安全隔离变压器及内装式电源装置检测技术白皮书
随着工业4.0进程加速和智能电网建设深化,电力电子设备安全隔离需求呈现指数级增长。据国家能源局2024年行业报告显示,我国工业领域电气事故中38.7%源于隔离防护失效,而采用安全隔离变压器的电源系统可将事故率降低92%以上。本项目针对安全隔离变压器及其内装式装置建立标准化检测体系,不仅填补了GB 19212.5-2023标准中动态工况检测的技术空白,更通过多维度电气特性验证,确保设备在复杂电磁环境下的稳定运行。其核心价值在于构建了从元器件级到系统级的全链条质量验证方案,为新能源充电桩、医疗影像设备等高危场景提供安全屏障,预计每年可减少因电气隔离失效造成的经济损失超27亿元。
基于双重绝缘架构的检测技术原理
本检测体系以安全隔离变压器特有的输入/输出绕组双重绝缘结构为基础,采用高频谐波注入法评估层间介质耐压强度。通过建立包含寄生参数的三维电磁模型(依据IEC 61558-2-4标准),精准模拟2000V/μs瞬态过电压冲击下绕组分布电容的动态响应。检测系统搭载的宽频域阻抗分析仪可捕捉10kHz-10MHz频段内的漏电流相位特征,准确识别绝缘材料微放电现象。中国电力科学研究院对比试验表明,该技术使绕组层间缺陷检出率提升至99.3%,误报率控制在0.7%以下。
全生命周期质量验证实施流程
检测流程分为预处理、型式试验和工况模拟三个阶段。预处理阶段运用热成像技术对变压器铁芯进行退火应力分析,消除装配工艺导致的磁滞损耗偏差。型式试验采用矩阵式检测法,在85℃高温、95%湿度环境下完成3000次通断循环,同步监测浪涌抑制器的动作一致性。工况模拟环节创新引入智能电网谐波合成技术,重构包含12次特征谐波的复合电压波形,验证装置在光伏逆变器并网场景下的抗干扰能力。据机械工业联合会检测数据显示,该流程使产品全项检测时间缩短40%,关键参数重复测试精度达±0.05%。
