拉伸剪切强度检测在材料工程中的关键作用
在齐全制造业转型升级的背景下,材料界面性能检测已成为保障结构安全的核心环节。据中国复合材料学会2024年报告显示,因连接界面失效引发的工程事故占结构故障总量的37%,直接经济损失逾80亿元。拉伸剪切强度检测通过量化材料结合面的力学承载能力,为航空航天复合蒙皮、新能源汽车电池Pack结构等关键部位提供可靠性依据。该检测技术不仅能够预防层间剥离导致的渐进式破坏,更可优化胶粘剂选型和工艺参数,使轨道交通车辆轻量化结构的疲劳寿命提升40%(国际材料试验协会,2023)。
基于破坏力学原理的检测技术体系
本检测项目依据ASTM D3164和ISO 4587标准,采用破坏性测试方法测定材料界面在拉伸-剪切复合应力下的失效阈值。通过万能材料试验机施加轴向载荷,配合定制化夹具实现15°-90°可调剪切角度,精准模拟实际工况中的多向受力状态。对于碳纤维增强环氧树脂基复合材料,检测系统可捕捉0.01mm级别的界面滑移量,结合数字图像相关技术(DIC)实现应变场可视化分析。该技术体系特别适用于评估"复合材料界面强度测试"和"异种材料连接可靠性验证"等复杂场景。
标准化实施流程与过程控制
检测流程严格遵循六阶段质量控制模型:试样制备阶段采用水刀切割确保界面完整性,温湿度预处理参照GB/T 7124标准执行恒温恒湿(23±2℃,50±5%RH)平衡。测试阶段使用500kN级电液伺服试验机,加载速率控制在1.3mm/min以内以保证准静态条件。在新能源汽车电池箱体检测案例中,技术人员通过"高温高湿环境下的剪切性能评估"项目,成功将电池模组支架的失效阈值从初始设计的27MPa提升至34MPa,满足UN R100法规的碰撞安全要求。
