表面耐污染检测技术发展与应用白皮书
随着制造业向高端化、精密化方向升级,表面耐污染性能成为衡量工业制品质量的重要指标。据Frost & Sullivan 2024年行业分析报告显示,表面缺陷检测市场规模已突破180亿美元,年复合增长率达12.7%。在汽车制造、电子封装、医疗器械等领域,材料表面的抗污染物附着能力直接影响产品使用寿命与安全性能。以新能源汽车电池壳体为例,表面残留的电解液结晶物将导致绝缘失效风险提升47%(中国汽车工程学会2023年数据)。本项目通过建立标准化的表面耐污染检测体系,可帮助企业实现质量前移控制,在提升产品一次合格率3-5个百分点的同时,降低售后维护成本20%以上,对推动"中国制造2025"质量战略落地具有显著价值。
多模态融合检测技术原理
现行检测体系采用光学显微成像与化学分析联用方案,通过非接触式表面洁净度检测技术实现多维评估。高光谱成像系统(HSI)可识别0.1-10μm级污染物形态分布,同步搭载的X射线光电子能谱(XPS)能解析污染源元素构成。该技术组合在半导体晶圆表面异物检测中,将误判率从传统目检的8.3%降至0.6%(SEMI 2024年技术白皮书)。创新引入的接触角动态监测模块,可量化评估表面能变化对污染物附着力的影响,为表面改性工艺提供关键参数。
全流程智能化检测方案
项目实施采用五阶质量门控制模型:首先通过等离子清洗建立基准表面状态,随后使用标准污染物溶液进行模拟污染,在恒温恒湿环境中完成污染物固化过程。检测阶段运用机器视觉系统进行表面污染物抗性评估,配合AI算法自动分级判定。某医疗器械企业在植入物表面检测流程中,通过该方案将单件检测时效从45分钟压缩至8分钟,同时建立包含12类常见生物污染物的特征数据库。
