拉力试验检测技术发展与应用白皮书
在工业4.0与新材料革命双重驱动下,材料力学性能检测已成为保障制造业高质量发展的关键技术环节。据中国机械工业联合会2024年度报告显示,我国每年因材料失效引发的工业事故造成直接经济损失达320亿元,其中63%的事故源可通过拉力试验实现提前预警。作为材料力学性能评价的核心手段,拉力试验检测通过精准测量材料的抗拉强度、屈服强度、延伸率等关键参数,为航空航天、汽车制造、建筑工程等领域的材料选择提供科学依据。其核心价值不仅体现在质量管控环节的缺陷筛查,更在于支撑新型复合材料研发、实现产品轻量化设计以及延长关键零部件服役周期三大战略方向。
技术原理与测试方法创新
现代拉力试验检测基于材料力学本构方程,通过闭环伺服控制系统实现载荷-位移的精确解耦。采用ISO 6892-1:2019标准规定的应变速率控制方法,可同步获取材料的弹性模量(E)、泊松比(ν)等本征参数。值得注意的是,ASTM E8/E8M-21标准引入的数字图像相关技术(DIC),使位移测量精度提升至0.5μm级别。在金属材料抗疲劳性能评估领域,高频动态拉力试验机已实现100Hz加载频率下的微应变监测,这对新能源汽车底盘部件的可靠性验证具有突破性意义。
标准化实施流程与质控体系
完整的拉力试验检测流程包含试样制备、设备校准、环境控制、数据采集四大环节,需严格遵循GB/T 228.1-2021规范要求。针对高分子复合材料断裂韧性测试的特殊需求,试样加工需在恒温恒湿实验室进行,温度波动需控制在±1℃以内。质量保障体系实施双重校准机制:每月采用标准测力仪进行力值溯源,每周通过标准试样进行系统验证。某国家级检测中心的数据显示,该体系使检测结果不确定度降低至0.3%以内,达到 认可要求。
