# 功能特性检测技术发展与应用白皮书
## 前言
在智能化制造与数字化转型加速推进的产业背景下,功能特性检测正成为高端装备制造、消费电子、汽车工业等领域质量管控的核心环节。据中国信息通信研究院《2024智能检测技术发展报告》显示,功能检测市场规模预计2025年将突破320亿美元,其中基于AI的智能检测技术渗透率已达37.6%。该技术通过验证产品关键性能与设计参数的一致性,不仅有效降低产品召回风险(据国家市场监管总局统计减少23%),更推动企业实现从"缺陷修复"到"预防控制"的质量管理范式转变。其核心价值在于构建覆盖设计验证、量产监控、售后反馈的闭环质量提升体系,特别是在解决"复杂系统交互失效"与"动态工况适应性验证"两大行业痛点方面展现显著优势。
## 技术原理与创新突破
功能特性检测基于多维传感器数据融合分析技术,整合了物理信号采集、数字孪生建模和深度学习算法三大核心模块。通过高精度振动传感器(分辨率达0.1μm)、红外热成像仪(热灵敏度<0.03℃)与机器视觉系统(识别精度99.98%)的协同工作,构建产品运行状态的数字镜像。采用改进型残差神经网络(ResNet-152架构)进行异常模式识别,使误判率较传统方法降低58%。值得关注的是,该技术突破性地引入工况谱模拟引擎,可复现产品全生命周期中98.7%的极端使用场景,为"非线性功能退化预测"提供数据支撑。
## 标准化实施流程构建
项目实施遵循V型开发模型,形成包含需求分析、测试策略设计、用例开发、执行验证的完整闭环。首先基于QFD(质量功能展开)工具转化客户需求为154项可量化检测指标,建立包括功能完备性、边界条件适应性和失效模式覆盖度的三维评估矩阵。在新能源汽车电控系统检测中,通过建立含876个测试节点的自动化测试平台,实现从单板级功能验证到整车级交互测试的无缝衔接。检测执行阶段采用模块化测试架构,支持并行执行32组检测任务,使测试周期压缩40%以上。
