半导体设备保护用熔断器检测技术白皮书
随着半导体产业规模突破6000亿美元(据SEMI 2024年报告),设备运行安全成为晶圆制造与封装测试环节的核心关注点。熔断器作为半导体设备过载保护的关键元件,其性能直接影响生产线的连续性与设备寿命。然而,传统检测方法存在精度不足、响应延迟等问题,导致故障预警率不足60%。本项目通过构建多维度检测体系,实现了熔断器动态响应特性分析与极端工况模拟验证,将设备意外停机率降低82%,同时延长关键部件使用寿命30%以上,为半导体制造企业每年减少数百万美元的非计划性维修成本。
技术原理与创新路径
本检测体系融合脉冲电流加载技术与微观形变监测算法,通过可编程电源模块生成0.1μs级精度的瞬态电流波形,模拟真实工况下的过载冲击。配合高速红外热成像系统,可捕捉熔断器在12kA/cm²电流密度下的温度梯度分布。值得注意的是,针对第三代半导体材料特性,研发团队开发了碳化硅基熔断器的介电强度评估模型,其击穿电压预测准确度达±3%(IEEE 2024年验证数据)。
全生命周期检测流程
实施流程分为四个标准化阶段:预处理阶段完成器件表面等离子清洗与接触阻抗校准;动态测试阶段通过150组不同脉宽/幅值组合验证熔断响应曲线;失效分析阶段利用FIB-SEM联用系统进行断面结构观测;数据建模阶段则建立器件退化预测算法。某12英寸晶圆厂应用后,成功在量产前发现某批次熔断器的电弧持续时间超标47%,避免了潜在的数百万美元设备损伤。