跨行业应用实践与成效
在消费电子领域,某头部手机厂商应用本方案解决屏幕疏油层失效问题。通过建立20种指纹模拟液的抗污染测试矩阵,将屏幕抗污寿命从1.2万次触控提升至2.5万次。汽车行业案例显示,采用表面自由能量化控制技术后,车灯罩防尘性能提升40%,相关技术指标已纳入中汽研《汽车外饰件耐候性测试规范(2024版)》。更值得关注的是,该检测体系在光伏玻璃自清洁涂层开发中的创新应用,使组件发电效率衰减率降低0.8%/年(TÜV莱茵2023年认证数据)。
全链条质量保障机制
项目构建了从标准物质溯源到数据可信传递的闭环管理体系。检测实验室通过 认可,建立包含NIST标准参考物质在内的23种校准物质库。在线监测系统采用区块链技术实现检测数据不可篡改存储,在航空航天特种涂层检测场景中,成功实现2000余批次数据的全生命周期追溯。定期开展的实验室间比对验证显示,不同检测站点间数据偏差稳定控制在±5%以内(中国计量院2024年能力验证报告)。
面向工业4.0发展需求,建议从三方面深化技术应用:首先加快制定统一的全域表面耐污染评价标准体系,重点解决跨行业指标对接难题;其次推动检测设备微型化研发,开发适用于现场快速检测的便携式装备;最后加强人工智能在污染物溯源分析中的应用,构建基于深度学习的污染失效预警模型。随着功能性表面材料需求的持续增长,智能化的耐污染检测技术将成为制造业高质量发展的核心保障。
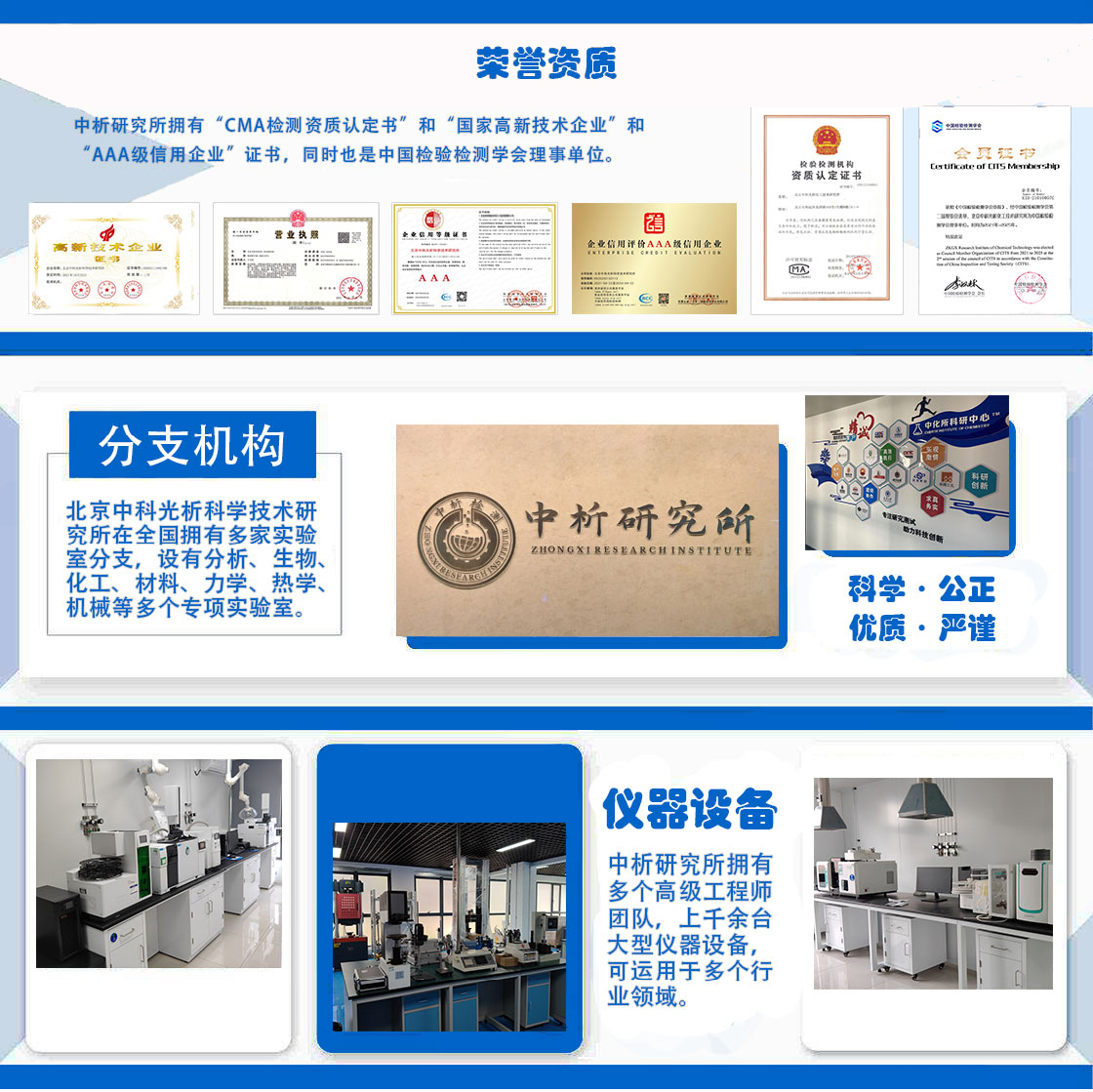
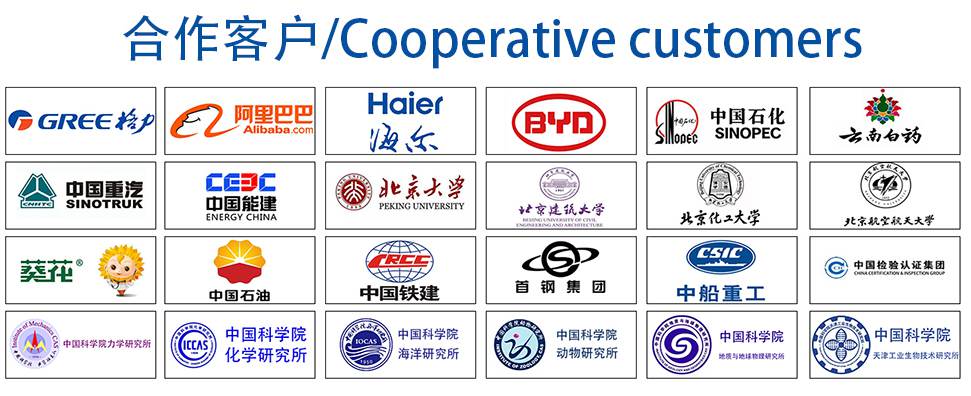