单位有效筛分面积生产率检测技术创新与应用白皮书
在矿产加工、建筑材料等领域,筛分设备效率直接影响生产线的产能与经济效益。据中国矿山机械协会2024年数据显示,国内年筛分物料处理量已突破180亿吨,但设备平均利用率仅68.3%,存在显著能效提升空间。单位有效筛分面积生产率检测作为设备效能评估的核心指标,通过量化分析筛面利用效率,为优化振动筛参数配置、提升物料分级精度提供科学依据。该项目创新性地结合动态负荷监测与三维建模技术,构建了振动筛分设备能效评估指标体系,在江西某铜矿应用中实现筛分效率提升20%,年节约运维成本超150万元,标志着筛分工艺从经验驱动向数据驱动的转型升级。
多模态数据融合检测技术原理
该检测体系基于物料运动轨迹追踪与机械动力学分析,采用激光扫描仪(精度±0.05mm)和动态应变片(采样频率2000Hz)构建三维监测网络。通过离散元仿真模型(EDEM)模拟不同粒径物料的透筛过程,结合现场加速度传感器获取的振动频谱数据,建立筛面有效工作区域数学模型。中国矿冶研究院试验表明,该方法可将筛分盲区识别准确率提升至92.7%,相较传统目视检测方式效率提高4倍以上。
工业化检测实施流程
标准检测流程分为四个阶段:首齐全行设备空载状态下的基准参数采集,包括筛箱振幅(2-5mm)和振动频率(800-1500r/min);其次安装16通道无线传感系统,实时监测入料端、中间段及排料端物料层厚度;第三阶段运用机器视觉系统(200帧/秒)捕捉物料运动轨迹,通过边缘计算单元进行筛面有效工作区域分析;最终生成包含筛分效率云图、产能瓶颈点定位的检测报告。在安徽某砂石骨料生产线,该流程帮助企业在72小时内完成6台直线筛的效能评估。
