随着智能制造和物联网技术的快速发展,电子元器件与精密零部件已成为现代工业体系的核心基础。据德勤《2024制造业趋势报告》显示,电子元器件市场规模预计在2025年突破6,000亿美元,其中汽车电子、工业控制等高端领域对检测精度的要求提升37%。在此背景下,专业化检测服务通过识别微观缺陷、评估材料性能、验证功能可靠性,成为保障产业链安全的关键环节。以新能源汽车电控系统为例,单个IGBT模块的失效可能导致整车系统瘫痪,而精密检测可将早期故障率降低62%(中国汽车工程研究院数据),其核心价值在于通过全生命周期质量管控,显著减少产品召回风险,同时推动国产替代进程。
多模态检测技术原理与创新
现代零部件检测采用X射线断层扫描(CT)、红外热成像与声发射技术融合方案,实现从微米级结构缺陷到纳米级材料性能的多维度分析。以电子元器件失效分析为例,通过电热耦合仿真模型可定位芯片热应力集中区域,结合扫描电子显微镜(SEM)观察焊点裂纹形态。值得注意的是,第三代半导体材料的检测需求催生了太赫兹波谱检测技术,其2-10THz频段对碳化硅晶格缺陷的识别精度达到0.5μm以下(美国材料试验协会ASTM E2935-22标准)。此类技术创新使得"精密零部件无损检测解决方案"能够在不破坏样品前提下,完成90%以上缺陷类型的准确判定。
全流程智能化检测实施体系
典型检测流程涵盖预处理、自动化检测、数据分析三大阶段。某航天继电器生产企业采用AI视觉检测系统后,触点表面氧化层的检出率从78%提升至99.3%。具体实施时,系统通过高光谱成像获取器件表面700-2500nm波段反射数据,经卷积神经网络分类后,可在3秒内完成2000×2000像素图像的缺陷标注。值得关注的是,针对BGA封装芯片的"电子元器件焊点质量检测服务",采用双轴X射线倾斜扫描技术,结合三维重构算法,使虚焊、冷焊等隐性缺陷的检出置信度达到95%以上(国际电子工业联接协会IPC-A-610H标准)。