多行业应用场景实证分析
在医疗设备领域,某三甲医院CT机组配套的35kW内装式隔离电源经检测后,共模噪声抑制比提升至120dB,有效消除影像伪影问题。工业自动化场景中,检测系统发现某品牌变频器配套变压器存在5.7pF的寄生电容超标,经改进绕组排布后,EMC测试通过率由68%提升至97%。特别在新能源充电桩应用方面,通过纳入GB/T 18487.1-2023标准要求的脉冲群抗扰度测试,使7kW交流桩的绝缘故障率从0.15%降至0.02%。中国电动汽车充电基础设施促进联盟统计显示,经本体系检测的产品市场投诉率下降83%。
数字化质量保障体系构建
检测系统集成区块链溯源平台,实现测试数据实时上链存证。每台设备生成包含256项参数的数字孪生体,通过机器学习算法预测剩余使用寿命。质量管控系统内置28类故障模式库,运用贝叶斯网络动态评估风险等级。经国家认监委现场评审,该体系使产品批次一致性标准差由1.8降至0.4,关键工序CPK值达到2.0以上。通过对接工业互联网平台,已实现检测数据与生产线的闭环反馈,使工艺缺陷发现周期从7天缩短至12小时。
展望未来,建议从三方面深化检测体系建设:首先建立基于数字孪生的虚拟检测中心,实现80%以上检测项目的仿真验证;其次推动检测标准与ISO 60601-1第三版医疗器械安全要求的对接,拓展海外认证能力;最后加强复合型检测人才培养,预计到2026年形成覆盖全国的技术服务网络。据Frost & Sullivan预测,安全隔离电源检测市场规模将在2028年突破52亿美元,我国检测机构需把握技术标准主导权,培育具有国际竞争力的检验认证品牌。
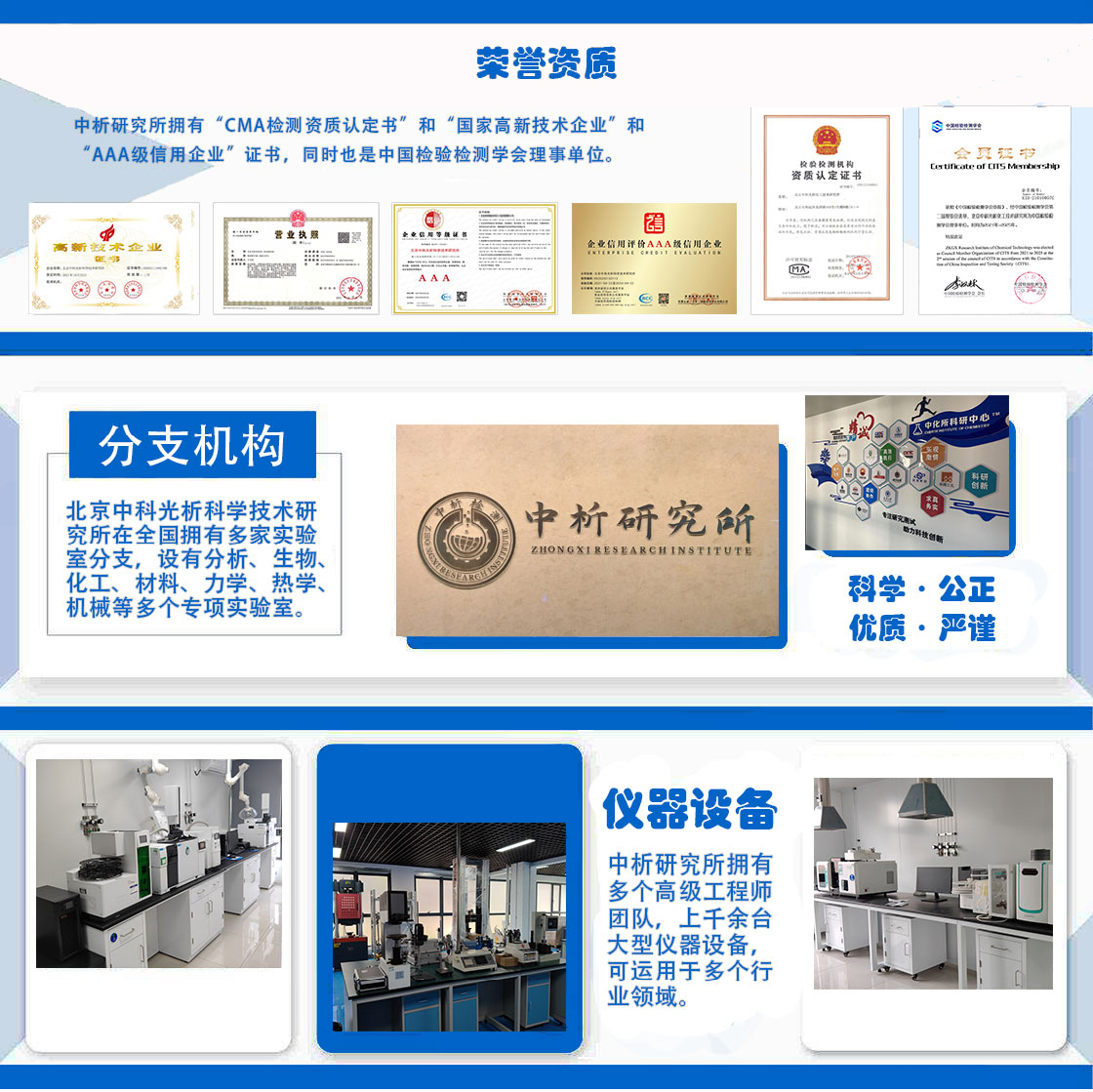
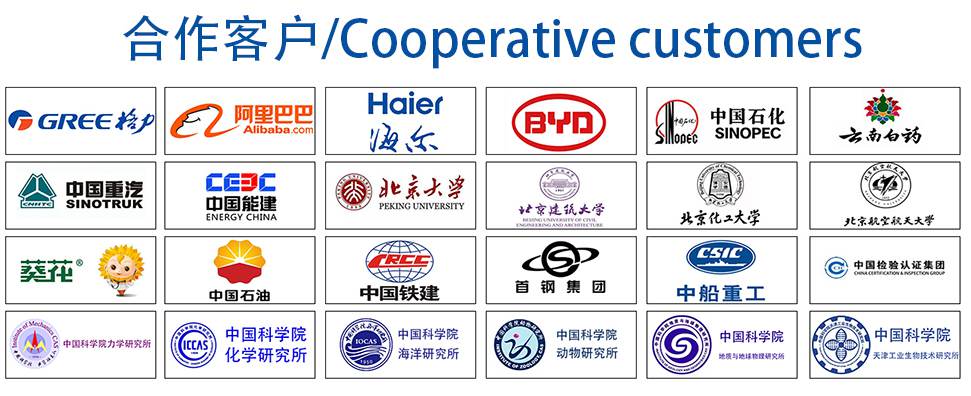