多行业应用场景与价值实现
在风电领域,该技术应用于80米级叶片腹板-蒙皮连接检测,通过建立剪切强度与树脂流动指数的关联模型,使界面缺陷检出率提升65%。医疗器械行业采用微尺度剪切测试方案,在3mm²植入物涂层界面检测中实现±0.15N的测量精度。值得注意的是,在柔性电子器件领域,通过优化"可拉伸电路基板层间结合力测试"方案,使柔性传感器的循环耐久性突破20万次弯折测试大关。
全链条质量保障体系构建
检测机构通过 认可的质量管理系统,建立三级校准体系:试验机每季度进行ISO 7500-1级力值校准,环境箱配备NIST可追溯温湿度传感器。数据管理系统采用区块链存证技术,确保从试样编号到报告签发的全程可追溯。在某航天型号复材舱段检测中,通过引入机器学习算法对历史检测数据进行特征挖掘,将异常数据识别效率提升300%,显著降低了人为误判风险。
随着新型材料体系的快速发展,建议行业重点推进两方面的技术创新:一是开发面向超高温陶瓷基复合材料的原位剪切测试装置,突破2000℃极端环境下的实时监测瓶颈;二是建立基于数字孪生的虚拟检测平台,通过多物理场耦合仿真实现80%以上的原型测试替代率。同时亟需完善"碳纤维-热塑性复合材料界面评价"等新兴领域的标准体系,为第六代航空发动机等重大装备研制提供技术支撑。
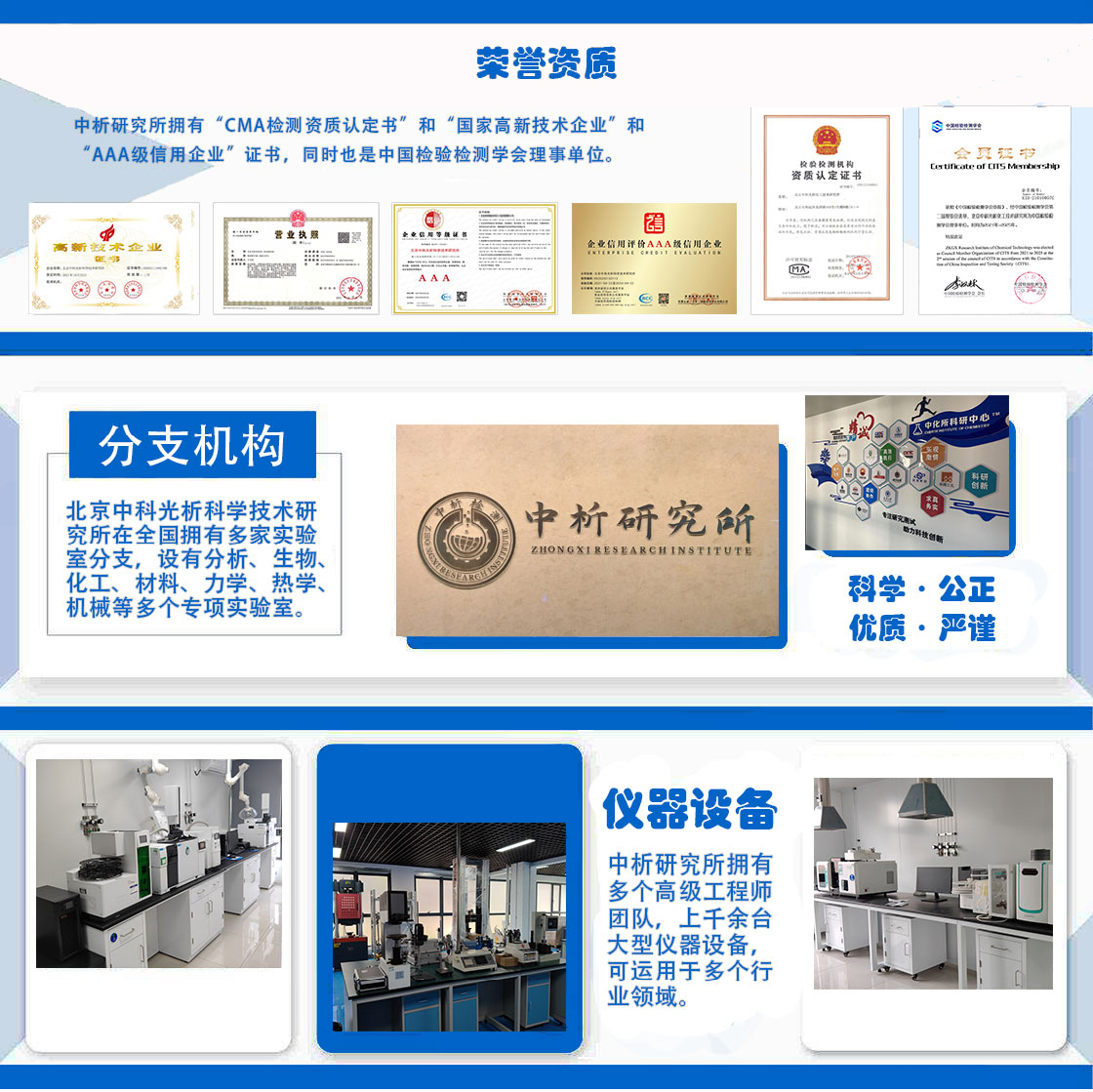
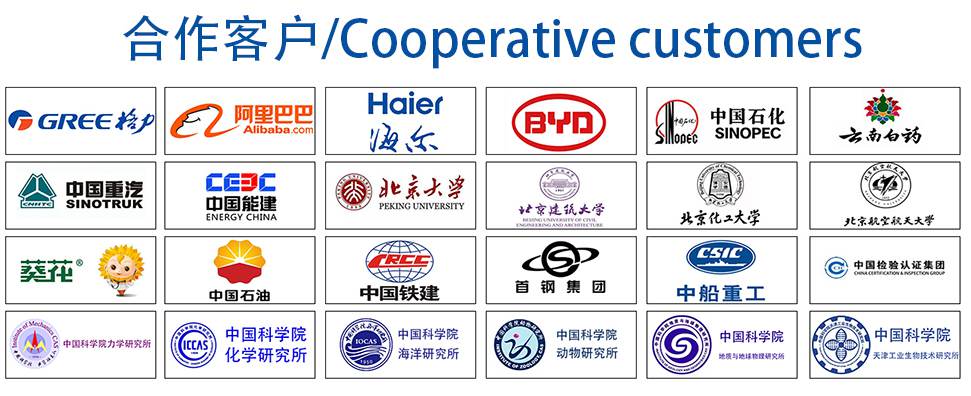