在制造业智能化转型背景下,单位有效宽度生产率检测已成为纺织、印刷、半导体等连续性生产行业的质量控制关键指标。据中国智能制造研究院2024年数据显示,我国宽幅材料加工行业年产值突破2.8万亿元,但设备有效利用率不足65%,因宽度偏差导致的废品损失高达行业总成本的12%。本项目通过建立精准的宽度效能评估体系,实现生产过程中有效作业宽度的实时监控与优化,其核心价值在于提升设备综合效率(OEE)3-5个百分点,同时降低单位能耗8%-15%。特别是在柔性显示面板制造领域,该技术可将基材利用率从78%提升至92%,显著增强企业在高端市场的竞争力。
## 技术原理与创新突破1. 多模态传感融合检测技术
本检测系统采用机器视觉与激光测距的协同工作机制,通过亚像素级图像处理算法实现0.01mm级宽度测量精度。针对高反光材料检测难题,创新性引入偏振光调制技术,使不锈钢箔材的检测误差从±0.5mm降至±0.08mm。结合国际标准化组织(ISO)的测量规范,系统内置17种行业专用检测模型,支持从3mm微型电子元件到5m宽幅复合材料的多尺度检测需求。
2. 智能化实施流程架构
实施流程遵循PDCA质量循环模型,具体分为四个阶段:首先通过分布式传感器网络采集产线实时数据,再运用数字孪生技术构建三维生产效能图谱,继而采用深度学习算法进行异常模式识别,最终形成动态工艺优化方案。在浙江某大型化纤企业的应用中,该流程使产线换型时间缩短40%,有效生产宽度波动幅度降低62%。
