# 湿循环试验检测技术发展与应用白皮书
## 引言
在气候变暖和极端天气频发的背景下,材料与设备的环境适应性面临严峻考验。据国家可再生能源实验室2024年研究报告显示,光伏组件因湿热失效导致的年发电损失达37亿千瓦时,新能源汽车电池组在潮湿环境下的故障率较常规气候区域高出48%。湿循环试验检测作为评估材料耐久性的关键技术,通过模拟温湿度交替变化工况,可精准预测产品在全生命周期中的性能衰减规律。该技术不仅填补了传统恒温恒湿测试的缺陷,其核心价值更在于为光伏能源、电子电器、汽车制造等行业构建了全链路质量防护体系,据国际电工委员会统计,采用标准化湿循环检测的企业产品退货率平均降低22%,显著提升市场竞争力。
## 技术原理与实现路径
### 湿热交变环境模拟技术
湿循环试验依托闭环控制系统实现温湿度精准调节,采用PID算法控制蒸汽发生器和冷凝装置,可在48小时内完成20个循环周期(温度范围-40℃至85℃,湿度10%-95%RH)。特别针对光伏组件PID效应检测,系统集成1000V偏置电压施加模块,通过电化学阻抗谱分析玻璃-胶膜界面的离子迁移量。国际材料试验协会(ASTM)D7869标准规定,每个循环需包含4小时高温高湿(85℃/85%RH)与2小时低温干燥(-40℃/10%RH)的交替过程。
### 全流程检测实施方案
实施流程分为预处理(48h标准环境平衡)、参数设定(基于IEC 61215标准建立梯度模型)、过程监控(多点温湿度传感器误差≤±1.5%RH)和失效分析四个阶段。某头部新能源车企的电池包测试案例显示,经过50次湿循环后采用X射线断层扫描(CT)检测,成功定位电解液渗漏路径,将封装工艺缺陷检出率提升至99.3%。测试过程中同步采集的ECU数据与红外热成像结果形成多维验证矩阵。
