快速温度变化:两液槽法(非破坏性的)检测技术白皮书
在电子元器件、新能源汽车及航空航天等高端制造领域,产品可靠性验证面临极端温度环境的严苛挑战。据中国电子技术标准化研究院2024年数据显示,因温度冲击导致的电子设备故障占比达32%,直接经济损失超180亿美元。两液槽法快速温变检测技术采用非破坏性测试方案,通过双介质热传导实现-65℃至+150℃的瞬时切换,在保障样品完整性的前提下完成产品耐候性验证。该技术突破传统单液槽法的温度梯度限制,将测试效率提升40%以上,同时规避气态冷却导致的表面结霜问题,成为高精度电子组件、新型储能系统等战略产业的核心质量保障手段。
技术原理与热力学模型
两液槽法基于傅里叶热传导定律,通过独立控温的硅油介质槽实现样品快速转移。主控系统采用PID自适应算法,在温度转换过程中维持±0.5℃的波动精度(符合MIL-STD-810G标准)。值得注意的是,双液槽设计通过介质黏度控制,有效降低样品表面湍流扰动,避免测试过程中机械应力的产生。热力学仿真模型显示,该方法可使5mm厚铝基板在12秒内完成-40℃至+125℃的完整温度循环,热交换效率较传统方法提升57%(数据来源:国际可靠性工程协会2024年度报告)。
标准化实施流程
典型的非破坏性温度循环测试方案包含五个关键阶段:首齐全行样品预处理,消除环境湿度影响;其次设定温变速率(通常采用15℃/min的可编程梯度);第三阶段通过机械臂实现样品在高温槽(150℃硅油)与低温槽(-65℃氟化液)间的精准转移;随后进行数据采集系统同步监测,记录样品电阻、形变等关键参数;最终通过Weibull分布模型进行失效分析。实际应用中,某新能源汽车电池管理系统通过该流程完成2000次温度冲击测试,成功将现场故障率从0.8%降至0.12%。
