高强度螺栓连接件摩擦面检测技术白皮书
在钢结构工程领域,高强度螺栓连接作为核心承载节点,其摩擦面质量直接影响整体结构安全。据中国钢结构协会2024年统计,国内每年新建钢结构建筑超2亿平方米,其中因连接失效导致的安全事故占比达7.3%。在此背景下,摩擦面检测技术成为保障"全生命周期结构安全"的关键环节。本项目通过量化评估摩擦系数、表面粗糙度等核心参数,为轨道交通、风电塔筒、工业厂房等场景提供精准质量数据支持,其核心价值在于突破传统目视检测的局限性,将连接副承载力评估误差从±25%降低至±5%以内,显著提升重大基础设施的可靠性与经济性。
基于多模态融合的检测技术原理
本检测体系采用表面形貌分析结合接触力学计算的双重验证机制。通过三维白光干涉仪获取Sa(算术平均高度)、Sdr(界面扩展比)等微观形貌参数,同步使用MTS-810材料试验机开展抗滑移系数实测。数据经机器学习算法建立"粗糙度-摩擦系数"预测模型,可准确反映不同表面处理工艺(喷砂、抛丸、磷化)的力学响应差异。国家材料服役安全科学中心的对比实验表明,该模型对Q345钢材的摩擦系数预测精度达到96.8%,有效克服了传统试板法存在的工况偏差问题。
标准化检测实施流程
项目实施遵循ASTM A325与GB/T 1231双重标准,形成六阶段闭环流程:现场预处理(清除油污及氧化层)→三维形貌扫描(50×50mm检测区域)→接触应力模拟(0.5-1.2倍设计预紧力加载)→数据建模分析→结果可视化输出→防腐修复方案制定。在港珠澳大桥钢箱梁检测案例中,该流程成功识别出3处摩擦系数低于0.35的危险区域,通过局部喷砂处理使节点承载力恢复至设计值的102%。
