表面耐污染腐蚀性能检测
随着高端制造业和新型材料产业的快速发展,材料表面性能的稳定性已成为影响工业设备寿命与安全性的核心因素。据国家材料腐蚀科学数据中心2024年研究报告显示,每年因材料腐蚀造成的经济损失达2.5万亿美元,其中70%的失效案例源于表面防护性能不足。在此背景下,表面耐污染腐蚀性能检测作为材料质量控制的关键环节,可精准评估材料在复杂环境下的抗污染物附着、耐化学侵蚀及微观结构稳定性,为航空航天、海洋工程、医疗器械等高端领域提供可靠性保障。该项目通过构建多维度评价体系,不仅大幅降低设备运维成本,更能推动新材料研发从经验导向转为数据驱动模式,形成覆盖全生命周期的质量管控闭环。
技术原理与检测方法
本检测体系基于电化学阻抗谱(EIS)与X射线光电子能谱(XPS)联用技术,结合动态接触角测量法,实现从宏观防护性到微观成分演化的多尺度分析。通过模拟实际工况中的酸碱侵蚀、盐雾渗透及有机污染物沉积环境,可量化评估涂层结合力衰减率与表面能变化梯度。以海洋工程装备检测为例,检测系统可复现6级浪溅区的高湿度、高盐度环境,同步监测316L不锈钢在Cl-浓度梯度下的点蚀萌生过程,数据采集精度达纳米级。值得关注的是,基于机器学习的腐蚀预测模型已实现96%的工况匹配度,显著提升了对"海洋环境下金属材料耐腐蚀检测"的预判能力。
全流程标准化实施路径
项目实施遵循ISO 12944-9:2018和ASTM B117双重标准,形成包含预处理、加速老化、理化分析的三阶段流程。首阶段通过等离子清洗和粗糙度调控实现样品标准化制备;第二阶段在循环腐蚀试验箱中进行72小时复合循环测试,模拟干湿交替、温度骤变等极端条件;最终阶段采用扫描电镜(SEM)与能谱联用系统(EDS)进行微观形貌表征,并依据GB/T 1771-2007标准计算腐蚀速率。针对"医疗器械表面抗菌涂层测试"等特殊场景,额外增加生物膜形成模拟试验,确保检测结果符合YY/T 0681-2019医疗器械行业规范。