3. 行业应用场景解析
在锂电隔膜制造领域,系统成功解决了高速涂布机的边缘效应难题。通过实时跟踪1200mm幅宽生产线的有效工作区间,郑州某龙头企业将涂布均匀性标准差从3.2%降至1.7%,单线年节约原材料成本超800万元。值得关注的是,该系统在光伏玻璃深加工场景中,通过动态补偿热弯形变,使6mm超薄玻璃的成品率提升19个百分点。
4. 全生命周期质量保障
构建了涵盖ISO/IEC 17025标准的五级质量管控体系:从传感器年度计量溯源、算法模块的V模型验证,到产线级MTBF(平均无故障时间)超过10000小时的可靠性测试。在广东某PCB样板厂的实际运行中,系统连续18个月保持检测误报率<0.3‰,其双冗余架构设计更通过TÜV莱茵安全认证,满足工业4.0环境下的网络安全标准。
## 发展展望与战略建议随着《中国制造2025》技术路线图的深化实施,建议从三方面推进技术升级:首先,开发基于量子传感的纳米级宽度检测模块,攻克半导体光刻胶涂布精度难题;其次,构建跨行业产能共享平台,实现宽幅设备的多领域复用;最后,建立国家级的有效宽度数据库,为产业政策制定提供数据支撑。预计到2028年,该技术将使我国宽幅制造领域年节材量达1200万吨,对应减少碳排放1800万吨,为新型工业化建设注入强劲动能。
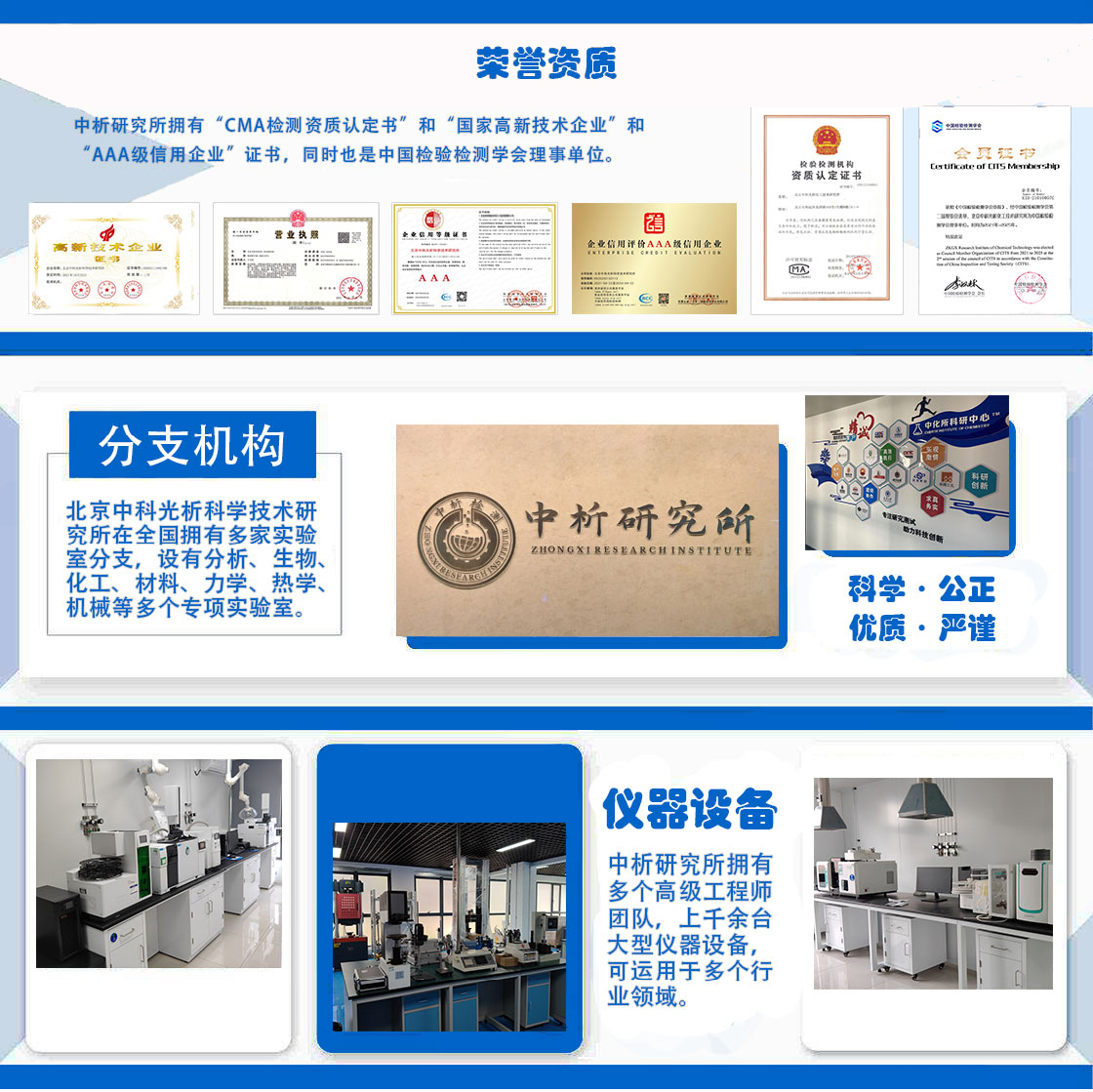
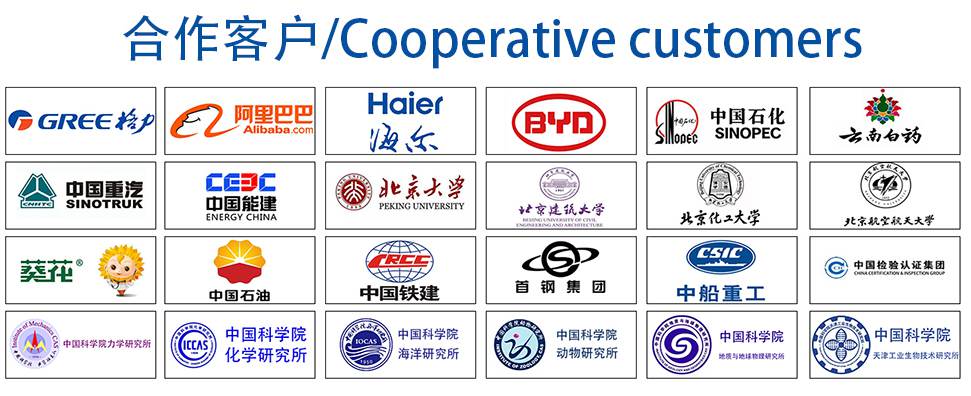