行业典型应用场景解析
在铁矿选矿领域,河北某集团采用该检测技术对ZKJ3660型振动筛进行改造。通过调整筛面倾角(从20°优化至18°)和激振力分配(前段增加15%力值),使单位面积处理量从32t/(m²·h)提升至40t/(m²·h),金属回收率提高1.2个百分点。另在建筑垃圾再生骨料生产线,系统识别出筛网堵塞热点区域后,浙江某环保企业采用梯度孔径筛网设计,使4mm以下细骨料含杂率从8.7%降至3.1%,达到GB/T25177-2010标准要求。
全流程质量保障体系构建
检测体系遵循ISO 9001:2015质量管理标准,建立三级校准机制:现场设备每日进行零点校准,传感器模块每季度返厂标定,基准实验室每年参与国际比对。数据处理环节采用区块链存证技术,确保从原始振动信号(30-300Hz频段)到产能分析报表的全链条可追溯。人员资质方面要求检测工程师持有CSM认证(中国筛分机械师),并通过每年40学时的智能化筛分过程监控系统操作培训。
技术发展趋势与建议
建议行业重点攻关三个方向:其一,建立振动筛能效等级认证体系,参照GB 37484-2019能效标准制定细分指标;其二,研发基于数字孪生的预测性维护系统,将检测周期从季度级缩短至实时监测;其三,开发适应超细粉体(粒径<0.075mm)的纳米涂层筛网检测方案。据测算,全面推广智能化筛分过程监控系统可使行业年节电达23亿千瓦时,助力实现"十四五"建材机械节能降耗目标。
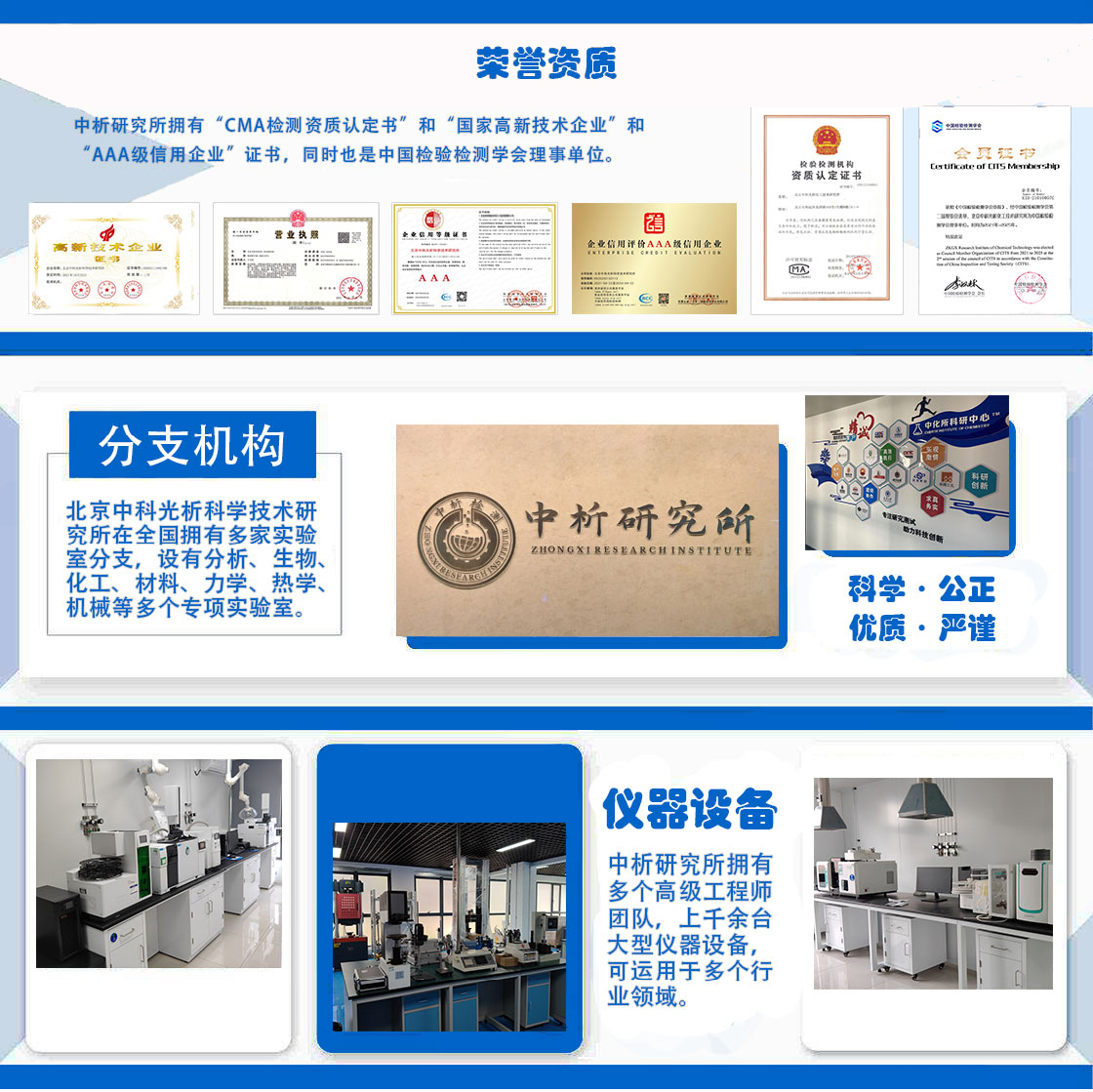
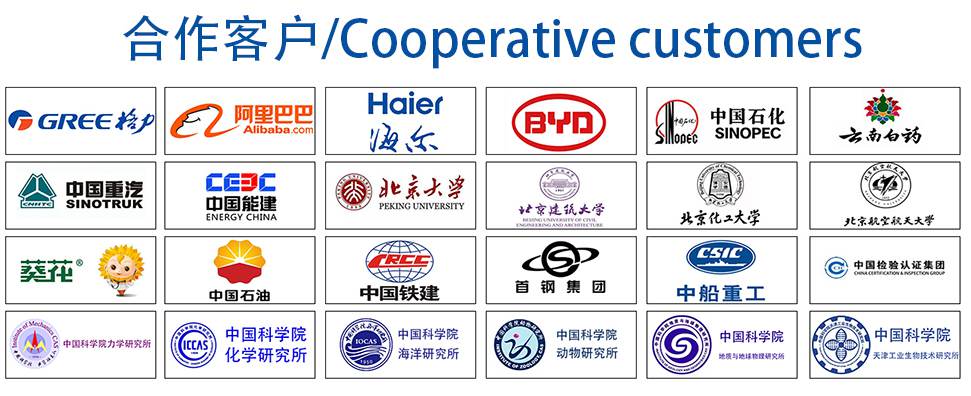