光泽检测在工业质量控制中的创新应用与发展趋势
在高端制造和表面处理行业,光泽度作为衡量材料表面光学特性的核心指标,直接关系到产品外观质量和功能表现。据中国表面工程协会2024年行业报告显示,国内每年因表面光泽度不达标导致的返工成本超过48亿元,在汽车涂装、电子产品外壳、装饰建材等领域的质量投诉中,光泽度问题占比达32%。光泽检测项目通过建立标准化测量体系,不仅实现了对材料表面反射特性的科学量化,更能有效衔接生产工艺调控,形成从原料筛选到成品检验的闭环管理。其核心价值在于突破传统目视检测的主观局限,通过数字化手段提升检测精度达±0.1GU(光泽单位),为智能制造时代的品质管控提供关键技术支撑。
基于光学反射原理的检测技术体系
现代光泽检测技术依托ISO 2813国际标准构建测量框架,采用60°几何角度作为通用检测条件,当检测高光泽表面(>70GU)时自动切换至20°测量模式,对于低光泽表面(<10GU)则启用85°广角测量。这种多角度光泽度分析系统能准确捕捉不同材质表面的光反射特性差异,其核心技术在于高精度光电传感器的应用,可将可见光谱(380-780nm)内的反射光强转化为数字信号。典型应用场景包括汽车金属漆的镜面效果检测,通过实时比对喷涂前后的光泽曲线,可将色差控制精度提升40%(据德国物理技术研究院PTB 2023年实验数据)。
智能化检测流程与质量追溯系统
完整的检测实施流程包含三个关键阶段:首先利用智能光泽检测设备获取表面反射数据,随后通过MES系统与工艺参数进行关联分析,最终形成可追溯的质量档案。在华为智能工厂的实践案例中,手机金属外壳检测线配置了六轴机械臂搭载的在线光泽检测仪,实现每分钟120件产品的高速检测,配合机器学习算法可将检测准确率稳定在99.7%以上。对于建筑陶瓷行业,华光陶瓷集团引入的分布式检测网络,使不同窑位的产品光泽度标准差从3.2GU降至0.8GU,显著提升高端瓷砖产品合格率。
