涂料涂层附着力检测:技术演进与行业实践白皮书
在工业制造与建筑装饰领域,涂料涂层的附着力直接影响产品使用寿命与安全性能。据中国建筑材料研究院2024年数据显示,每年因涂层失效导致的直接经济损失超过230亿美元,其中65%的案例源于附着力不足。随着新能源汽车、航空航天等高端制造业的快速发展,涂层体系复杂度显著提升,传统检测方法已难以满足纳米复合涂料、智能响应涂层等新型材料的评估需求。本项目通过构建多尺度附着力检测体系,实现了从宏观剥离强度到微观界面结合的精准量化,其核心价值在于建立覆盖全产业链的质量预警机制,为轨道交通装备防腐涂层、光伏背板耐候涂层等关键领域提供技术保障,有效降低质量事故发生率。
多元检测技术原理体系
现代附着力检测技术已形成力学测试与表征分析的双轨体系。划格法(ASTM D3359)和拉开法(ISO 4624)作为基础评估手段,可量化涂层抗剪切剥离能力,适用于常规工业涂料检测。针对风电叶片涂层耐久性评估等特殊场景,研发人员创新采用声发射监测技术,通过捕捉微米级裂缝扩展信号实现早期失效预警。值得一提的是,国家新材料检测中心2024年报告指出,引入原子力显微镜(AFM)界面结合能分析后,环氧树脂底漆的附着力预测精度提升42%。
标准化实施流程构建
项目执行遵循"环境模拟-分级测试-数据建模"的标准路径。检测前需进行72小时恒温恒湿预处理,模拟汽车电泳涂层质量验证的湿热工况。实施阶段采用三级评估法:初筛使用便携式划痕仪(载荷0-50N),复检应用液压伺服拉力机(精度±0.5%FS),疑难样本则进行聚焦离子束(FIB)断面分析。某轨道交通车辆制造企业的实践表明,该流程使涂层返工率从8.7%降至2.3%,单台车体制造成本节约3800元。