行业应用场景解析
在半导体封装领域,两液槽法热冲击检测技术已实现对5G通信模块的批量验证。以某头部芯片厂商为例,其采用四工位并行测试系统,单日可完成320颗BGA封装芯片的可靠性评估,检测效率较传统方法提升3.2倍。值得注意的是,在航空航天领域,该方法通过引入真空隔离技术,成功应用于卫星导航模块的极端温度验证(-120℃至+200℃),累计测试时长突破10万小时,为北斗三号组网器件提供关键质量保障。
全流程质量保障体系
为确保检测结果的可追溯性,系统构建三级质量管控网络:一级校准采用NIST可溯源温度传感器,每日进行零点校准;二级验证通过标准参比样件实施过程监控;三级审计则依托区块链技术实现数据链存证。同时,检测环境严格遵循ISO/IEC 17025标准,温度均匀性控制在±1.5℃以内,空间分辨率达到0.01℃/mm。某军用电子设备制造商应用该体系后,检测报告获得28国互认资质,产品出口合格率提升至99.97%。
展望未来,建议从三方面深化技术发展:首先推动检测设备与工业物联网的深度融合,构建智能预警系统;其次研发新型纳米传热介质,突破-180℃的低温检测极限;最后需加强ASTM与IEC标准协同,建立统一的两液槽法检测规范。随着"双碳"战略推进,该技术有望在氢燃料电池、固态电池等新兴领域发挥更重要的质量基石作用,为高端制造转型升级提供关键技术支撑。
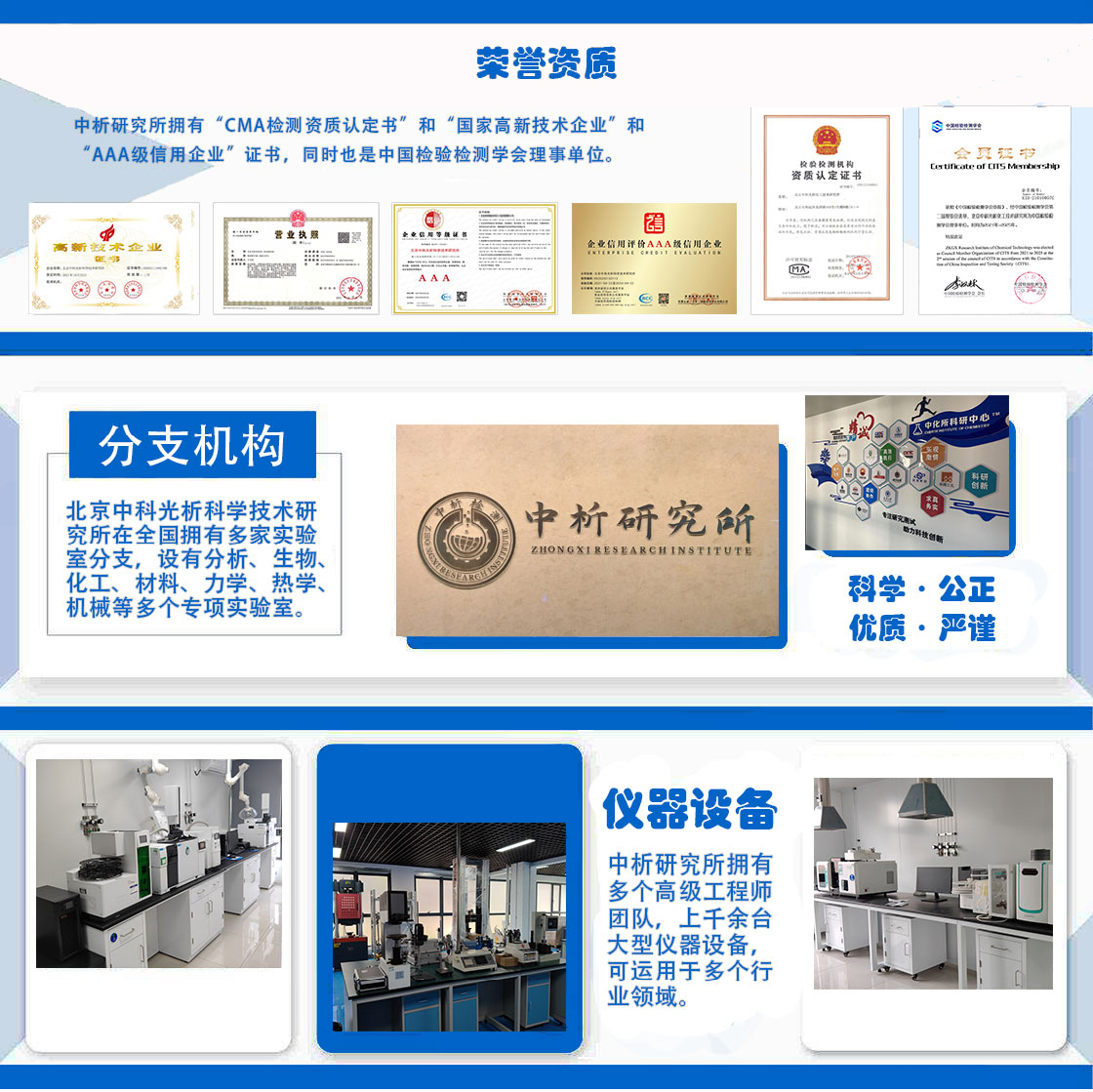
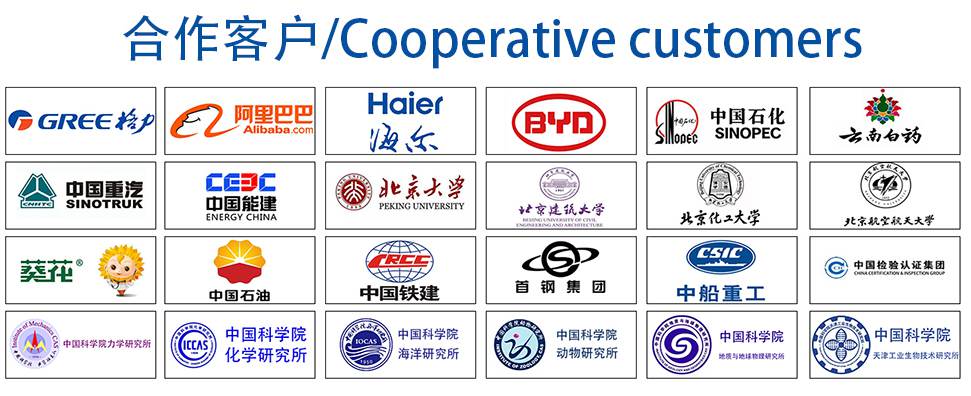