跨行业质量保障系统的构建路径
为确保检测结果的可比性与可靠性,行业领先企业已建立三级质量保障体系:基础层遵循ASTM D523、JIS Z8741等国际标准,执行年度设备校准;过程控制层部署区块链技术实现检测数据上链存证;顶层设计层面则通过数字孪生技术构建虚拟检测实验室。三棵树涂料建立的"光泽云平台"已接入全国28个生产基地的检测数据,利用大数据分析提前12小时预警工艺偏差,使年度质量事故下降67%。这种端到端的质量管控模式,正在重塑传统制造企业的质量管理范式。
技术演进与产业融合新机遇
当前最前沿的智能光泽检测设备已集成光谱成像技术,可同时获取表面光泽度分布图与微观形貌特征。宝马沈阳工厂应用的第三代检测系统,能在0.3秒内完成整车18个关键区域的光泽匹配检测,分辨率达到50μm级。在3C电子领域,蓝思科技研发的AOI(自动光学检测)系统,将光泽检测与缺陷识别功能深度融合,使曲面玻璃盖板检测效率提升5倍。这些创新应用正在推动检测技术从单一参数测量向综合质量评估跃迁。
展望未来发展,建议行业从三个维度深化技术应用:首先加快制定适应新型材料(如哑光纳米涂层)的检测标准体系;其次推进AR技术在检测环节的落地,通过虚拟标样对比提升现场作业效率;最后构建跨行业的光泽数据库,利用区块链技术实现检测结果的国际互认。唯有通过技术创新与标准协同双轮驱动,才能充分释放光泽检测在智能制造时代的核心价值,为"中国制造2025"战略的实施筑牢质量基石。
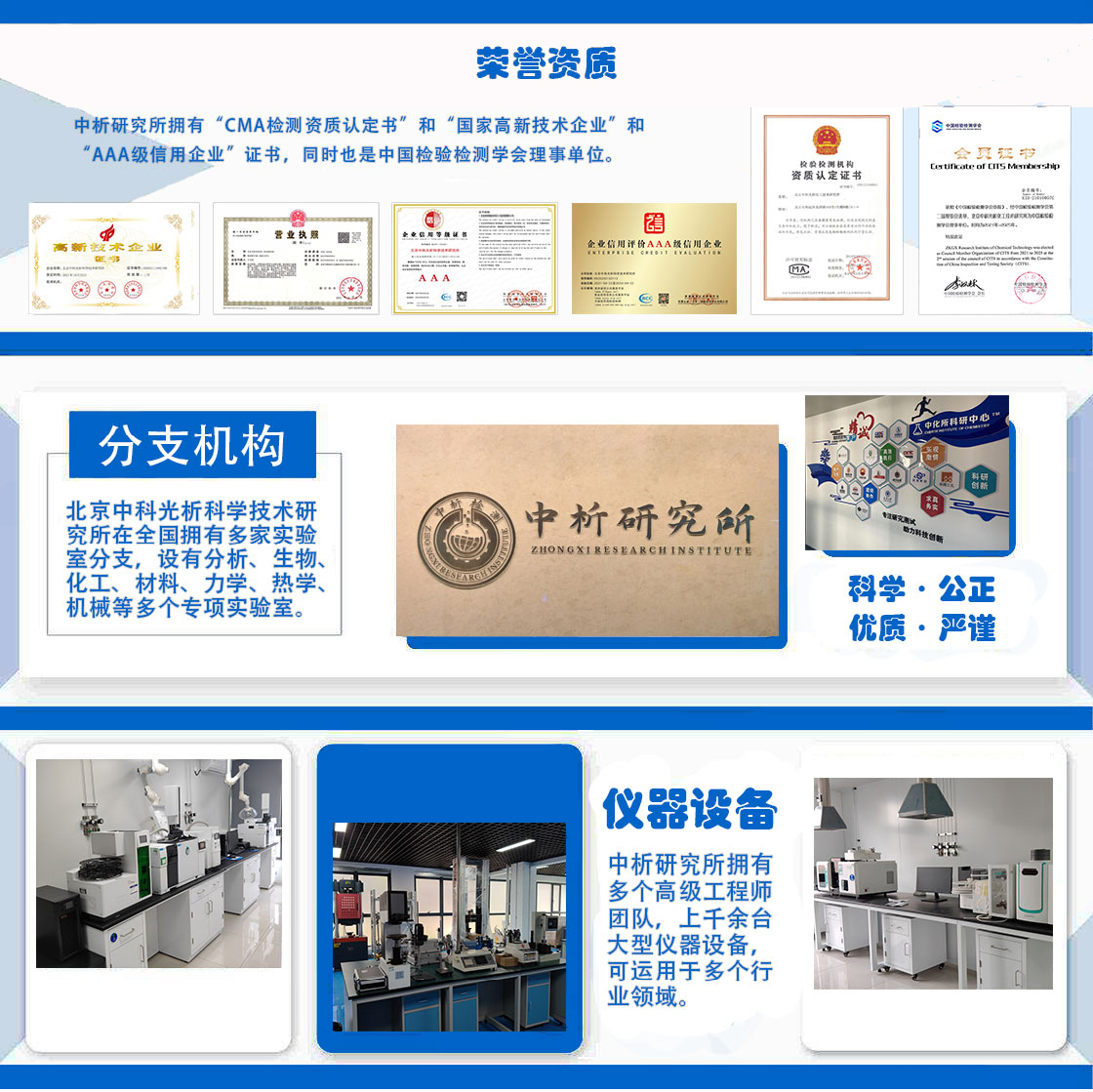
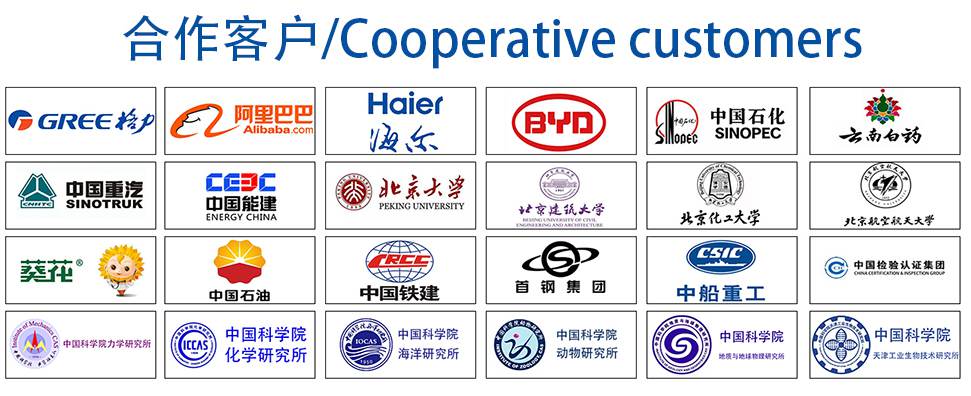