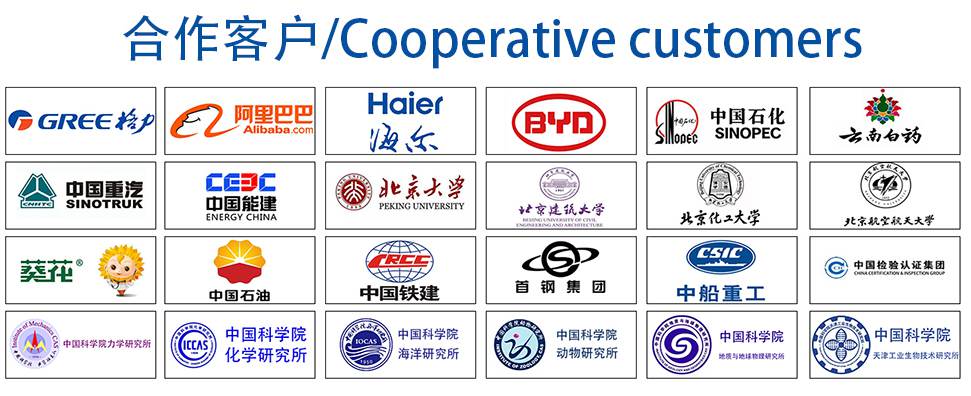