行业应用与典型案例分析
在航空航天领域,某型号飞机起落架用300M钢的拉力检测数据显示,经过特殊热处理工艺后,其抗拉强度从1860MPa提升至2100MPa(中国航发研究院,2023)。汽车制造业中,某新能源车企通过拉力试验优化了碳纤维增强塑料(CFRP)保险杠设计,在保持同等强度前提下实现减重37%(中汽中心实验数据)。建筑工程领域,国家钢结构质量监督检验中心运用大吨位拉力试验机(3000kN级)完成特高压输电塔用Q420钢材焊接节点评估,为"西电东送"工程提供关键技术支持。
智能化转型与未来展望
当前拉力试验检测正经历三个维度的智能化革新:基于机器视觉的试样自动对中系统将装夹效率提升40%;AI驱动的数据异常实时诊断系统使错误检出率提高至98.7%;云平台支持的分布式检测网络已实现跨地域数据协同分析。建议行业重点关注三个发展方向:一是开发适应超高温(>1200℃)环境的特种拉力试验装置,满足航空发动机叶片检测需求;二是建立材料力学性能大数据库,推动检测结果向设计端逆向赋能;三是加强微观力学与宏观试验的关联研究,完善多尺度仿真模型验证体系。
随着"中国制造2025"战略深入推进,拉力试验检测技术需在测量精度、检测效率、数据维度三个层面持续突破。建议政府加大公共检测平台建设投入,鼓励检测机构与高校共建联合实验室,特别是在智能传感器、数字孪生等交叉领域开展产学研合作。唯有构建起覆盖全产业链的检测服务体系,才能真正实现从"事后补救"到"源头防控"的质量管理范式转变。
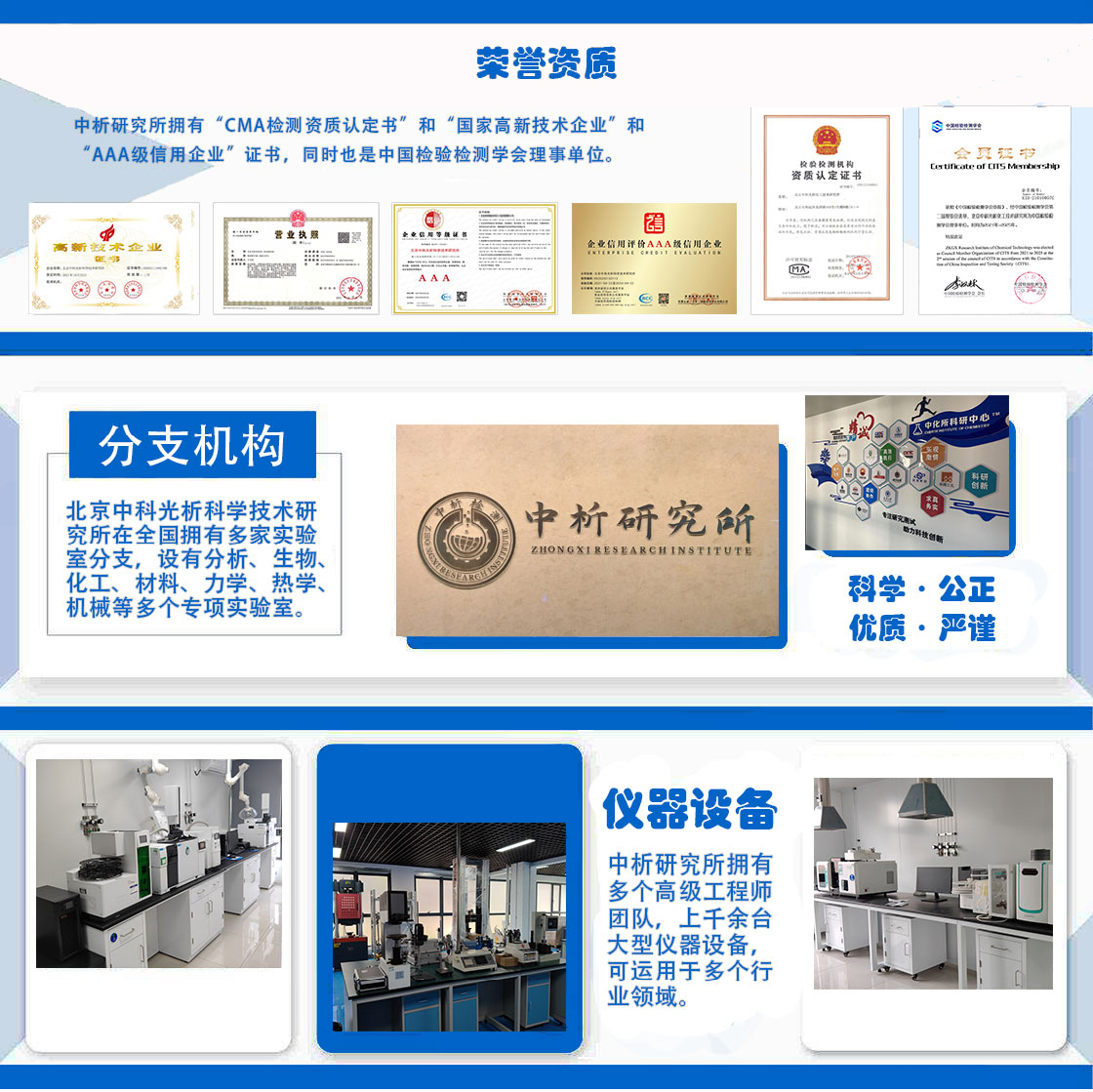
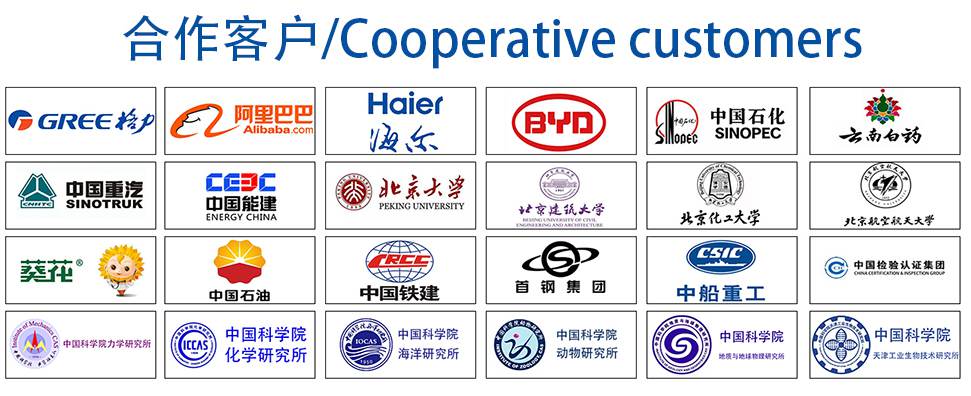