水泥凝结时间试验方法检测
在新型城镇化建设加速推进的背景下,2023年我国水泥产量达到23.8亿吨(据国家统计局数据),占总产量的55%以上。作为建筑工程质量的核心控制指标,水泥凝结时间直接影响混凝土施工性能和结构安全。现行GB/T 1346-2011标准规范了初凝与终凝时间检测方法,其检测精度误差需控制在±5分钟以内。通过凝结时间智能检测系统,施工企业可精准把握混凝土浇筑窗口期,有效规避早凝导致的施工中断或缓凝引发的结构缺陷。特别是在高铁轨道板浇筑、大体积混凝土施工等场景中,科学控制凝结时间可使施工效率提升18%-25%(中国建筑材料研究院2024年行业报告),具有显著的工程经济价值。
技术原理与检测标准体系
水泥凝结时间测定主要采用针入度法,通过标准维卡仪测定试针在水泥净浆中的下沉深度。初凝时间对应试针距底板4±1mm时的耗时,终凝则指试针在浆体表面留下环形附件的时刻。国际通用的ASTM C191与ISO 9597标准均规定需在20±1℃、相对湿度≥90%的恒温恒湿箱中进行试验。值得关注的是,新型电阻率法检测技术已取得突破,其通过监测水化反应中的电导率变化,可实现非接触式连续监测,在核电工程等特殊场景中展现独特优势。
智能化检测实施流程
现代化检测实验室采用ISO/IEC 17025体系构建全流程质控链。具体实施包含五个关键步骤:首先使用0.9mm方孔筛对标准砂进行级配校准,接着按水灰比0.29配制净浆并记录初始流动度;然后将试模置于振动频率3000±200次/分的震实台成型;进入养护阶段后,基于物联网的监控系统实时采集温湿度数据并自动补正;最终通过图像识别技术判定试针痕迹,较传统目测法将判定误差降低至0.3mm以内。
