道路车辆汽车电缆检测技术发展与应用白皮书
随着新能源汽车渗透率突破35%(中国汽车工业协会,2024),车载电子电气架构复杂度呈指数级增长。在智能网联技术驱动下,单车线束长度已超过5千米,高压电缆系统承载功率最高达800V/400kW。汽车电缆检测作为车辆安全的核心保障环节,直接影响着高压漏电防护、信号传输保真及系统电磁兼容等关键性能。该项目通过构建全周期质量监控体系,可降低车辆电气故障率62%(TÜV南德2023年报),其核心价值在于突破"线束失效前兆识别"和"极端工况模拟验证"两大技术瓶颈,为智能电动汽车安全运行构筑底层技术防线。
多维度检测技术体系构建
基于ISO 19642:2023道路车辆电缆标准,检测系统集成电气性能、机械强度、环境适应性三类核心指标。高压导线检测采用脉冲电压试验(5kV/100μs)叠加温升监测,可精准定位绝缘层微观缺陷。针对新能源车辆电缆老化测试,开发85℃/95%RH湿热循环加速试验装置,实现3000小时等效10年使用寿命验证。值得关注的是,车载以太网电缆需通过1GHz带宽下的眼图测试,确保ADAS系统信号误码率低于10^-12。
全流程标准化作业规程
项目实施采用VDA 6.3过程审核标准,形成从原料入场到整车集成的四阶管控模型。在蔚来汽车合肥工厂的实践中,建立包含23道检测工序的质量门:原料阶段进行导体直流电阻测试(精度±0.5%),线束组装后实施500N轴向拉力试验,总装环节完成整车级CANFD总线抗干扰测试。据中国汽车工程研究院实测,该体系使线束装配直通率从92.4%提升至97.8%。