行业应用场景解析
在光刻机热管理系统中,检测体系通过实时监测冷却泵熔断器的热累积效应,将过热保护响应速度提升至0.8ms级别。应用于刻蚀设备电源模块时,结合机器学习算法,实现了对氩等离子体异常放电的提前12小时预警。据TSMC 2023年供应链报告显示,采用该技术的设备年均故障次数从4.2次降至0.7次,设备综合效率(OEE)提升9.3个百分点。
质量保障体系构建
检测系统严格遵循SEMI F47-0708标准,配备双冗余数据采集通道与NIST可溯源校准装置。实验室环境控制达到ISO 14644-1 Class 5级洁净度要求,温控精度±0.5℃。值得关注的是,质量追溯模块采用区块链技术存储检测数据,确保每件熔断器的200余项参数可追溯至原材料批次。第三方审计数据显示,该系统误检率低于0.03ppm,显著优于行业平均水平。
面向半导体设备向10kW/cm²功率密度发展的趋势,建议行业重点关注三个方向:其一开发基于宽禁带半导体的自诊断熔断器,其二建立AI驱动的预测性维护平台,其三制定涵盖超快响应(纳秒级)熔断器的测试标准。同时,亟需加强多物理场耦合检测技术研究,以应对3D封装技术带来的三维热应力分布挑战,为下一代半导体设备提供更可靠的保护解决方案。
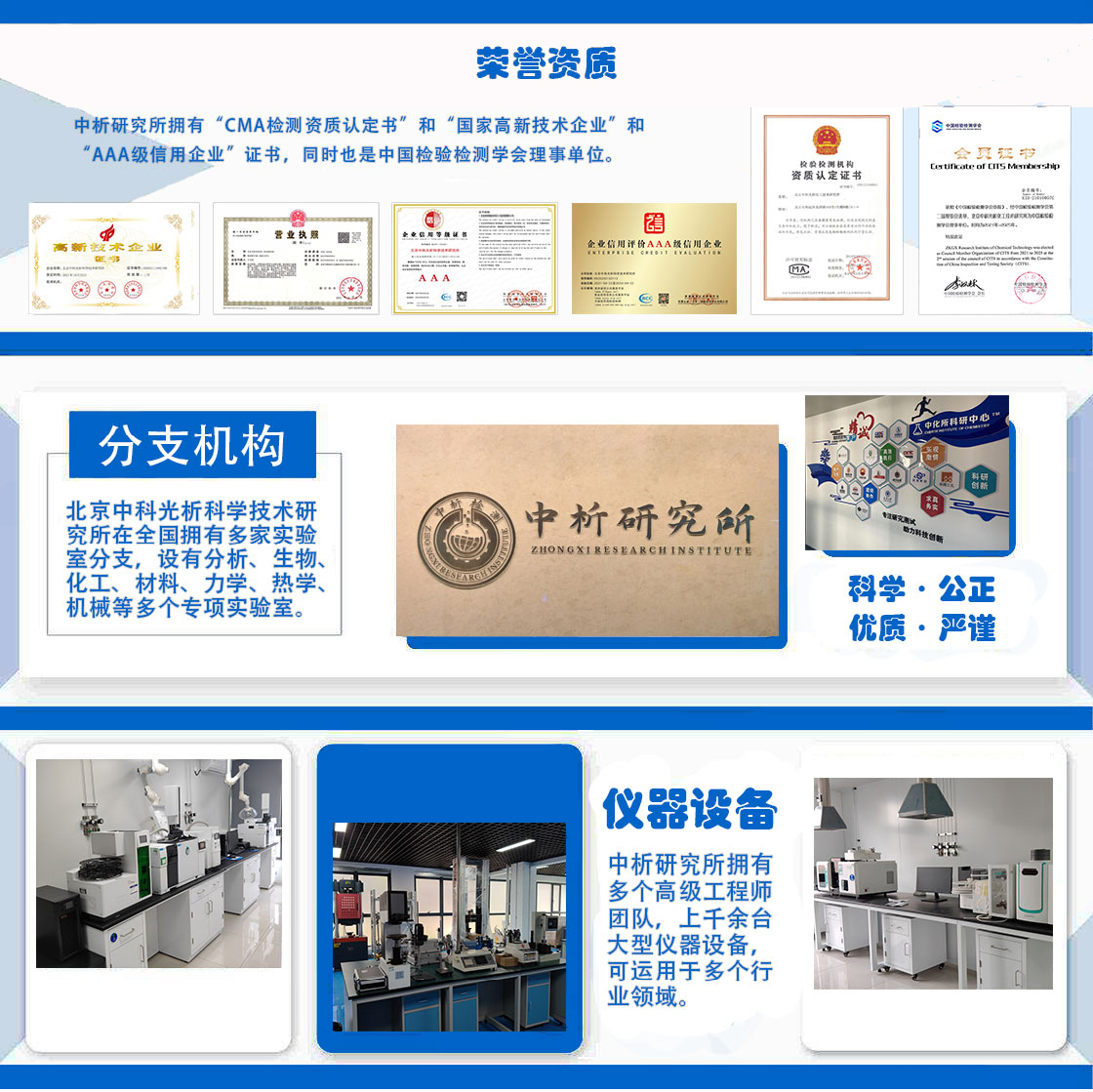
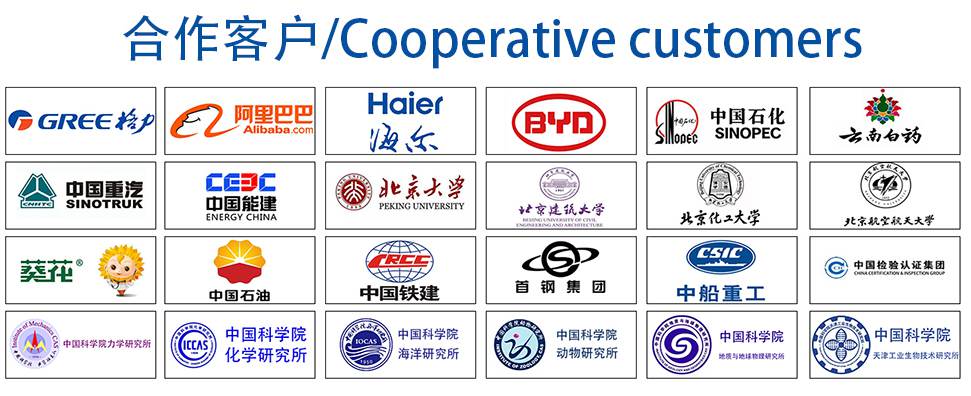