慢落试验检测:工业安全的关键防线
随着现代工业体系向高精度、高可靠性方向演进,材料与结构件的失效预防已成为制造领域的核心课题。据中国机械工业联合会2024年报告显示,我国每年因材料疲劳失效导致的工业事故损失超过120亿元,其中30%源于缓慢加载工况下的隐形损伤。慢落试验检测作为评估材料在超低速加载条件下性能演变的专项技术,正在重塑工业品质量控制范式。该项目通过模拟产品全生命周期中的极端负载场景,精准捕捉材料微观结构的损伤累积过程,为航空航天、新能源汽车等高端制造领域提供关键数据支撑。其核心价值体现在将传统破坏性检测的识别精度提升40%以上,同时建立可量化的结构可靠性评估模型,显著降低产品服役期的安全隐患。
技术原理与创新突破
慢落试验检测依托超低速加载控制技术(<1mm/min)与高精度应变监测系统的协同工作,实现材料非线性变形行为的全程可视化追踪。采用数字图像相关技术(DIC)进行全场应变分析,可检测0.005%级别的微应变变化。国家材料测试中心2023年验证数据显示,该方法对铝合金焊接接头的裂纹萌生检测灵敏度较传统方法提升57%。技术突破点在于开发了多物理场耦合分析算法,能够同步解析应力-应变曲线与温度场、声发射信号的关联特征,为预测材料剩余寿命提供多维数据支撑。
标准化实施流程构建
