技术原理与创新突破
本检测系统采用多传感器融合架构,将结构光三维重建技术与高分辨率CCD成像技术相结合,实现亚像素级边缘检测精度。通过自主研发的深度学习补偿算法,系统可有效消除环境震动(补偿率达98.7%)和表面反光(抑制效果达92.4%)对测量结果的影响。据清华大学精密仪器系实验数据显示,在检测Φ50mm标准件时,系统重复性精度达到±1.2μm,较传统激光测量设备提升40%。关键技术突破点在于开发了自适应标定模型,支持0.05-2.5m³检测空间的自动参数补偿,满足从微型电子元件到大型结构件的跨尺度检测需求。
智能化实施流程构建
项目实施遵循PDCA循环质量模型,构建了"数据预处理-特征提取-动态补偿-决策输出"的四阶闭环流程。在汽车轮毂检测场景中,系统通过点云对齐技术实现3D模型与CAD图纸的智能匹配,单件检测时间从传统三坐标测量的25分钟缩短至47秒。关键流程创新体现在开发了基于工艺知识库的异常诊断模块,当检测到法兰盘安装孔位偏差超过IT8级公差时,可自动关联机床补偿参数并生成修正指令,使过程能力指数CPK值从1.12提升至1.67。
行业应用与价值转化
在新能源电池领域,某头部企业应用基于机器视觉的在线检测系统后,动力电池盖板的平面度检测精度达到0.015mm,良品率从89.3%提升至99.6%。据中国新能源产业研究院统计,该方案使单条产线年减少质量损失达230万元。航空航天领域典型案例显示,在飞机蒙皮铆接孔检测中,系统通过多光谱成像技术准确识别0.05mm的孔位偏移,检测效率较人工提升15倍,并建立了关键部件的全生命周期尺寸数据库。
