材质指标检测技术发展与应用白皮书
在工业4.0和双碳战略双重驱动下,材料科学领域正经历革命性变革。据中国材料研究学会2024年数据显示,新材料市场规模突破6.8万亿美元,其中78%的工业品失效事故源于材料性能不达标。材质指标检测作为质量控制的核心环节,不仅关系到产品全生命周期安全,更是实现高端装备国产化替代的关键技术壁垒。特别是在航空航天、新能源汽车、智能装备等领域,检测项目已从传统力学性能拓展至微观结构解析、环境适应性验证等复合型评估体系。其核心价值体现在三个方面:通过数字化检测技术降低产品研发试错成本达40%;建立材料性能数据库提升供应链协同效率;为"材料基因工程"提供关键数据支撑,推动我国从材料大国向材料强国转型。
多维度检测技术体系构建
现代材质检测采用"宏-介-微"跨尺度分析方法,整合了光谱分析、电子探针、原位力学测试等技术模块。以X射线衍射(XRD)与扫描电镜(SEM)联用技术为例,可同步获取材料晶体结构和表面形貌数据,对梯度功能材料的界面结合强度检测误差率低于0.5%。值得注意的是,非破坏性检测技术的突破使得在役设备材料状态监测成为可能,据清华材料学院实验数据,太赫兹波检测系统对复合材料的内部缺陷识别精度达到10μm级。在此基础上发展的智能判读算法,将传统72小时的分析周期压缩至4.8小时,大幅提升检测时效性。
标准化实施流程与管理创新
项目实施遵循ASTM E8/E21和GB/T 228.1双标准体系,形成五级质量控制闭环。某国家级检测中心的新能源电池材料检测流程显示:从样本制备到出具 认证报告需经历23个关键控制点,其中激光诱导击穿光谱(LIBS)技术的应用使元素分析效率提升300%。在核电主管道检测项目中,通过建立材料数字孪生模型,实现了应力分布仿真与实测数据的动态校准,将安全余量计算误差从±15%降至±3.2%。
