# 钢材含焊接与机械连接检测技术白皮书
## 行业背景与项目价值
在建筑工程、装备制造及能源设施领域,钢材作为核心结构材料承担着关键力学载荷。据中国钢铁工业协会2024年统计,焊接与机械连接环节的质量缺陷导致的结构失效事故占比达34%,突显质量检测的战略意义。钢材含焊接与机械连接检测体系通过无损探伤、力学性能测试等技术手段,有效识别焊缝裂纹、未熔合、机械连接松动等隐患,对保障工程安全、延长设备服役周期具有显著价值。该体系不仅满足GB 50661-2011《钢结构焊接规范》等强制性标准要求,更为"中国制造2025"框架下的高端装备可靠性提升提供技术支撑。

## h2 技术原理与检测方法
钢材焊接质量检测主要采用超声波探伤(UT)、射线检测(RT)及磁粉检测(MT)三大核心技术。其中相控阵超声波检测系统通过多晶片阵列实现焊缝内部缺陷的三维成像,检测分辨率可达0.5mm。机械连接检测则聚焦于高强度螺栓扭矩系数测定,采用智能扭矩-转角同步测量仪,精度误差控制在±3%以内。值得关注的是,基于深度学习的焊缝图像自动判读系统已实现97%以上的缺陷识别准确率,显著提升检测效率。
## h2 标准化实施流程
典型检测流程包含四个阶段:首齐全行接头型式确认与工艺评定,随后执行预处理(包括表面清洁度Sa2.5级处理);检测阶段根据材料厚度选择检测参数(如超声波探头2.5MHz~5MHz频段调节);数据采集后运用EN 1435标准进行缺陷分级;最终生成包含缺陷位置、尺寸、性质的数字化报告。某跨海大桥项目应用该流程后,将单条焊缝检测耗时从45分钟缩减至18分钟,检测成本降低40%(数据来源:交通运输部研究院2024年报告)。