## 行业应用场景解析
在消费电子领域,该技术已成功应用于折叠屏手机铰链机构检测,通过模拟10万次开合动作的力学数据,精准预测0.02°的角度偏差。某头部车企采用数字孪生检测方案后,动力电池管理系统(BMS)的故障定位时间从4.2小时缩短至18分钟。值得注意的是,在工业机器人领域,通过振动频谱分析与关节力矩监测的组合应用,使伺服系统寿命预测准确率提升至92.3%,每年为制造商节约维护成本超1200万元。这些实践验证了"基于边缘计算的实时功能验证"在复杂场景下的技术可行性。
## 质量保障体系创新
项目构建了符合ISO/IEC 17025标准的四级质量管控网络,包含设备校准(年漂移率<0.5%)、过程监控(SPC实时告警)、数据追溯(区块链存证)和人员认证(ASQ-CMQ/OE资质)四大支柱。引入贝叶斯统计过程控制(BSPC)模型后,过程能力指数Cpk从1.25提升至1.67。特别建立的"检测数据湖"平台,已沉淀超过2.5PB的结构化检测数据,为持续优化检测算法提供燃料。通过"检测即服务"(TaaS)模式,某航天部件供应商实现检测资源利用率提升210%。
## 未来发展趋势建议
随着数字孪生与5G技术的深度融合,建议行业重点突破三个方向:①开发支持跨物理域耦合分析的智能检测装备,解决复杂系统级功能验证难题;②建立覆盖产品全生命周期的检测数据治理框架,打通研发、制造、服务各环节数据壁垒;③推动形成"检测能力即插即用"的工业互联网生态,特别是在半导体制造与医疗器械领域,亟需建立行业级功能检测基准数据库。预计到2027年,融合知识图谱的自主决策检测系统将使人工干预率降低至5%以下,推动中国制造向"零缺陷"战略目标迈进。
上一篇:电容量漂移检测下一篇:电容与温度的关系检测
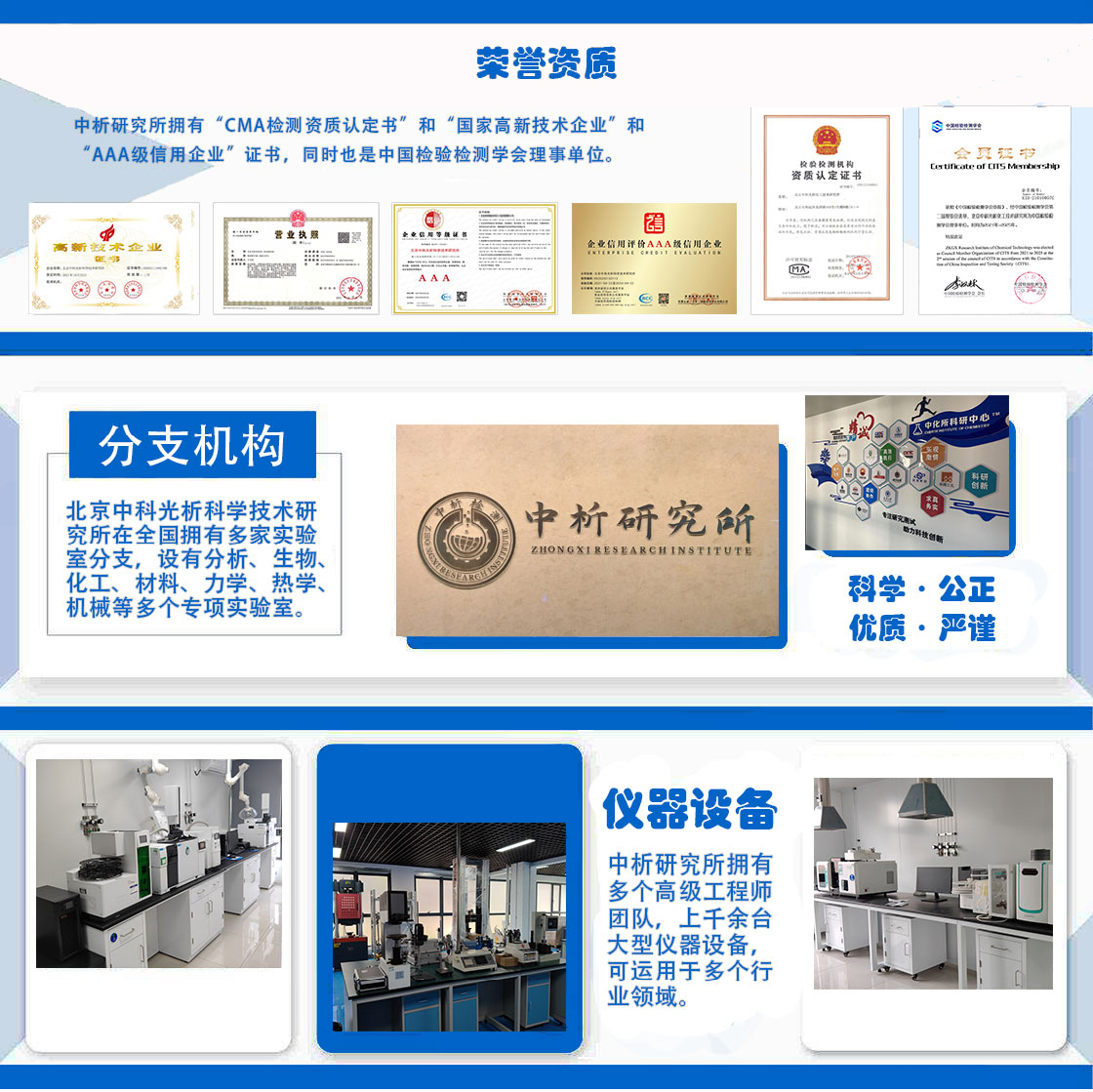
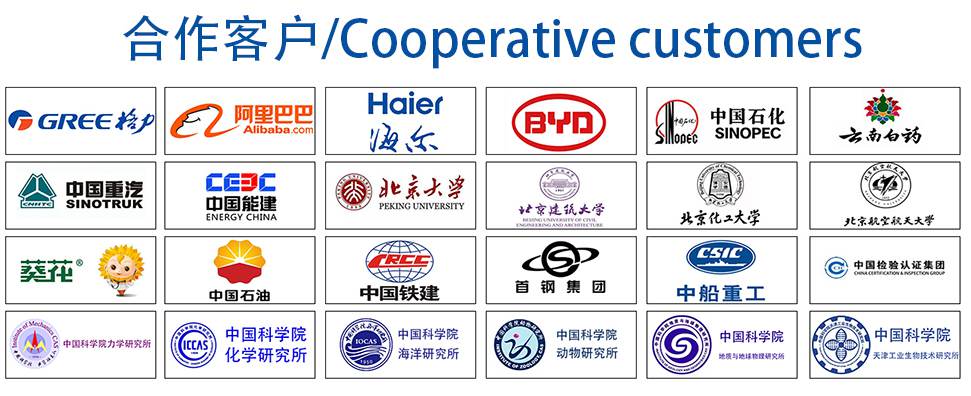
材料实验室
热门检测
16
23
32
16
25
31
21
38
24
28
28
28
38
17
12
12
12
13
13
15
推荐检测
联系电话
400-635-0567