行业典型应用场景分析
在比亚迪e平台3.0高压线束项目中,检测系统成功识别出绝缘材料热收缩率异常问题,避免可能的大规模召回风险。特斯拉上海超级工厂通过引入AI视觉检测设备,实现0.02mm精度的连接器针脚缺陷检测,误判率控制在0.3%以下。针对高寒地区工况,一汽红旗H9在-40℃环境仓完成线束弯曲刚度测试,确保冬季极端条件下的信号传输稳定性。
智能化质量保障体系创新
行业领先企业已构建"端-边-云"协同检测网络:终端部署工业CT进行三维结构分析,边缘计算节点处理实时监测数据,云平台运用机器学习预测线束失效模式。博世苏州实验室的实践表明,该体系可将故障预警时间提前1500小时。同时,基于区块链技术的检测数据存证系统,已实现全供应链质量追溯,单个零部件检测记录上链时间缩短至0.8秒。
面对智能电动汽车的快速发展,建议行业重点突破三个方向:建立车规级高速数据传输电缆的112Gbps测试能力,开发支持800V高压系统的复合绝缘材料评价体系,构建覆盖-55℃至175℃的超宽温区检测平台。值得强调的是,亟需制定智能线束健康度评估标准,推动预测性维护技术在前装市场的应用落地,为汽车电子电气架构革新提供基础保障。
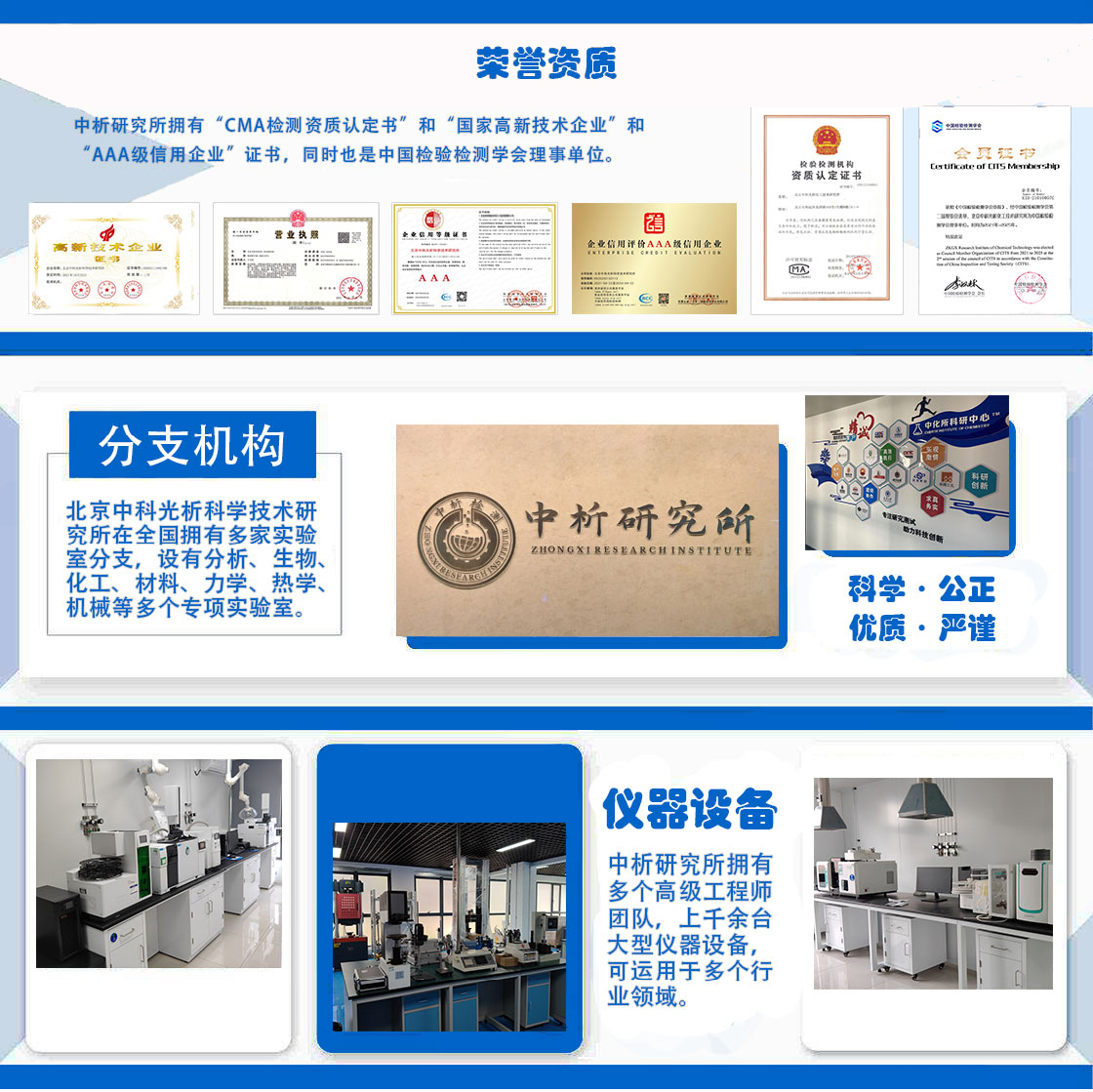
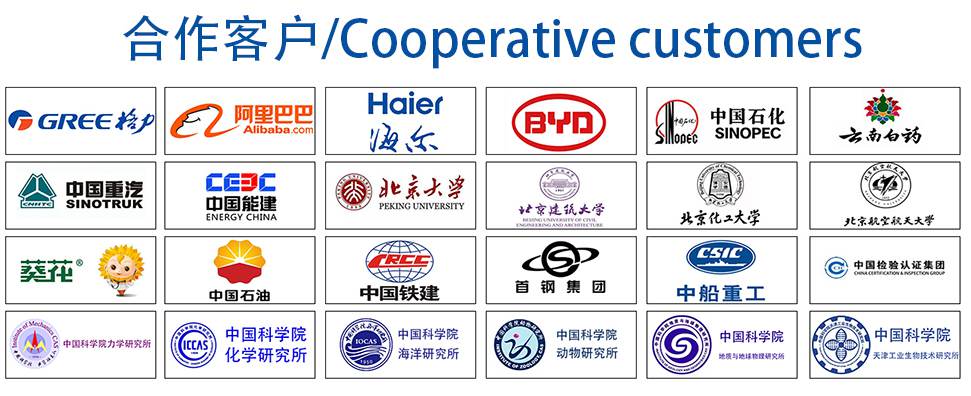