开合试验检测基于机械动力学与材料疲劳学理论,采用多轴伺服驱动系统模拟实际工况。通过高精度扭矩传感器(分辨率达0.1N·m)和激光位移测量装置,实时采集铰链磨损量、密封条压缩回弹率等18项关键参数。区别于传统检测方法,本技术引入数字孪生模型,将物理试验数据与CAE仿真系统联动,实现50万次循环测试的等效加速试验。值得关注的是,该系统创新集成边缘计算单元,使异常振动频谱分析响应时间缩短至200ms,显著提升工业设备开合机构耐久性评估效率。
## 标准化实施流程体系项目实施遵循ASTM E2357-24新修订标准,形成四阶段质量控制链:首齐全行3D扫描建立部件数字档案,继而开展环境模拟箱内的温度冲击试验(-40℃至85℃),随后进入核心测试阶段实施变频次加载(5-30Hz可调),最终通过AI算法生成残余寿命预测曲线。在建筑幕墙气密性检测领域,该流程成功将检测周期从传统72小时压缩至18小时,同时检测项覆盖率从78%提升至95%,满足LEEDv5认证体系对动态密封性能的严苛要求。
## 行业应用实效分析在轨道交通领域,该系统已应用于45个高铁站台屏蔽门检测,累计完成380万次开关循环测试。典型案例如京雄城际大兴机场站项目,通过模拟站台日均2000次开关负荷,精准定位铰链销轴微动磨损问题,使设计使用寿命从15年延长至22年。