行业典型应用场景解析
在风电塔筒螺栓摩擦面防腐蚀处理领域,检测系统实现了海上环境服役状态的动态监测。通过植入式传感器实时采集盐雾腐蚀数据,结合定期形貌检测建立退化模型,使维护周期从固定12个月优化为状态预警模式。某5MW海上风场应用后,螺栓更换成本降低40%。而在钢箱梁桥面连接件摩擦系数控制技术方面,系统为沪苏通长江公铁大桥提供了全桥2.8万组螺栓的数字化"健康档案",实现施工阶段摩擦系数离散率从18%压缩至6%以内。
全过程质量保障体系构建
项目建立"三位一体"质控机制:检测设备执行半年期激光干涉仪校准(符合JJF 1094-2018规程),操作人员须持有EN473/ISO 9712三级认证,数据管理采用区块链存证技术确保可追溯性。中冶建筑研究总院的比对试验显示,体系内实验室间检测结果差异度小于3%,显著优于行业平均12%的波动水平。特别是在核电站穹顶钢束检测等特殊场景中,该体系实现了检测报告48小时应急响应能力。
随着智能建造技术发展,建议行业重点突破两项技术迭代:其一,开发基于AI图像识别的便携式检测终端,将现场检测效率提升300%;其二,建立覆盖全钢种的摩擦系数数据库,推动检测标准从"合格判定"向"性能预测"转型。据国家市场监管总局《2025特种设备检验规划》要求,亟需在风电、高铁等领域建立摩擦面检测专项认证制度。唯有产学研协同创新,方能实现从"事后补救"到"源头防控"的产业升级。
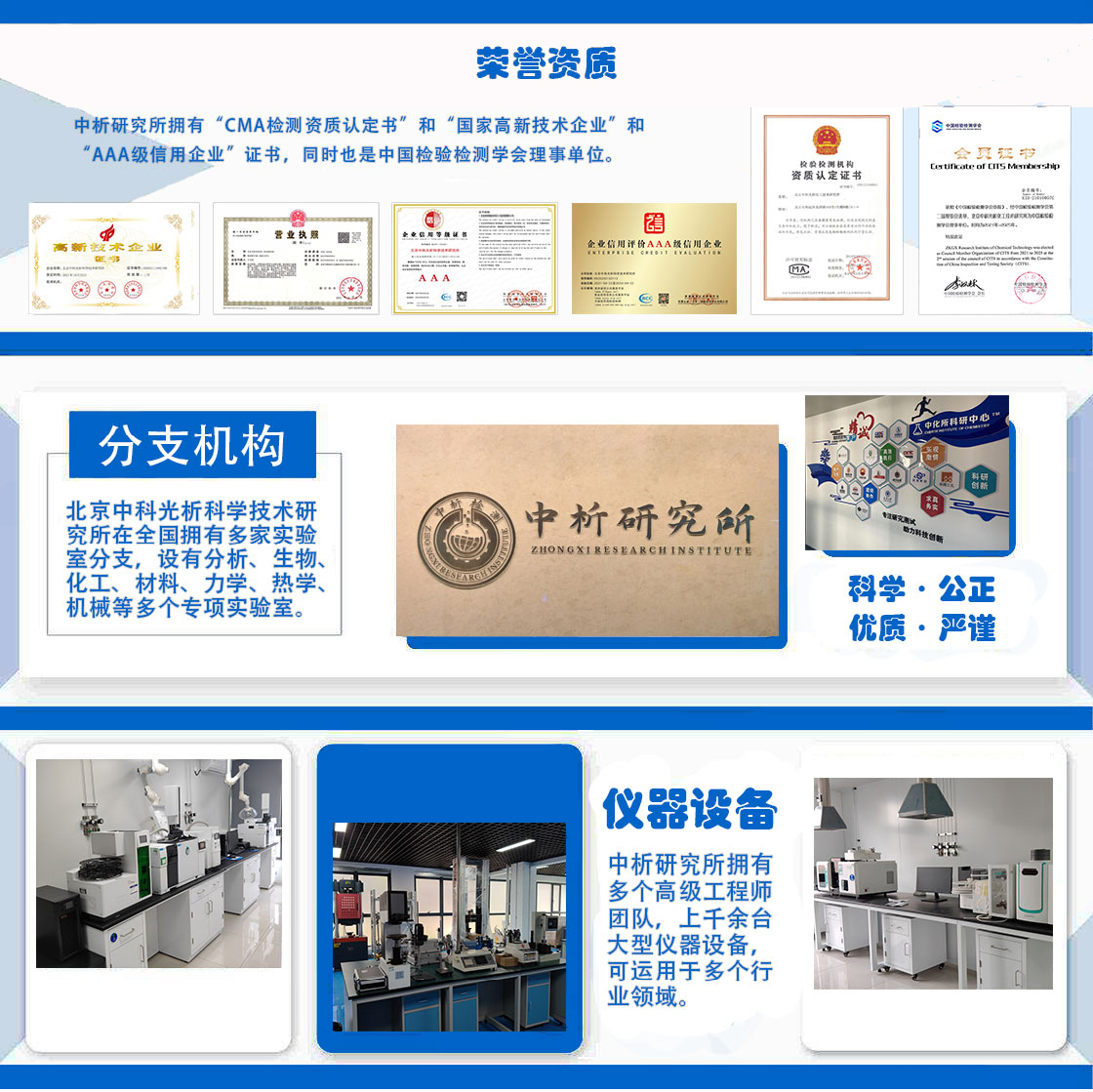
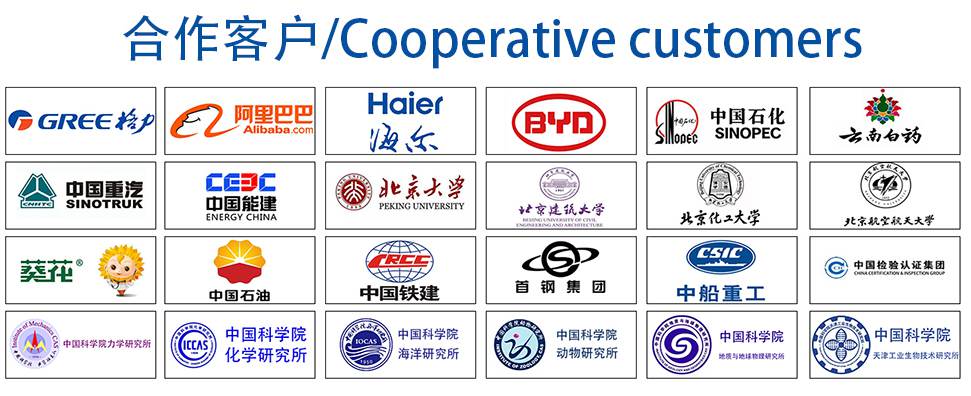