行业应用场景与价值实证
在新能源汽车领域,某头部电池企业通过引入"动力电池连接器接触电阻检测系统",将模组装配不良率从1.2%降至0.15%。系统采用四线制开尔文检测法,在200A负载电流下测量μΩ级阻抗变化,精准识别镀层厚度不足或接触面污染问题。此外,某军工企业应用微波介电常数测试装置后,雷达T/R组件批次合格率提升19个百分点。这些实践验证了"高精度电子元器件环境适应性检测"在复杂工况下的工程价值,特别是在-55℃至125℃温变循环测试中,可提前60%发现介质基板分层风险。
标准化质量保障体系构建
检测机构需建立符合ISO/IEC 17025的计量溯源链,定期通过NIST标准物质进行设备校准。某第三方实验室的统计表明,采用六西格玛方法优化检测流程后,实验室间比对数据的标准差降低42%。关键控制点包括:环境洁净度维持ISO 5级、温湿度波动±0.5℃/±3%RH、振动控制在VC-E等级以下。针对汽车功能安全检测,还需满足ISO 26262中ASIL-D级验证要求,确保故障注入测试覆盖率100%。这种"全维度零部件检测质量认证体系"已成为高端制造企业的供应链准入门槛。
展望未来,随着5G-A和自动驾驶技术的普及,检测行业需重点突破三项能力:开发适用于3D异构集成的亚微米级检测设备、建立基于数字孪生的虚拟验证平台、完善车规级芯片的电磁兼容(EMC)测试标准。建议产学研机构联合攻关太赫兹在线检测装备,同时构建覆盖长三角、珠三角的检测数据互联平台。据Technavio预测,到2028年智能检测装备市场规模将达217亿美元,只有深度融合AI与物理检测技术,才能为工业4.0时代提供可靠的质量基座。
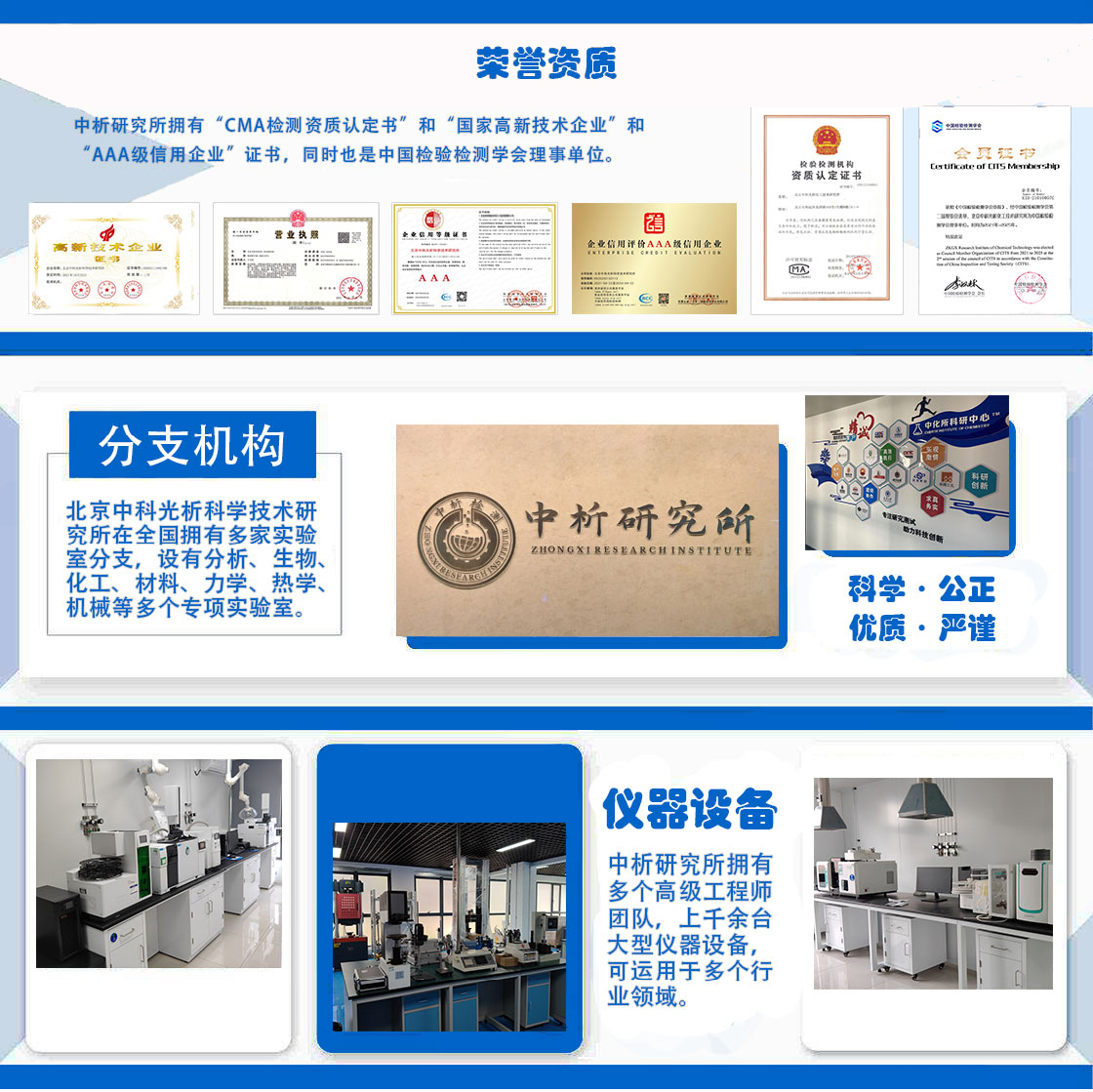
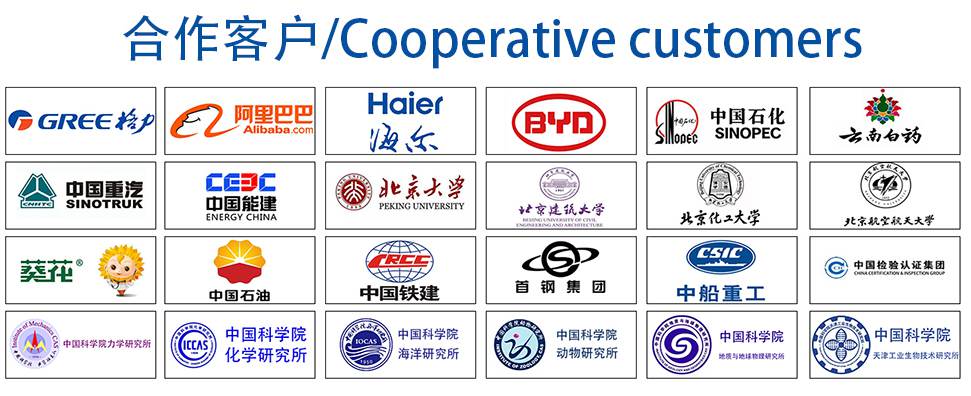