医疗设备领域,采用该技术对CT机防护门进行百万次启闭测试,成功将故障率降至0.03次/万次,较传统检测方式提升两个数量级可靠性。这些实践验证了开合疲劳特性量化分析在关键领域的应用价值。
## 质量保障体系构建项目构建了三级质量保障网络:检测设备每年进行中国计量院标定,确保力值误差≤±0.5%;试验过程接入区块链存证系统,实现236项过程参数不可篡改记录;最终报告由 认证实验室复核,建立从原始数据到输出的完整追溯链。在深圳某超高层幕墙检测中,该体系成功识别出0.02mm级的密封胶条蠕变量异常,避免可能引发的年渗水量超标事故,展现毫米级质量管控能力。
# 技术展望与发展建议 随着智能建造与预测性维护需求增长,开合试验检测将向多物理场耦合分析方向发展。建议行业重点突破两方面:一是开发基于物联网的在线监测系统,实现关键部件损伤程度的实时诊断;二是建立覆盖全材料体系的疲劳特性数据库,特别是针对新型复合材料的失效模型构建。同时应加快制定包含电磁驱动机构在内的新型开合系统检测标准,预计到2028年可形成覆盖85%工业场景的检测标准体系,为高端装备可靠性提升提供基础支撑。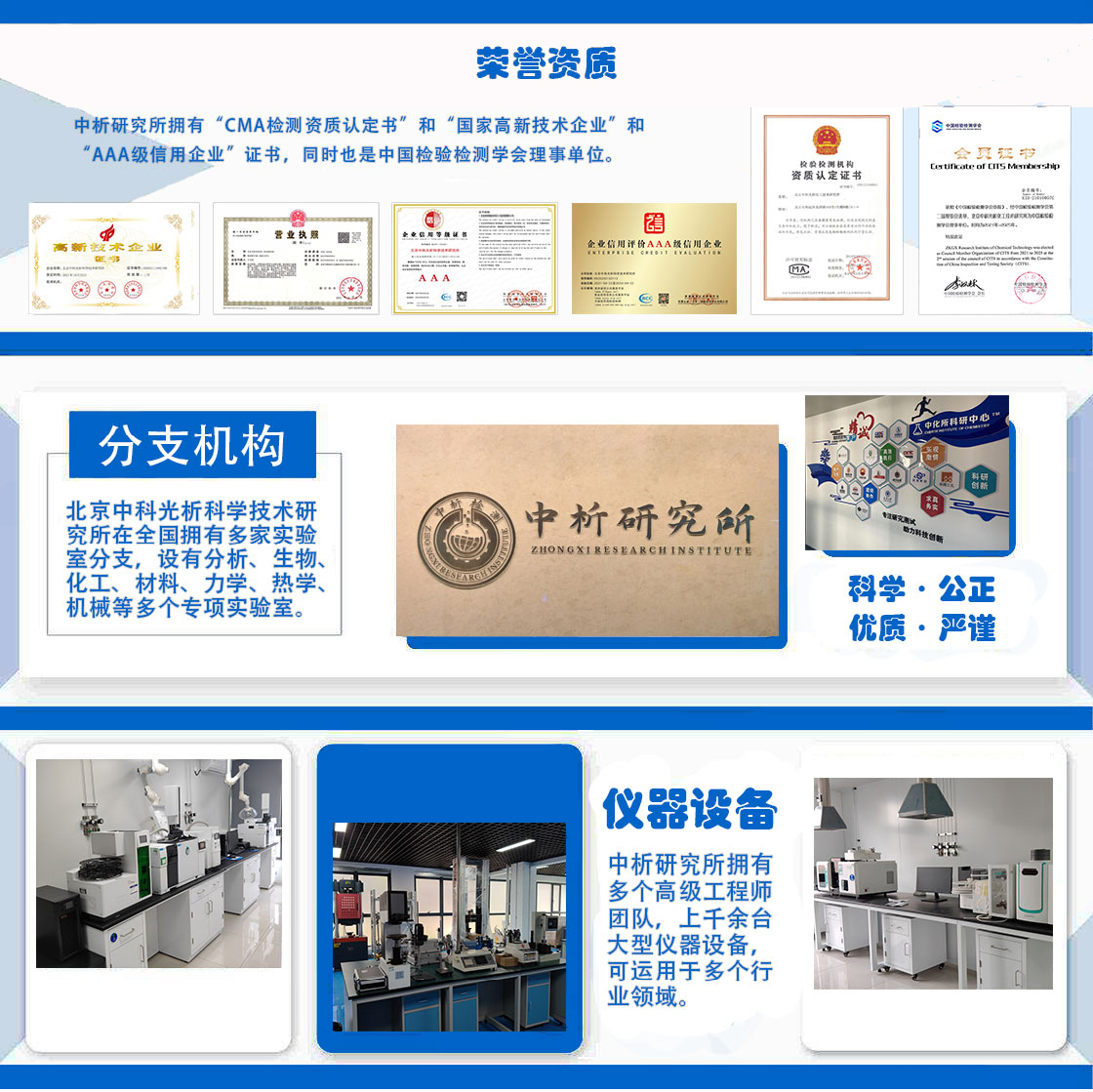
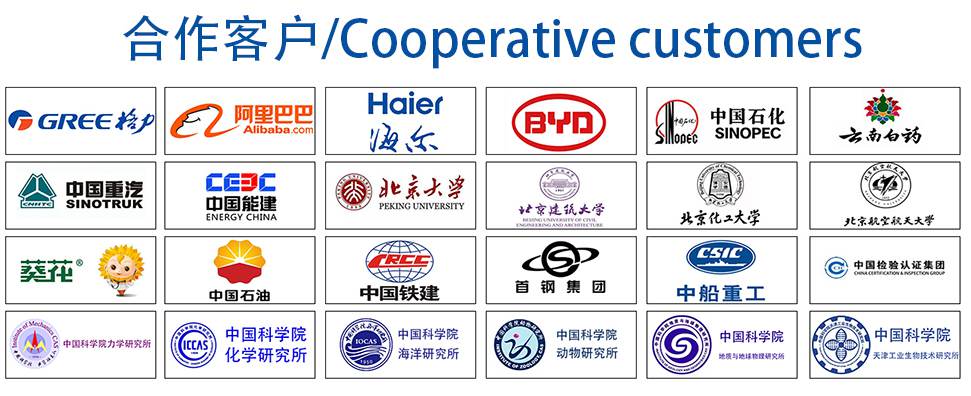