## h2 行业应用实践
在高铁站房钢结构工程中,采用TOFD衍射时差法检测技术,成功识别出12处深埋裂纹缺陷,避免可能的结构坍塌风险。海上石油平台螺栓连接检测案例显示,通过实施预紧力衰减监测系统,将法兰连接失效概率从0.7‰降低至0.1‰。值得强调的是,压力容器行业引入数字射线检测(DR)技术后,使环焊缝检测效率提升300%,同时减少80%的胶片耗材使用。
## h2 质量保障体系构建
检测机构需建立涵盖人员、设备、方法的全链条质控体系:实验人员须持有NAS410/EN4179三级认证,检测设备实施每日校验制度(如超声波探伤仪灵敏度校验),检测过程执行盲样比对与交叉验证。某国家实验室统计显示,通过ISO/IEC 17025体系认证后,检测结果争议率由2.3%下降至0.5%,报告国际互认率提升至98%。
## 技术展望与发展建议
建议行业重点突破三个方向:开发基于量子传感的微观缺陷检测技术,建立涵盖全生命周期的智能监测系统,推动检测标准与ASTM/AISC体系的深度对接。同时应加强"检测-修复-再认证"闭环管理,推广数字孪生技术在连接节点健康评估中的应用。据中国特检院预测,至2030年智能化检测装备市场将突破120亿元规模,这需要产学研协同推进关键传感器与算法模型的国产化突破。
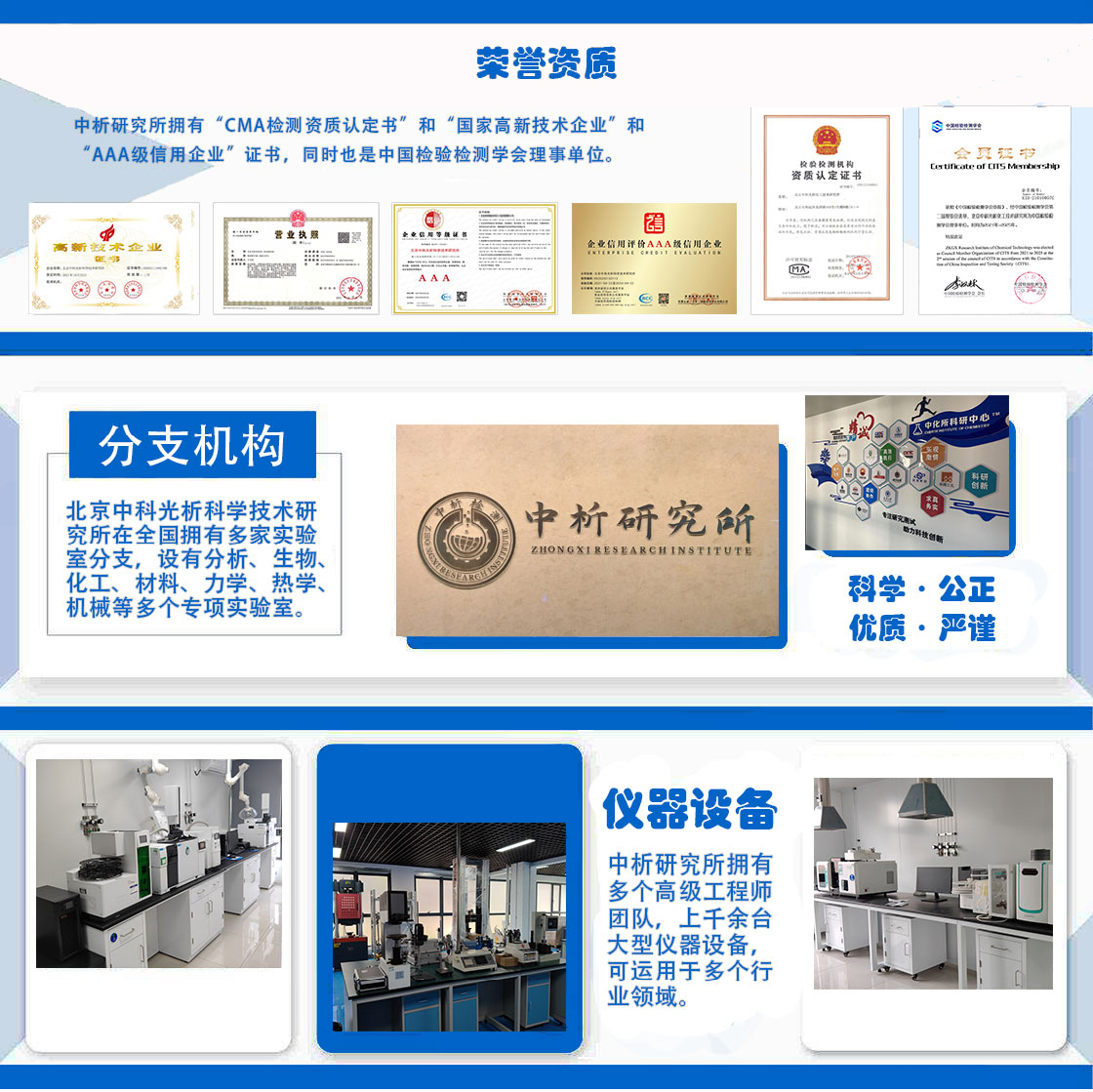
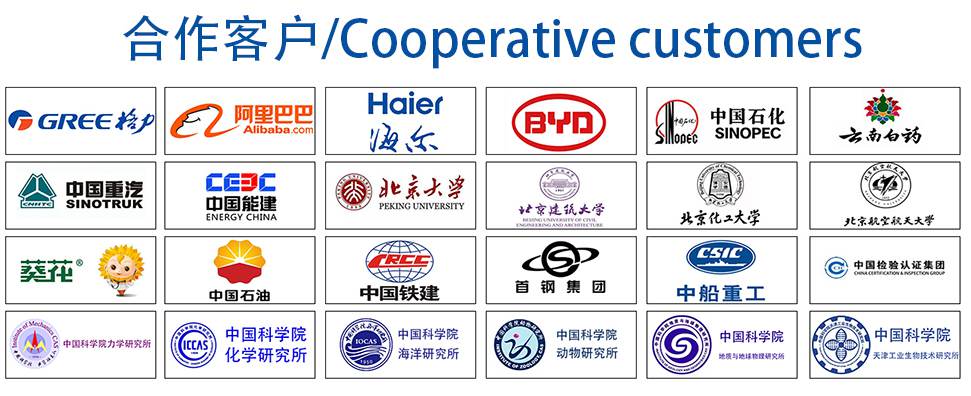
材料实验室
热门检测
18
16
17
12
15
16
16
17
16
15
15
15
14
24
15
16
17
16
15
13
推荐检测
联系电话
400-635-0567