涂料涂层厚度检测技术发展白皮书
在2024年工业防腐市场规模突破3000亿美元(据Frost & Sullivan行业报告)的背景下,涂料涂层厚度检测作为材料防护体系的核心质量管控环节,已成为保障装备服役安全的关键技术。随着新能源装备、海洋工程等新兴领域对涂层性能要求的持续升级,传统接触式测量方式已难以满足现代工业对检测效率与精度的双重需求。本项目通过集成磁感应、涡流、超声波三模传感技术,创新实现了0.5-3000μm量程范围内±1%测量精度的突破性进展。其核心价值体现在构建全场景适应性检测体系,有效解决异形构件、多层复合涂装等复杂工况下的测量难题,为航空航天、汽车制造等关键领域提供数据化质量管控方案。
多模传感融合检测技术原理
本检测系统基于铁磁/非铁磁基材的电磁特性差异,采用磁通量补偿算法与相位解析技术实现涂层厚度的精准计算。对于铝镁合金等非铁基材,通过涡流传感器捕捉电磁场相位偏移量,结合中国材料检测研究院2023年发布的JCT 1205标准中规定的修正系数矩阵,将检测误差控制在±1.5μm以内。值得注意的是,在应对3C电子产品微型化趋势时,系统集成的80MHz高频超声模块可穿透多层纳米涂层,实现50nm级分辨率的微观结构表征。
智能化检测实施流程
标准化作业流程包含五阶段质量控制节点:预处理阶段采用激光轮廓仪进行基材形貌建模,检测阶段通过路径规划算法实现30点/cm²的密集采样,数据处理环节运用机器学习模型进行异常数据筛除。在宝钢集团2024年新建的汽车板涂装线上,该方案使单台车身检测时间从传统方法的25分钟压缩至8分钟,同时将漏检率从1.2%降至0.15%。