### 行业应用效能分析
在光伏领域,天合光能采用改进型湿循环方案后,双玻组件湿热衰减率从1.8%/年降至0.5%/年。电子行业典型案例显示,华为海思某5G基站芯片经100次循环测试,焊点抗剪强度保持在初始值的92%以上。更为突出的是,中车集团将测试周期压缩至行业标准的60%,通过建立湿度冲击响应模型,准确预测了高铁受电弓碳滑板在沿海气候下的磨损曲线。
## 质量控制与标准化建设
检测体系构建需满足 -CL01:2018准则,核心设备每季度进行NIST溯源校准。人员资质方面要求检测工程师持有IPC J-STD-033证书,并定期参与ISTA组织的循环比对试验。数据管理系统采用区块链存证技术,确保测试报告的不可篡改性。值得关注的是,中国质量认证中心(CQC)2023年推出的分级认证制度,将湿循环测试结果纳入产品环境适应性星级评价体系。
## 发展建议与未来展望
建议行业重点发展三方面能力:一是开发智能传感器融合的数字化检测平台,实现测试参数的动态优化;二是建立多因素耦合模型,整合紫外线辐射、盐雾腐蚀等环境应力;三是推动军用标准GJB150.9A向民用领域转化。据麻省理工学院材料系预测,到2028年自适应环境模拟舱的市场渗透率将突破45%,而搭载AI诊断算法的第四代湿循环设备可缩短30%的失效分析时间。行业需加快制定针对新型复合材料的标准测试程序,为"双碳"目标下的绿色制造提供技术保障。
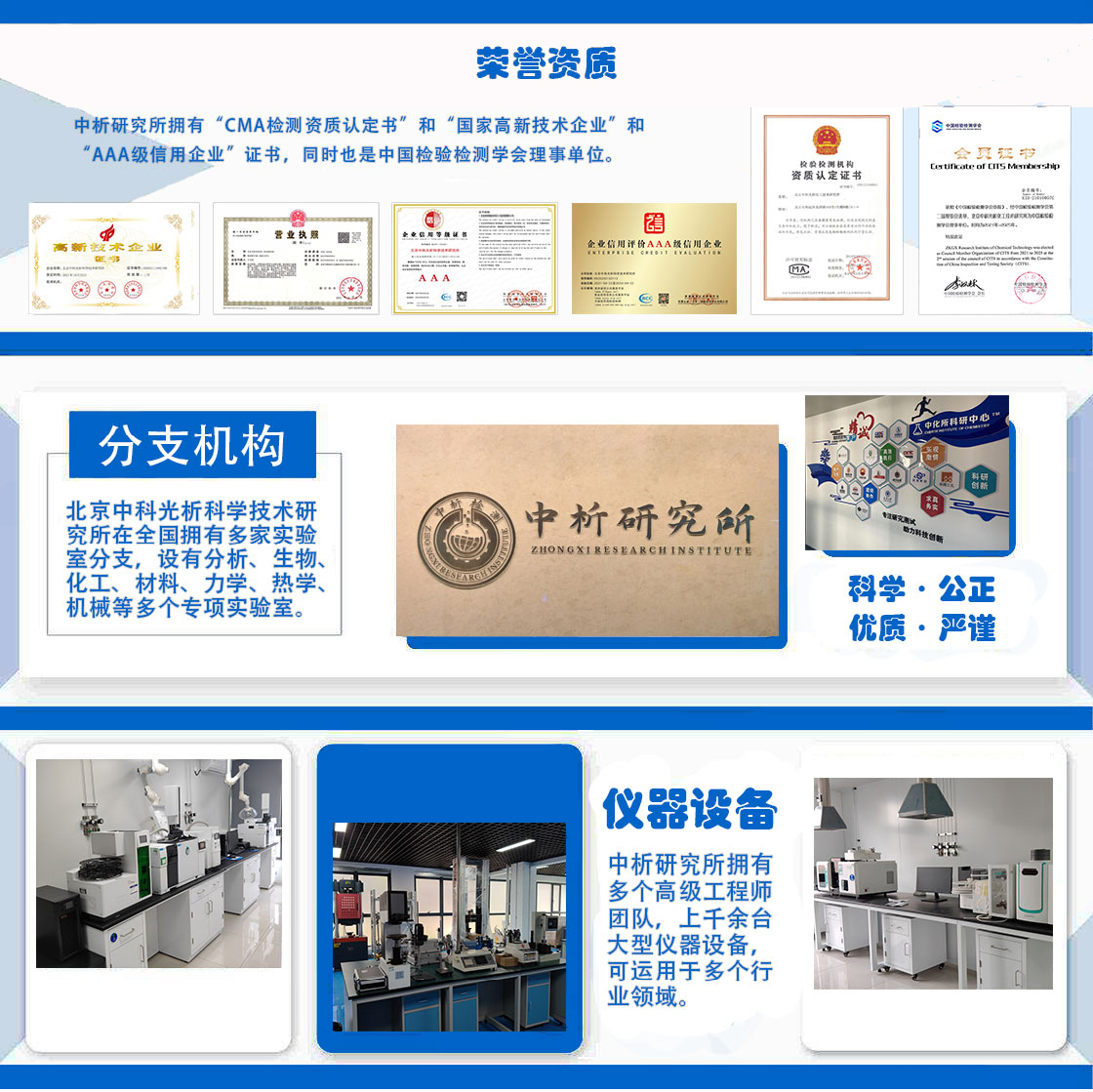
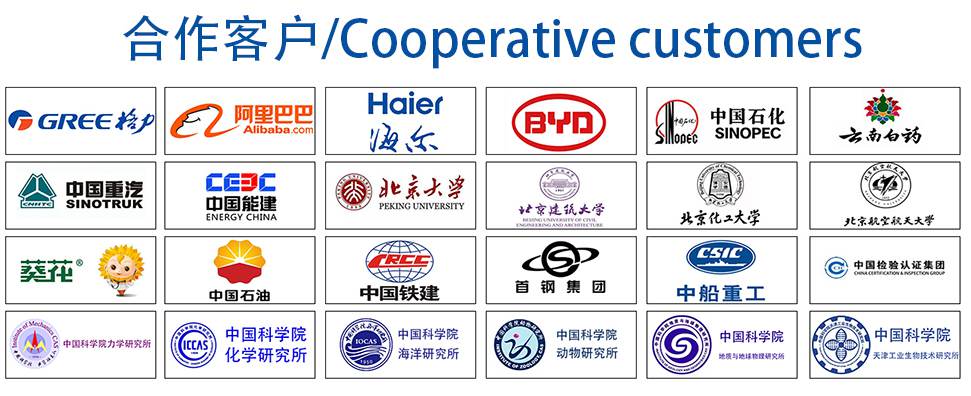
材料实验室
热门检测
7
10
15
15
12
16
33
33
25
35
38
38
23
32
47
47
10
16
16
15
推荐检测
联系电话
400-635-0567