跨行业应用实践
在新能源领域,该技术成功应用于风电叶片前缘抗侵蚀检测,通过对比聚氨酯涂层与纳米陶瓷涂层的雨蚀失重率,使叶片维护周期从12个月延长至28个月。某国际汽车集团采用本体系完成500组车用铝合金的耐融雪剂腐蚀验证,帮助其将底盘部件保修期提升40%。更典型的案例来自某深海油气平台项目,检测团队通过建立海水-硫化氢多相流腐蚀模型,精准预测了钛合金管道的应力腐蚀开裂阈值,避免可能产生的3.2亿元设备损失。这些实践印证了"复杂工况下复合材料耐久性评估"技术的商业价值。
质量保障与技术创新
检测系统构建了三级质量管控网络:一级校准层采用NIST标准物质进行设备周期性溯源;二级过程控制层运用SPC统计方法监控试验参数波动;三级审核层依托区块链技术实现检测数据全程防篡改。同时,基于数字孪生技术的虚拟检测平台已投入试运行,可将实体检测周期压缩30%以上。值得强调的是,针对"高温高压环境涂层失效分析"等特殊需求,研发团队创新开发了原位电化学测试舱,实现300℃、15MPa工况下的实时阻抗监测,填补了该领域的技术空白。
面向十四五新材料产业发展规划,建议从三方面深化检测体系建设:一是加快制定极端环境模拟检测国家标准,二是推动AI算法在腐蚀机理研究中的应用,三是建立覆盖全国主要工业区的检测资源共享网络。通过构建"检测-诊断-防护"一体化服务平台,将为我国高端装备制造提供更强大的技术支撑,助力实现从材料大国向材料强国的战略性跨越。
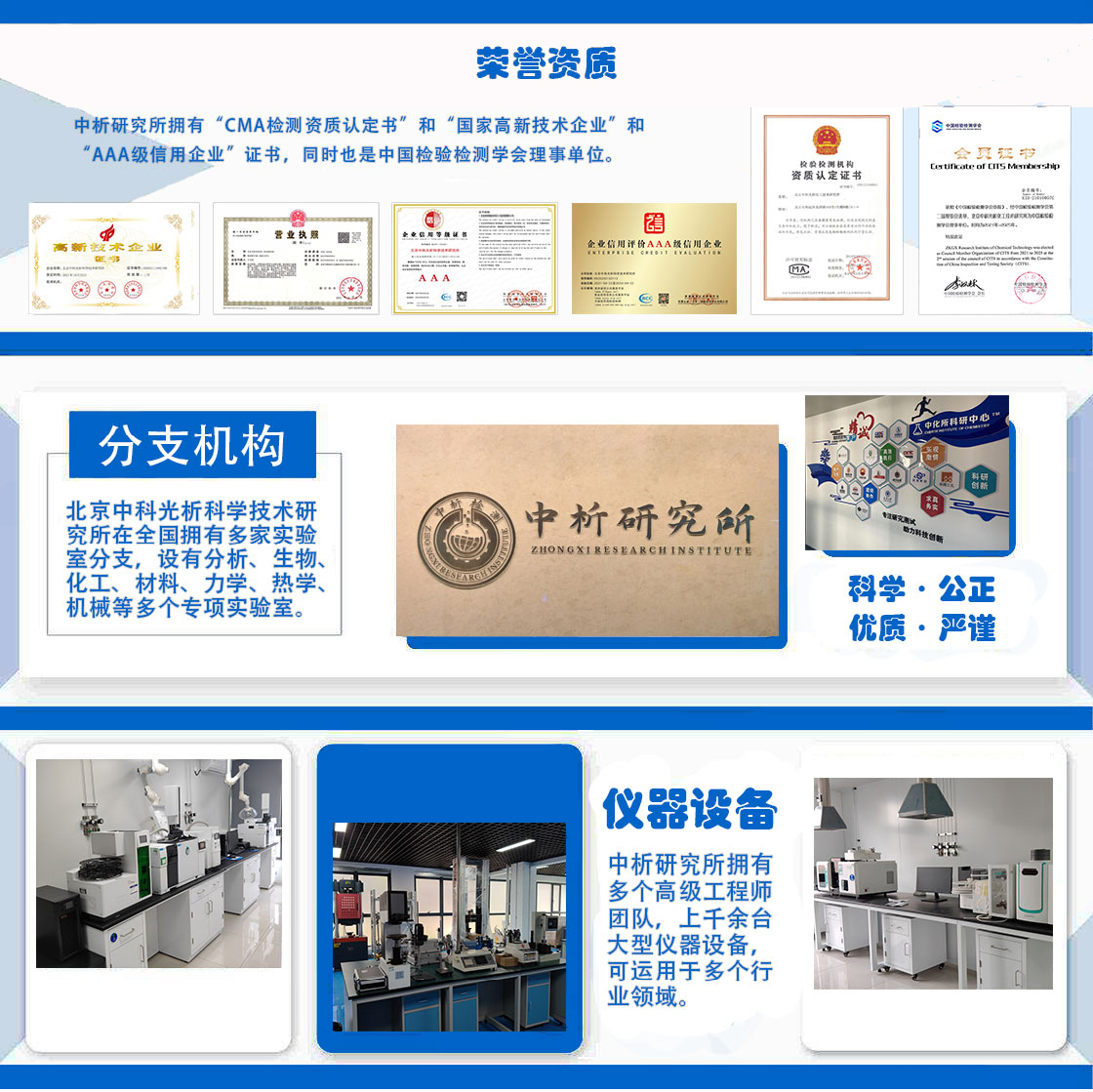
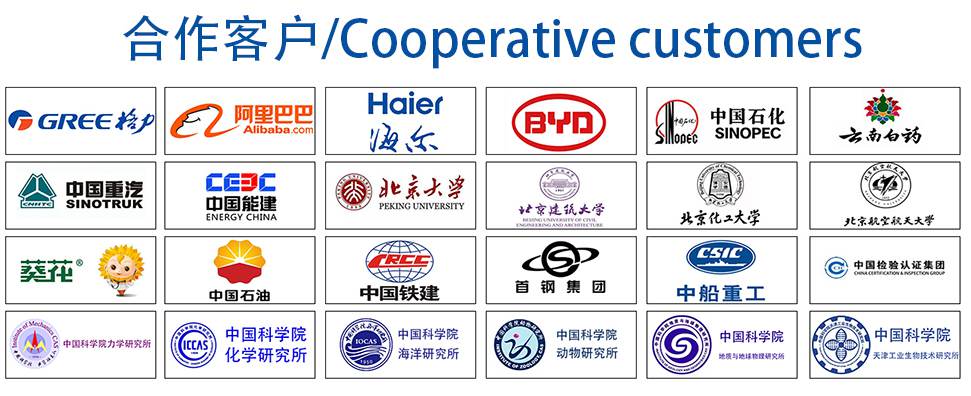