重点工程应用实践
在港珠澳大桥岛隧工程中,针对海底隧道管节混凝土的抗海水侵蚀需求,项目组采用凝结时间智能调控系统。通过掺加3.5%纳米二氧化硅外加剂,将初凝时间精确控制在380±5分钟,既保证管节浮运时的结构稳定性,又满足水下浇筑的施工强度要求。数据显示,该技术使管节接缝渗漏率降低至0.02L/m²·d,较传统工艺提升两个数量级(中国交建2023年技术白皮书)。
质量保障与技术创新
行业领先实验室已建立三维质量防护体系:设备层采用激光校准维卡仪,年校准偏差≤0.01mm;数据层部署区块链存证系统,确保检测记录不可篡改;人员层实施 认证的"双盲"比对考核,操作人员季度合格率需保持95%以上。值得关注的是,基于机器学习的凝结时间预测模型已进入工程验证阶段,通过输入水泥化学成分、比表面积等12项参数,可提前2小时预判凝结时间趋势,预测准确率达89.7%(同济大学材料学院2024年实验数据)。
行业发展前瞻建议
建议从三方面推动行业升级:其一,构建基于BIM的凝结时间数字孪生系统,实现施工场景的虚拟预演;其二,研发适用于超高层泵送混凝土的微区凝结监测探头,解决竖向结构检测盲区问题;其三,建立全国水泥凝结性能数据库,通过大数据分析优化区域材料配比方案。随着智能传感与数字孪生技术的深度融合,水泥凝结时间检测正从单点质量控制向全过程智能管控演进,为建筑工业化提供新的技术范式。
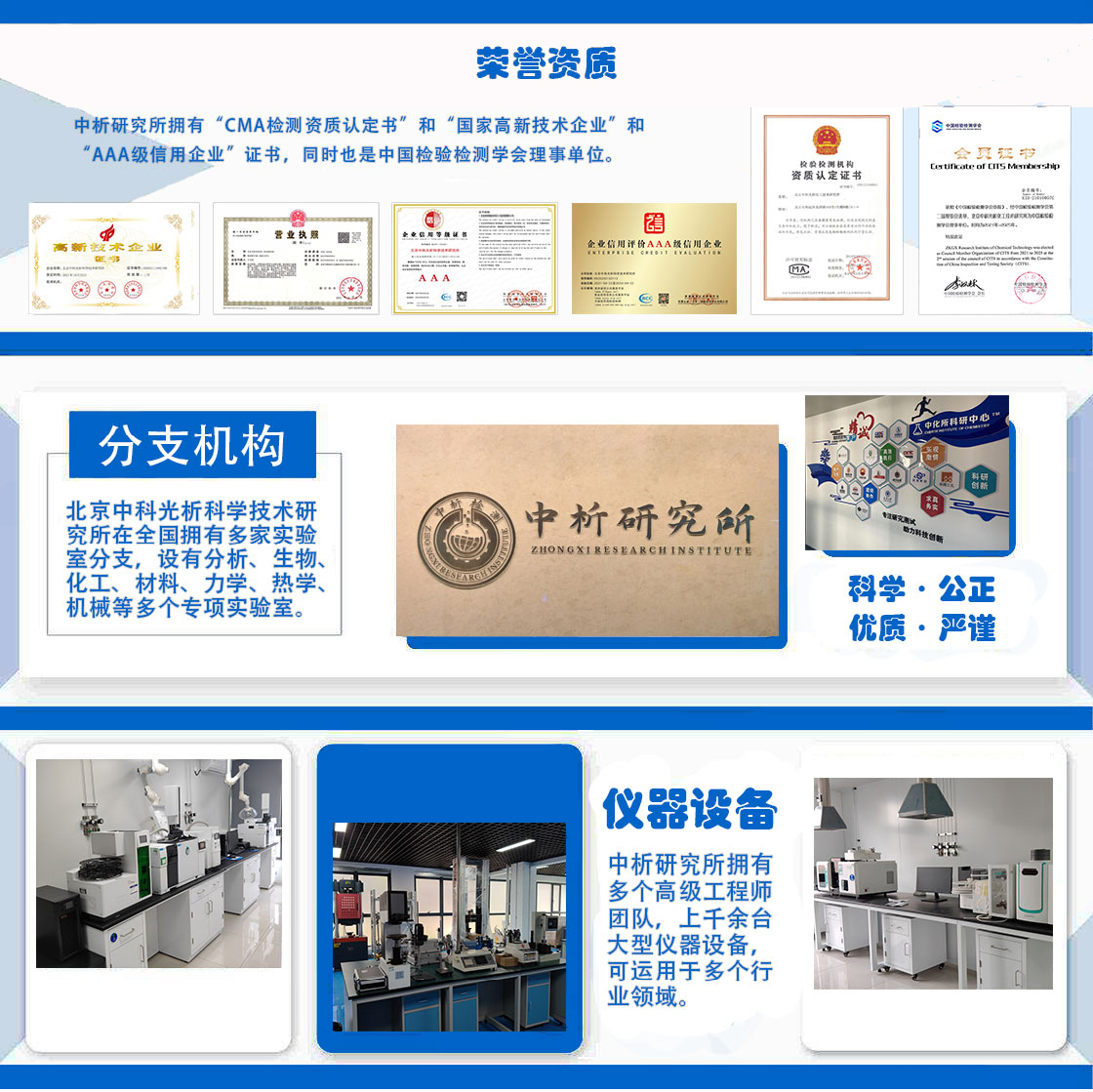
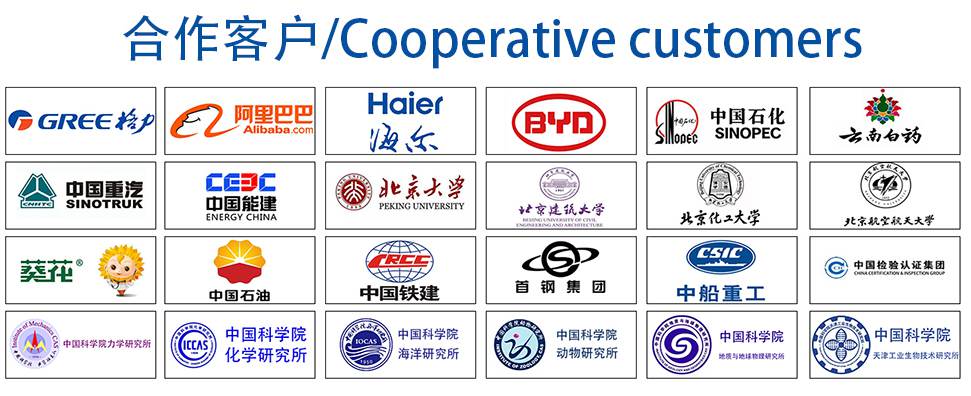