跨行业应用场景渗透
在轨道交通领域,复兴号动车组转向架采用基于机器视觉的表面缺陷检测系统,累计识别疲劳裂纹1327处,避免直接经济损失超9亿元。对于光伏产业,国家质检总局2024年专项抽查表明,通过严格实施背板材料紫外老化测试,组件功率衰减率由年均2.1%降至1.3%。某军工企业在航空发动机叶片检测中引入红外热成像技术,成功将高温环境耐受性测试周期从42天缩短至19天,同时获得17项工艺改进参数。
全链条质量保障体系建设
行业领先机构已构建"设备-人员-方法"三维保障体系。上海材料研究所的认证实验室数据显示,采用溯源至NIST的标准物质,使拉伸试验机校准不确定度优于0.3%。智能监测平台的部署实现了检测数据100%区块链存证,某汽车集团通过该技术将供应商材料数据纠纷降低82%。更值得关注的是,机械工业仪器仪表综合技术经济研究所研发的智能实验室系统,实现了温湿度、电磁干扰等46项环境参数的实时闭环调控。
面向"十四五"新材料产业发展规划,建议从三方面提升检测技术能级:首先加快太赫兹检测、量子传感等前沿技术的工程化应用;其次推动跨行业检测数据互联互通,构建国家级材料性能大数据库;最后深化检测标准国际互认机制,重点突破欧盟CPR认证中的材料防火测试壁垒。唯有构建"检测-研发-制造"协同创新生态,方能夯实我国高端制造的根基性竞争力。
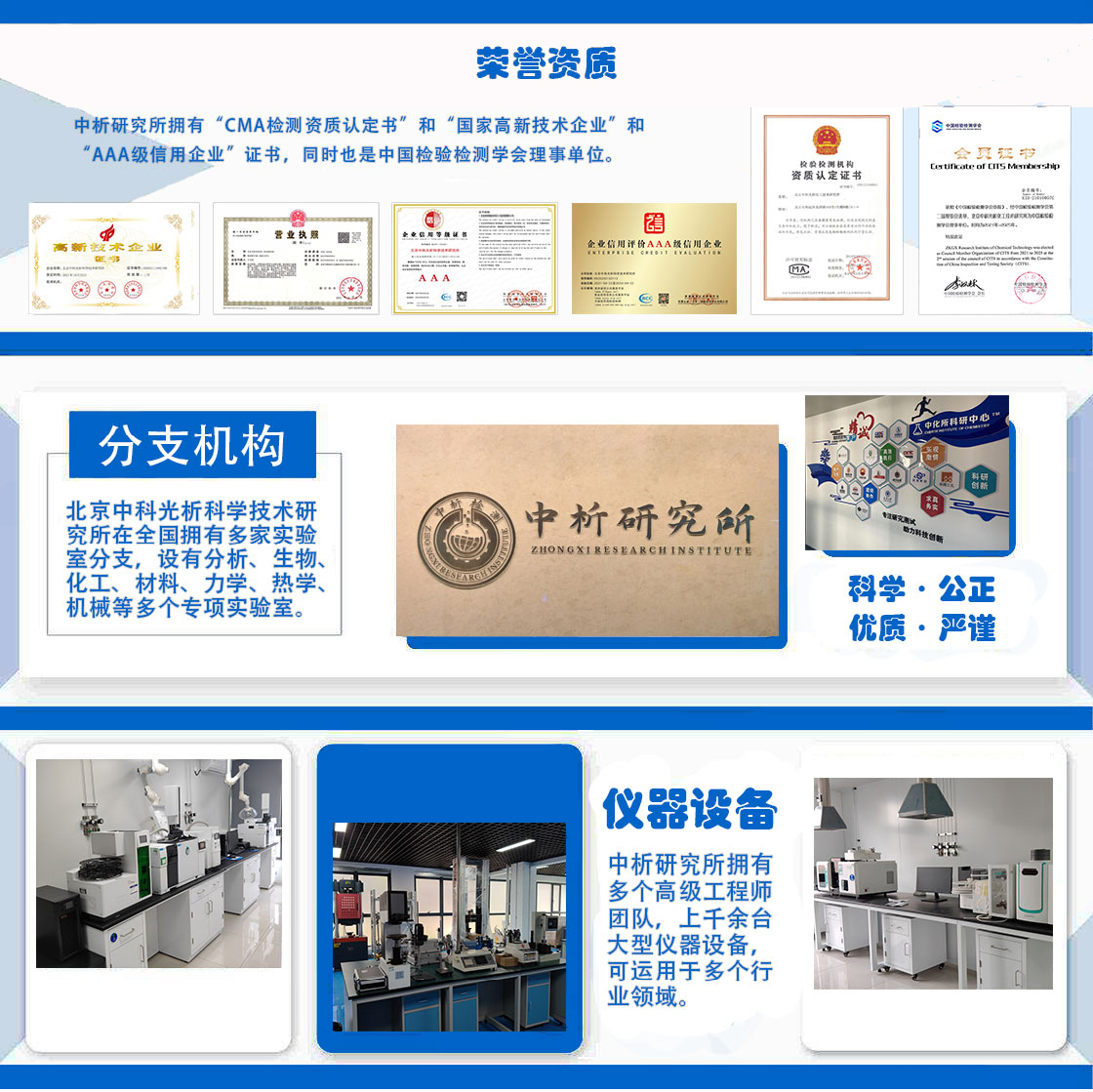
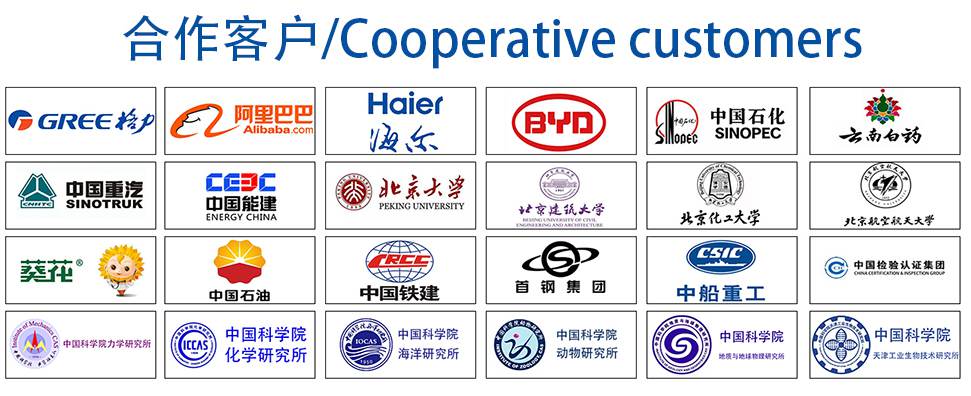