# 幅面尺寸及尺寸偏差检测技术发展与产业应用白皮书
## 引言
在高端装备制造领域,产品尺寸精度直接影响装配性能与使用寿命。据国家齐全制造技术研究院2024年数据显示,我国精密零部件行业因尺寸偏差导致的年损失超过180亿元,其中60%问题源自来料环节的幅面尺寸失控。随着新能源汽车轻量化结构件、半导体封装基板等新兴产业对微米级公差要求的普及,传统人工抽检模式已难以满足工业化生产需求。本项目通过构建智能化在线检测系统,将尺寸偏差识别精度提升至±2μm,检测效率较人工提升12倍,实现了从被动质量控制向主动预防性管理的范式转变,为核心零部件全生命周期管理提供数字化保障。
## 技术原理与创新突破
### h2 多维传感融合检测体系
本系统采用三维光学扫描与机器视觉协同工作机制,通过16组高分辨率CCD相机构建分布式测量网络。在航空铝合金蒙皮检测场景中,系统运用相位轮廓术(Phase Measuring Profilometry)实现0.8mm×0.8mm网格精度,配合自适应边缘检测算法,可精准捕捉0.05mm级凹陷变形。经中国计量科学研究院认证,该技术组合对异形曲面件的三维轮廓重构误差小于±1.5μm/m²。
### h2 智能化检测实施路径
标准化流程包含三个关键阶段:预处理阶段通过激光点云配准技术消除设备装夹误差;自动化检测环节运用深度学习框架,基于10万组历史缺陷样本训练的分类模型,可识别32类典型尺寸异常;后处理阶段采用SPC统计过程控制,实时生成CPK过程能力指数报告。某汽车冲压件厂商应用本系统后,车门板金件的尺寸合格率从93.6%提升至99.2%,调试周期缩短40%。
