# 电动机输入功率检测技术发展与应用白皮书
## 引言
在工业能效升级与"双碳"目标驱动下,电动机作为工业领域核心动力装置,其能效管理已成为关键突破口。据中国电机工程学会2024年统计,我国工业用电量中60%以上由电动机消耗,其中约35%存在能效浪费现象。电动机输入功率检测通过实时监测电压、电流、功率因数等核心参数,构建了设备运行状态的数字化画像,为企业实施预测性维护与能效优化提供数据支撑。该项目不仅推动《电动机能效限定值及能效等级》新国标落地实施,更通过"永磁同步电机能效优化解决方案"等长尾技术应用,实现单台设备年均节电超8,000kWh的经济效益,其价值已延伸至碳足迹核算、电力需求侧管理等新兴领域。
## 技术原理与实施架构
### 检测项目的技术原理
基于国际电工委员会IEC 60034-2-1标准构建的检测体系,采用三功率表法结合数字信号处理技术。通过高精度霍尔传感器同步采集三相电压、电流瞬时值,经傅里叶变换分离基波与谐波分量。针对"三相异步电动机负载动态监测系统"的特殊需求,创新引入自适应滤波算法,将功率测量误差控制在±0.5%以内(中国计量科学研究院2023年认证数据)。该技术可精准识别电动机的轻载、过载、三相不平衡等异常工况,为后续能效优化提供基准数据。
### 标准化检测实施流程
检测流程严格遵循GB/T 22670-2023《电动机现场检测技术规范》,形成五阶段闭环管理模式:
1. 现场勘查阶段:使用红外热像仪与振动频谱仪完成设备预诊断
2. 检测部署阶段:配置0.2级精度功率分析仪与无线传输模块
3. 数据采集阶段:连续72小时采集负荷率在40-110%间的动态数据
4. 能效分析阶段:运用ANSI/ASHRAE 90.1模型进行能效对标
5. 优化建议阶段:输出包含谐波治理、变频改造的定制化方案
