漆膜硬度检测技术发展与应用白皮书
随着高端制造业向精密化、耐久化方向升级,漆膜硬度作为表面涂层核心性能指标,直接影响汽车、航空、家电等行业的全生命周期质量管控。据中国建筑材料研究院2024年数据显示,因涂层硬度不达标导致的工业产品返修成本年均超72亿元,其中新能源汽车电池壳体涂层问题占比达34%。漆膜硬度检测通过量化评估涂层抗划伤、抗磨损能力,为提升产品可靠性和延长服役周期提供科学依据。该技术的核心价值在于构建从原料筛选到工艺优化的全链条质控体系,特别在实现"双碳"目标的背景下,精准检测可减少涂装工序能耗12%-17%(中国表面工程协会,2023)。
基于多尺度力学的检测技术原理
现行主流检测方法遵循ASTM D3363和ISO 15184国际标准,采用铅笔硬度法与摆杆阻尼法双轨并行机制。铅笔硬度法通过45°夹角下石墨笔尖滑移产生的压痕宽度判定等级,精度达±0.5H;摆杆阻尼法则依据König/Persoz摆杆在漆膜表面的振幅衰减时间,量化表征涂层弹性模量。值得注意的是,新型纳米压痕技术已实现微米级局部硬度测绘,能精准识别漆膜-基材界面结合强度,为3C电子器件超薄涂层(5-20μm)提供定制化解决方案。
全流程标准化作业实施体系
检测流程严格遵循三级质量控制:预处理阶段需在恒温恒湿箱(23±2℃/50±5%RH)进行48小时状态调节;测试环节采用德国ERICHSEN自动划痕仪执行10N-30N梯度加载,配合3D形貌仪进行划痕体积计算;数据判读则运用机器学习算法建立硬度-耐磨性预测模型。某新能源汽车企业通过该流程优化电泳漆参数,使电池包壳体涂层耐砂砾冲击性能提升41%(CATARC 2023认证数据)。