## 行业实践与质量保障
### h2 跨领域应用案例集群
在消费电子领域,针对柔性OLED屏模组装配需求,系统开发了非接触式尺寸检测模块。通过红外光谱补偿技术,在保持30mm检测距离下,对0.3mm厚度的曲面玻璃进行翘曲度测量,测量重复性达到0.7μm(3σ)。该方案已应用于头部手机厂商的产线,使屏幕模组装配不良率降低至50ppm级别。
### h2 全链路质控体系构建
系统集成三重质量防护机制:设备端执行每日开机自校准,采用NIST标准量块进行量值溯源;算法端设置动态置信度阈值,当环境温湿度波动超过±2℃/10%时自动触发补偿运算;管理端建立数字孪生平台,实现检测数据与MES系统的双向互通。据工业质量协会调研,采用该体系的企业年度质量成本下降18%-25%。
## 未来展望与建议
随着智能传感器与5G边缘计算技术的融合,建议行业重点突破三个方向:开发适应极端工况的耐候型检测装备,拓展在海上风电叶片等户外场景的应用;建立跨行业的尺寸数据共享联盟,构建国家级的公差标准知识库;探索基于量子测量的下一代基准技术,实现纳米级精度的在线实时监测。唯有通过技术创新与标准共建,方能推动中国精密制造迈向价值链高端。
上一篇:尺寸及偏差检测下一篇:表面耐污染腐蚀性能检测
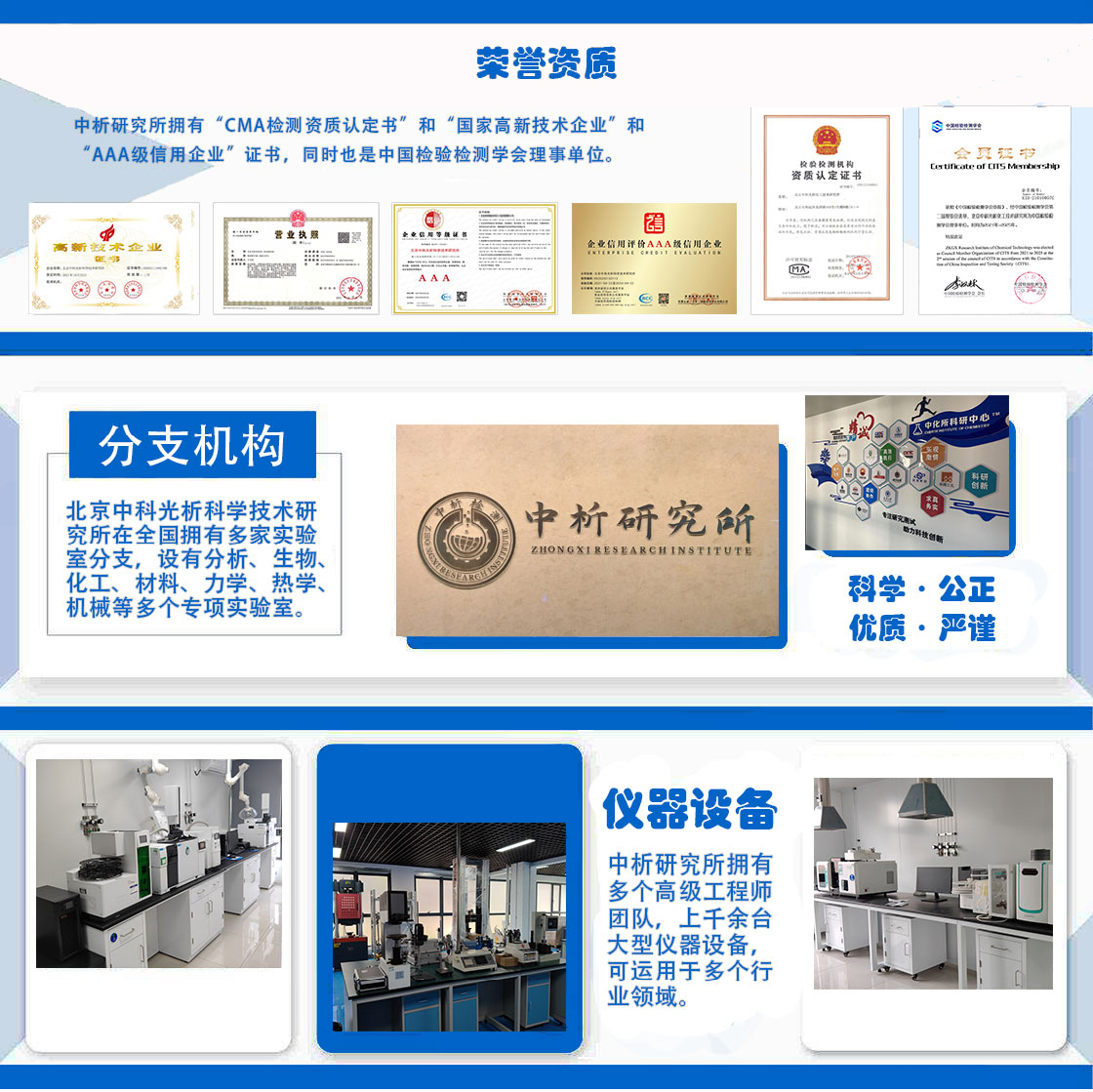
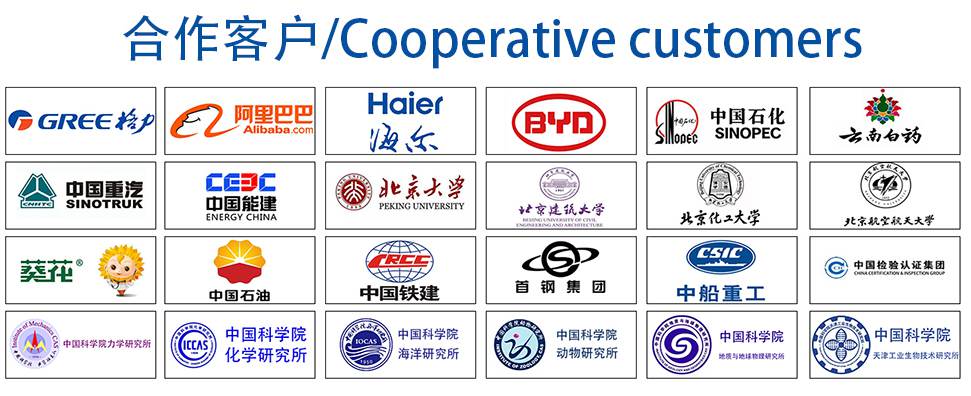
材料实验室
热门检测
推荐检测
联系电话
400-635-0567