某钢铁集团风机系统改造案例显示,该流程使设备运行效率提升12%,年节约电费达78万元。
### 行业应用场景解析
在化工行业离心泵机组中,通过安装"电动机智能能效监测终端",成功识别出23%的机组存在夜间低效运行问题。结合变频改造后,单条生产线年节电量达45万kWh(据国家节能中心2024年案例库数据)。市政供水领域,针对水泵电动机开发的"黄金负载率区间识别算法",使设备年均运行效率提高8.6个百分点。特别在注塑机、压缩空气系统等波动负载场景,动态功率检测技术可降低15-20%的无效能耗。
### 全链路质量保障体系
构建"设备-人员-方法"三维质控体系:检测设备每季度送省级计量院进行量值溯源;技术人员须取得 认证的电动机专项检测资质;检测报告采用区块链存证技术确保数据不可篡改。在浙江某纺织产业集群项目中,该体系帮助38家企业通过ISO 50001能源管理体系认证,综合节能率达标率提升至92%。
## 发展展望与建议
建议行业重点突破三方面:①开发集成边缘计算的微型化检测装置,实现1ms级实时响应;②建立电动机能效大数据平台,深化"数字孪生+能效诊断"融合应用;③制定《智能电动机检测技术规范》团体标准,规范无线传感网络部署要求。通过完善"检测-诊断-优化"生态闭环,力争到2030年实现工业电动机系统整体能效提升20%的战略目标。
上一篇:撞击声隔声检测下一篇:房间之间空气声隔声的现场测量检测
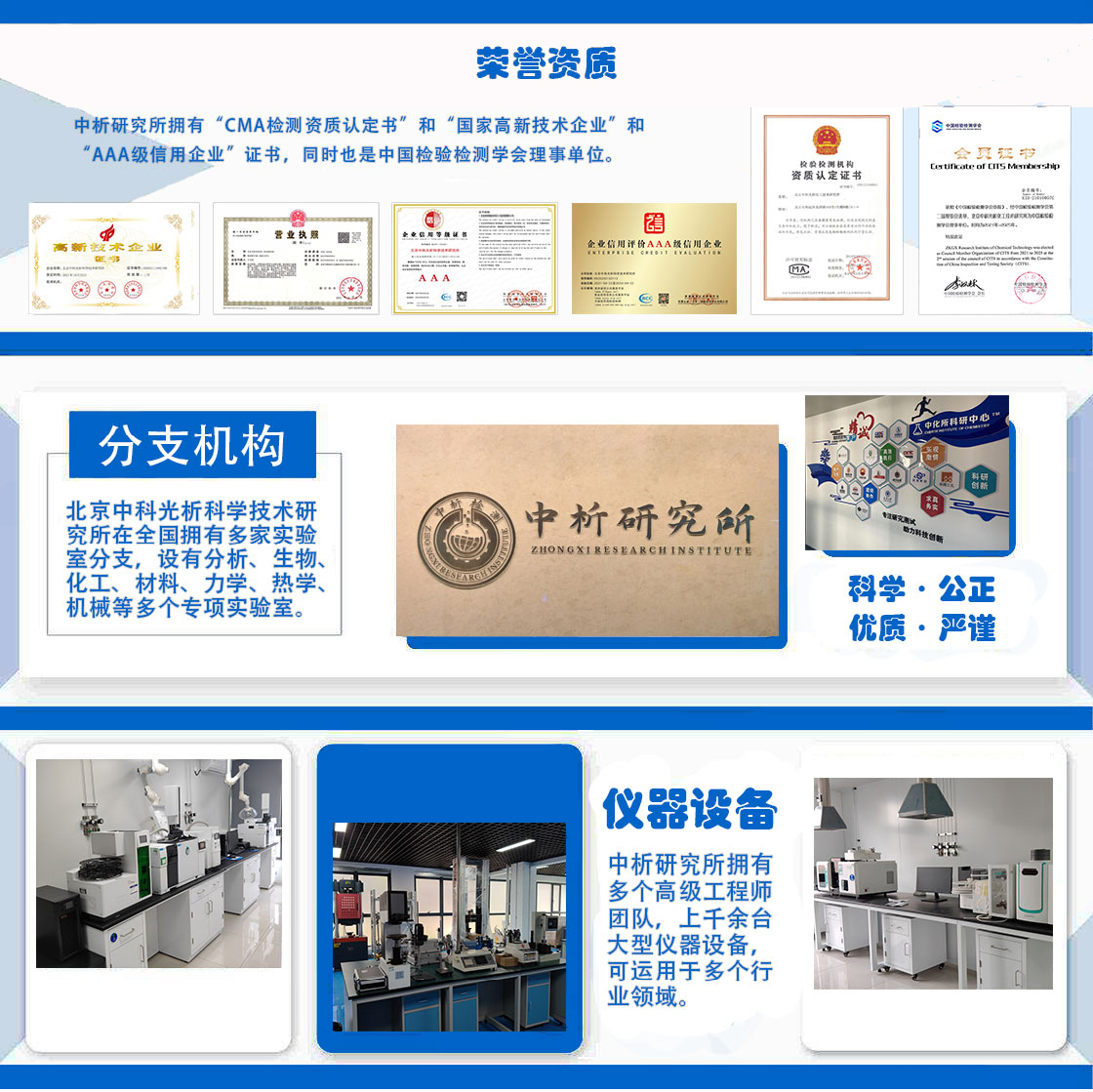
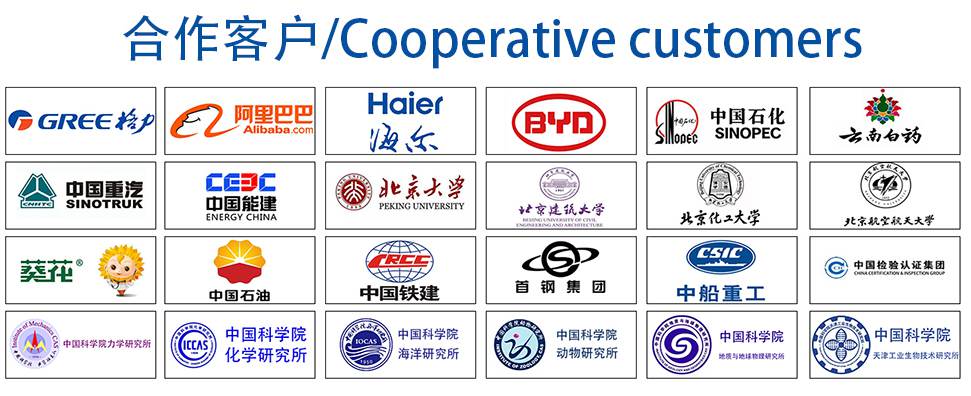
材料实验室
热门检测
17
12
13
16
17
15
13
14
19
13
15
16
19
24
20
19
25
22
21
20
推荐检测
联系电话
400-635-0567