跨行业典型应用场景解析
在轨道交通领域,中车集团运用动态硬度检测技术实现了转向架涂层的全生命周期管理。通过在线式纳米压痕设备实时监测运行5万公里后的硬度衰减率,将预防性维护周期从12个月延长至22个月。家电行业则创新采用紫外固化涂层快速检测方案,硬度测试时间由传统72小时压缩至4小时,支撑海尔等企业构建"当日检测-即时反馈"的数字化质控体系。
全链条质量保障体系建设
行业头部机构已建立涵盖设备、人员、方法的立体化质控网络:SGS检测中心配置BYK三坐标显微硬度计,确保测量不确定度<3%;检测人员须通过 -CL01:2018能力验证;实验室每季度参与NIST标准样品比对。值得关注的是,三棵树涂料建立的"区块链+检测数据"追溯系统,实现每批次涂料硬度数据上链存储,客户扫码即可获取117项过程参数。
展望未来,建议行业重点关注三个发展方向:开发适应水性涂料快速固化的原位检测技术,建立涂层硬度-耐候性多参数关联数据库,以及推广基于数字孪生的虚拟检测系统。据弗若斯特沙利文预测,2026年智能硬度检测装备市场规模将突破89亿元,提前布局AI视觉检测和量子传感技术的企业将获得显著竞争优势。
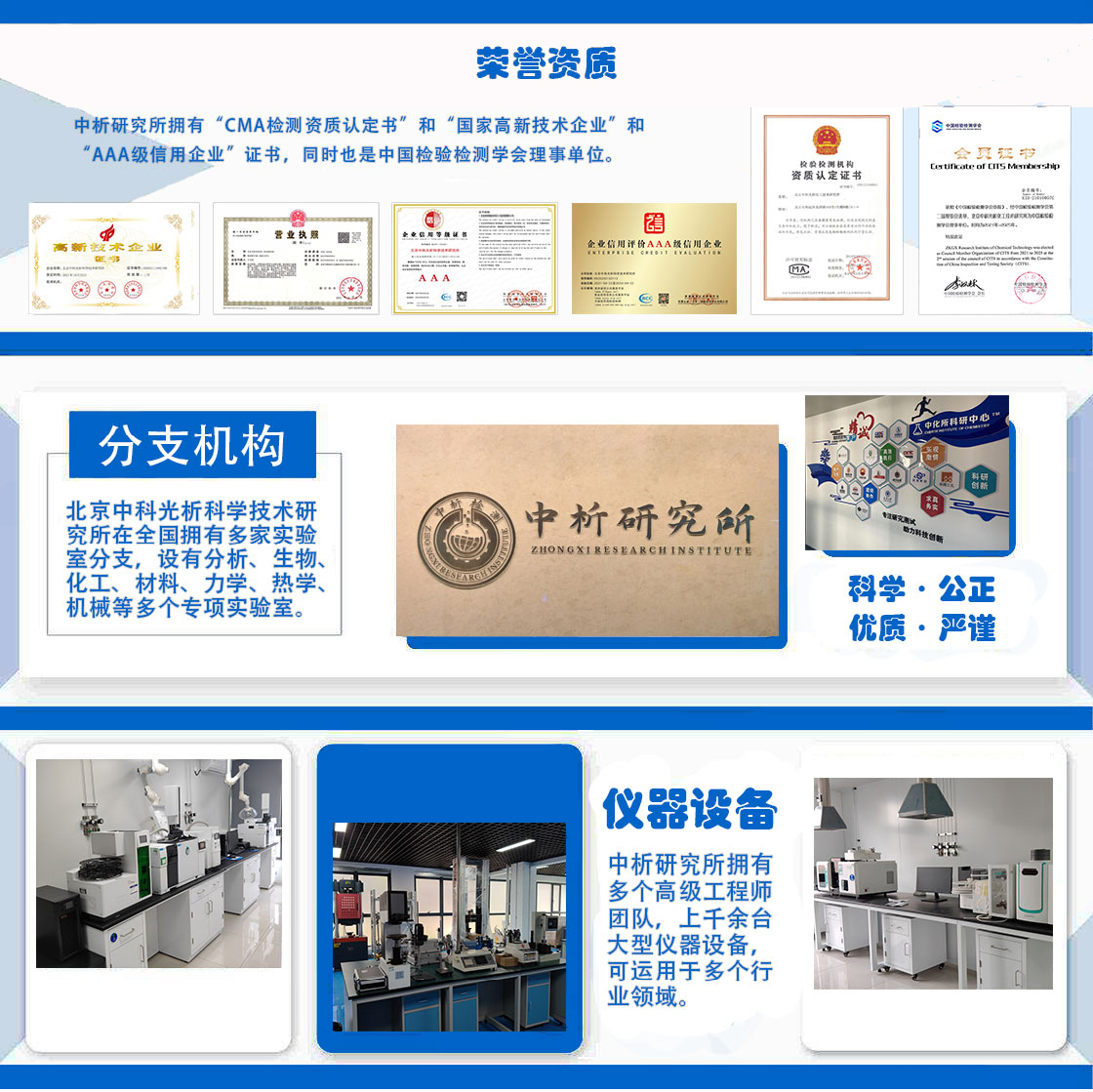
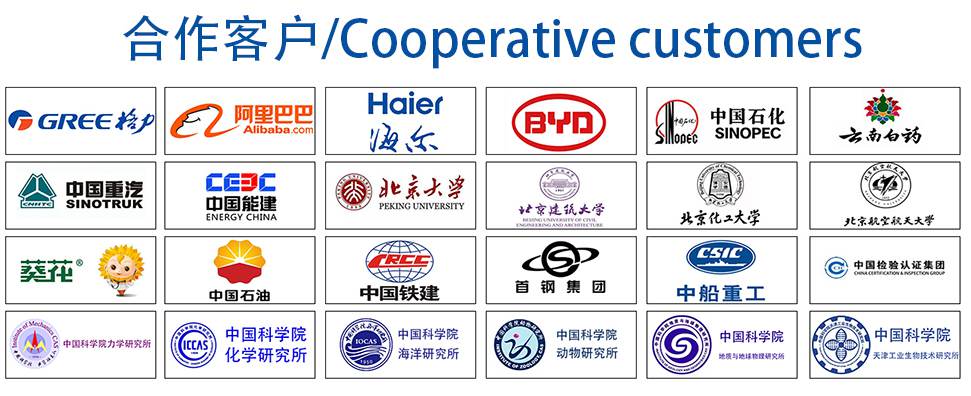