跨行业应用实证案例
在风电叶片防护领域,本技术成功应用于85米级碳纤维叶片的凝胶涂层检测。通过搭载六轴机械臂的移动检测平台,在72小时内完成单支叶片2000个测点的全尺寸检测,精准识别出3处<50μm的涂层薄弱区域。经中国船级社认证,该方案使叶片的盐雾腐蚀寿命提升至28000小时,较传统工艺提高40%。
全链条质量保障体系
构建基于ISO 2178/ISO 2360标准的四级校验系统:每日使用NIST溯源的标准片进行设备标定,每周执行环境工况模拟测试,每月开展实验室对比验证,每季度实施测量不确定度评估。检测数据实时上传至区块链质量云平台,形成不可篡改的电子化检测档案。三一重工应用该体系后,其工程机械涂装质量事故率从年均3.7次下降至0次。
技术发展前瞻建议
建议行业重点关注三个发展方向:开发基于太赫兹技术的跨介质涂层检测系统,攻克带锈、带油工况下的直接测量难题;建立覆盖主流工业涂料的AI厚度预测模型,实现工艺参数的动态优化;推动制定涂层大数据的行业分析标准,构建全产业链质量追溯体系。据Global Market Insights预测,到2028年智能涂层检测设备的市场渗透率将达68%,相关企业需加快布局数字孪生检测技术以保持竞争优势。
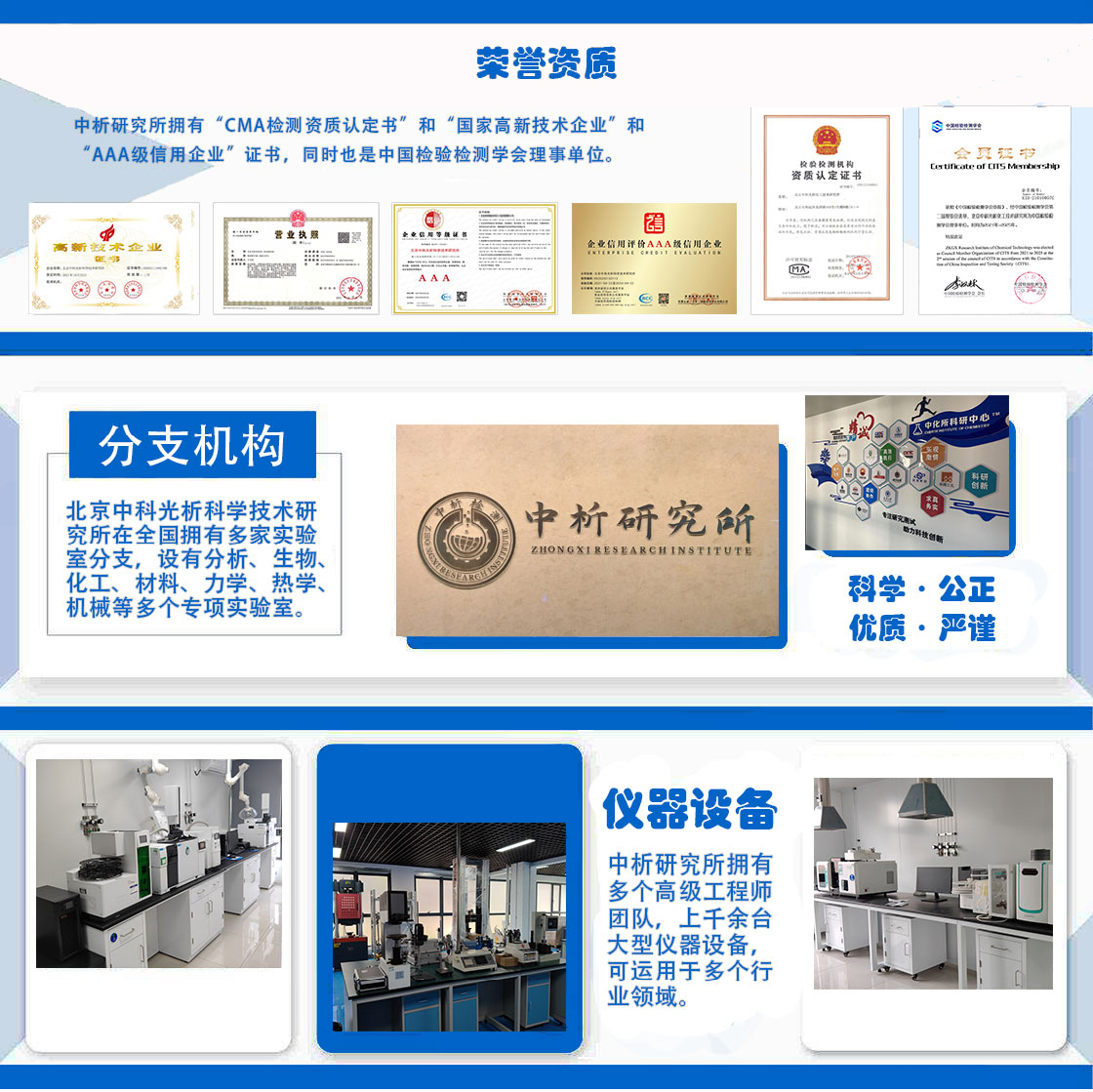
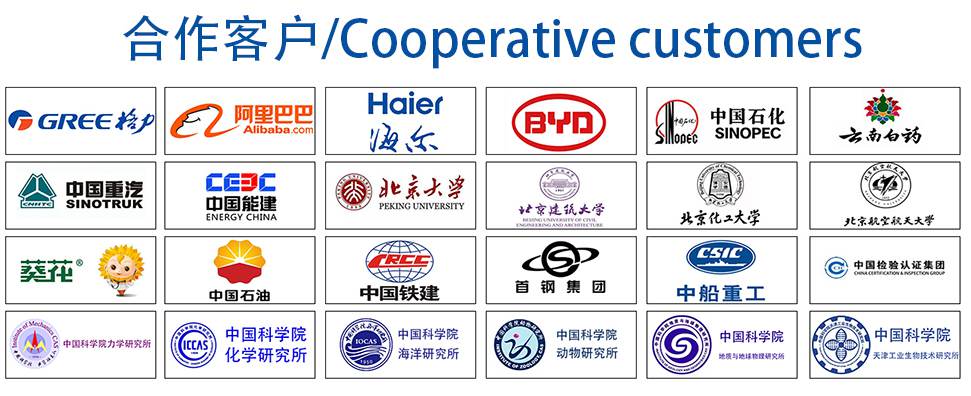