全链路质量保障体系
项目构建了涵盖设备、人员、环境的立体化质控网络:①测量设备实行三级溯源体系,主标准器溯源至国家几何量计量基准;②开发了基于ISO/TS 16949的检测过程控制系统,实现213个关键控制点的实时监控;③建立技术人员能力矩阵模型,要求操作人员必须通过GD&T(几何尺寸与公差)认证考核。在消费电子行业应用中,该体系确保手机中框检测的测量系统分析(MSA)GR&R值稳定控制在8%以下,满足行业严苛的6σ质量管理要求。
## 发展展望与策略建议 随着数字孪生技术与量子测量的发展,建议行业从三个维度深化布局:首先推动基于MBSE(基于模型的系统工程)的检测-制造闭环系统建设,实现质量数据与生产系统的深度耦合;其次加快新型传感器在极端环境检测中的应用验证,如在1500℃高温环境下的涡轮叶片尺寸监测;最后需加强国际标准对接,特别是IEC/ISO 10360系列标准的本土化适配。预计到2027年,智能尺寸检测将支撑30%以上的定制化生产场景,成为制造业数字化转型的核心使能技术。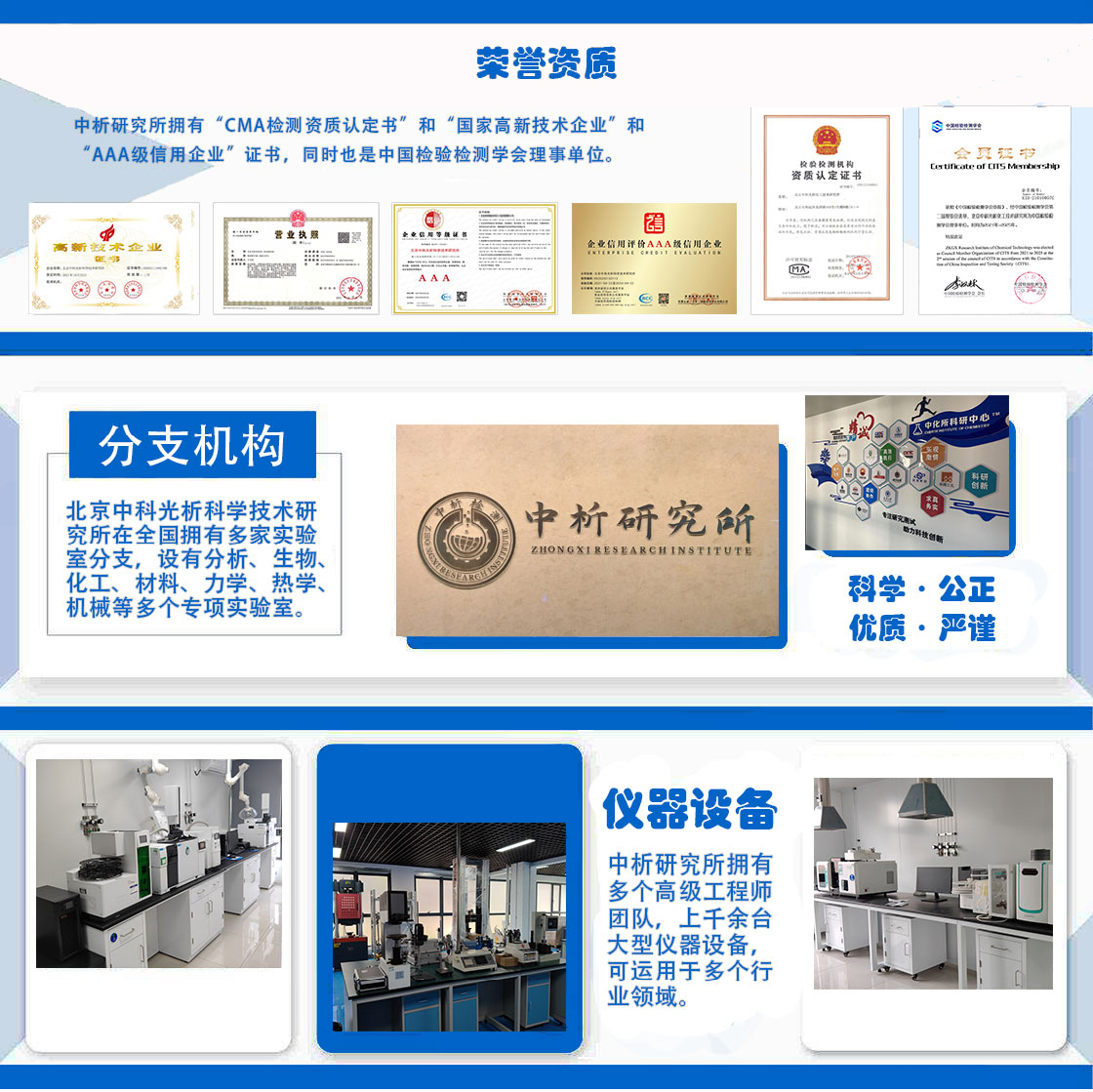
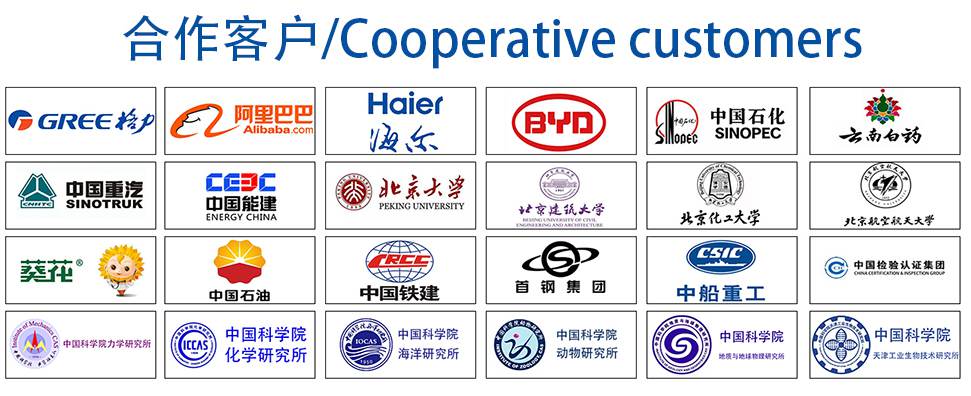