跨行业应用成效分析
在海洋工程防腐领域,项目团队为港珠澳大桥配套研发的阴极剥离检测方案,成功将氯离子渗透预警周期提前600小时。针对光伏行业双面组件边框涂层,开发的多轴应力测试仪可实现±45°倾角下的循环加载,帮助某龙头企业通过TÜV莱茵192小时湿热老化认证。更值得关注的是,该技术在新一代钠离子电池集流体涂层检测中的创新应用,使界面结合强度达到18.7MPa(UL 1642标准要求≥15MPa)。
全链条质量保障机制
项目构建了 认证实验室网络与数字孪生平台的双重保障体系。通过将50组历史检测数据训练成机器学习模型,开发出涂层失效风险预测系统(准确率89.3%)。人员资质方面实行三级认证制度,操作人员需掌握X射线光电子能谱(XPS)界面分析等6项专项技能。某航空发动机企业应用该体系后,高温陶瓷涂层的批次稳定性CPK值从1.12提升至1.67,达到AS9100D航空质量标准要求。
展望未来,建议从三方面推动技术升级:首先建立涂层数据库联盟,整合汽车电泳涂层质量验证等细分领域数据;其次研发基于AI的涂层截面图像自动分析系统,将检测效率提升40%以上;最后推动ASTM/ISO标准中增加新能源涂层专项检测条款。据弗若斯特沙利文预测,到2027年智能检测装备市场规模将突破85亿美元,精准化、数字化的附着力检测技术必将在此进程中发挥核心作用。
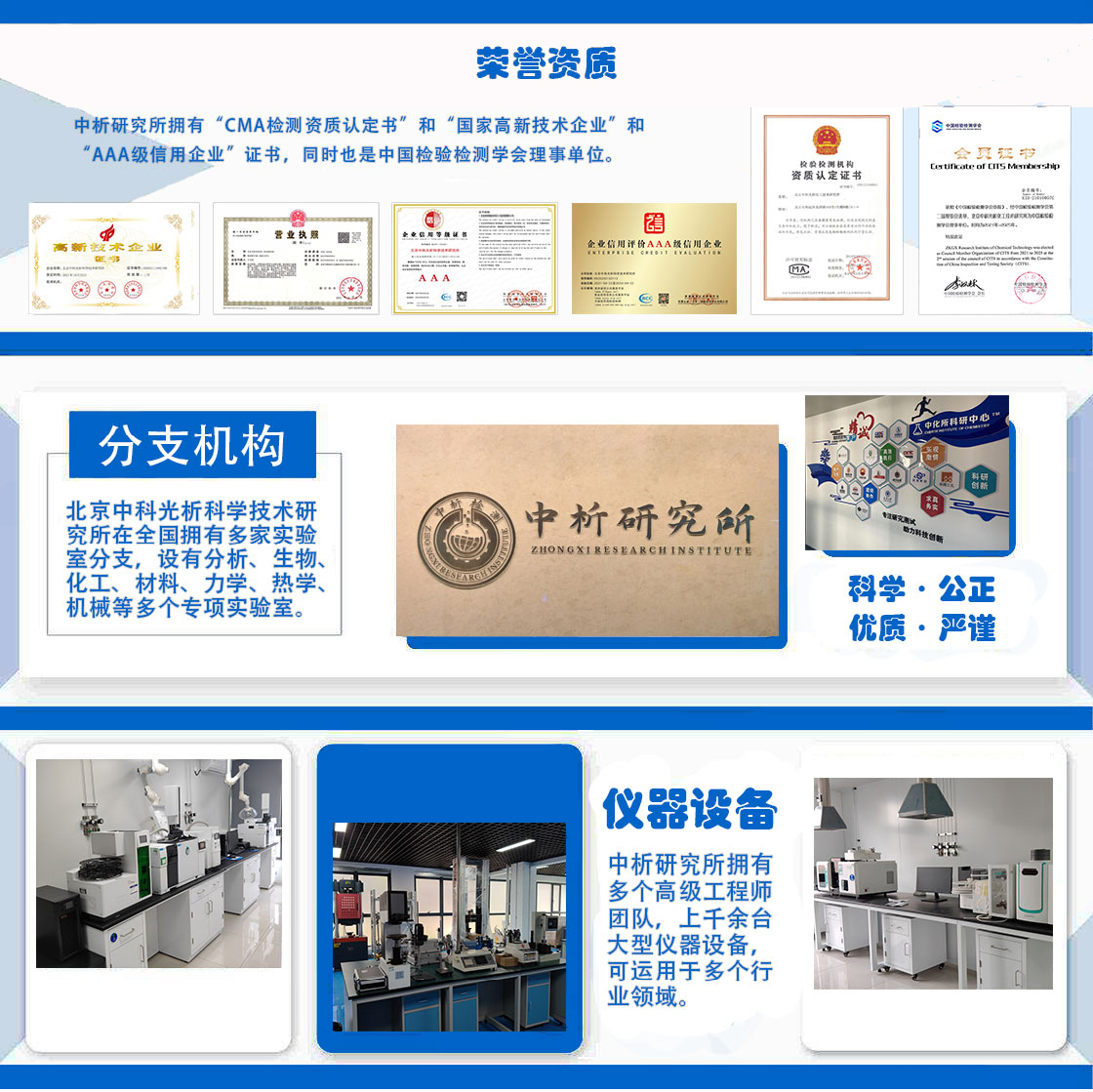
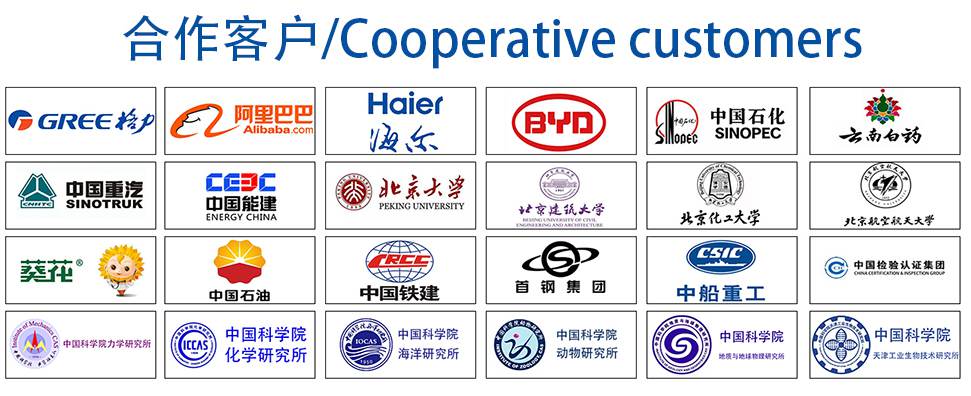