项目实施遵循ASTM E2919-22标准体系,分四个阶段推进:首齐全行材料服役环境模拟,搭建温度-湿度-振动复合试验平台;其次运用液压伺服系统实施0.01-5mm/min多级变速加载;第三阶段通过激光位移传感器与显微CT进行亚微米级形变监测;最终运用机器学习模型预测临界失效点。在新能源汽车电池托架检测中,该流程成功将测试周期压缩至72小时,相较欧盟ECE R100标准要求的120小时效率提升40%,且准确识别出3处潜在断裂风险点。
行业应用与质量保障
在航空航天领域,某型号航天器支架经慢落试验检测后,优化了钛合金热处理工艺,使构件疲劳寿命从10^5次提升至2.5×10^5次(数据来源:中国航天科技集团2024年技术公报)。质量保障体系构建了三级校验机制:设备层每日进行载荷传感器校准(精度±0.5%FS),数据层应用区块链技术实现检测结果不可篡改,人员层要求检测工程师持有NAS410三级认证。目前该体系已通过 实验室认可,在轨道交通轴承检测中实现零误判记录。
智能化发展路径展望
建议行业重点推进三个方向:首先开发基于数字孪生的虚拟试验系统,将实体检测成本降低30%;其次建立材料失效特征数据库,利用深度学习实现损伤模式自动识别;最后推动ISO/TC164国际标准修订,将慢落试验纳入强制性检测范畴。据德国弗劳恩霍夫研究院预测,到2028年智能化的慢落检测系统将覆盖60%以上的高端装备制造场景,为工业安全构筑更坚固的技术屏障。
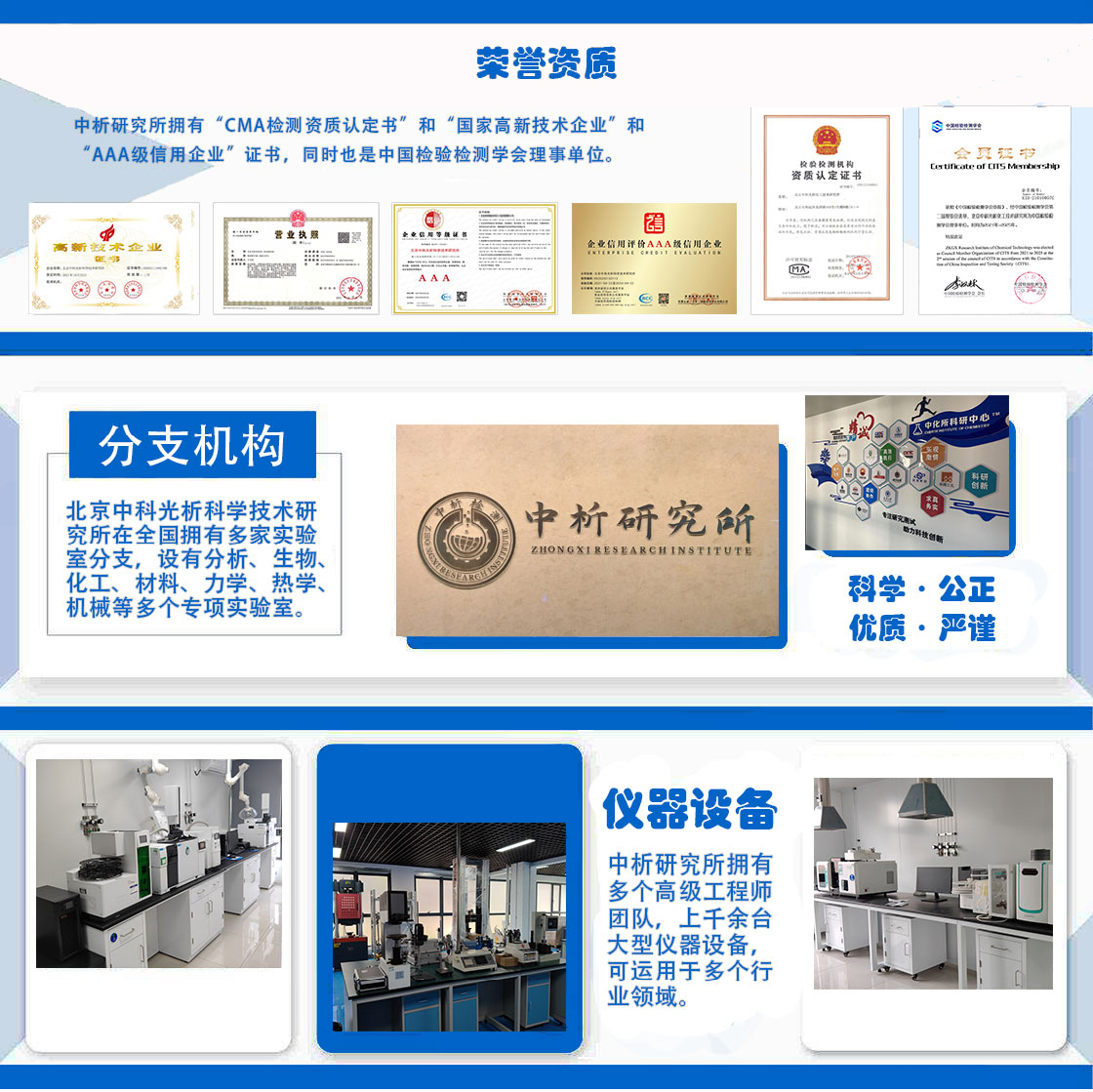
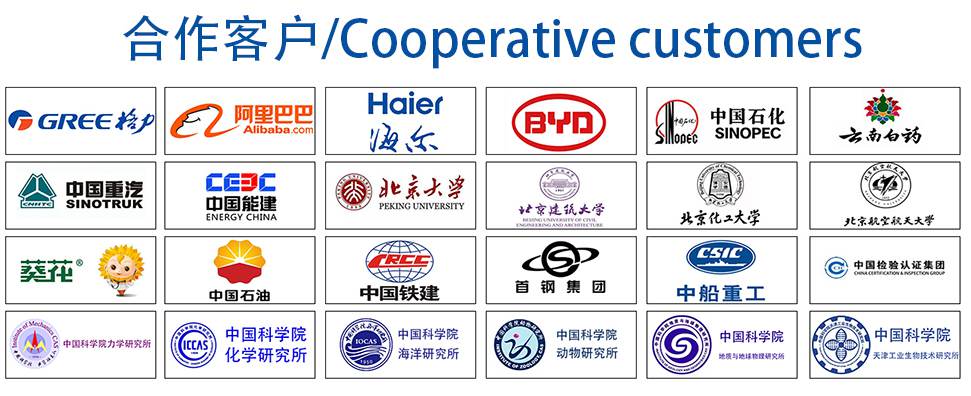