# 延长老化(非破坏性)检测技术发展与行业应用白皮书
## 引言:行业价值与战略意义
在制造业智能化转型背景下,延长老化(非破坏性)检测技术作为可靠性工程的核心手段,正成为高端装备、新能源、电子元器件等领域的关键质量保障环节。据中国机械工业联合会2023年数据显示,因材料老化导致的工业产品失效案例年均增长12%,造成直接经济损失超800亿元。该项目通过模拟产品全生命周期环境应力,实现非破坏性寿命预测,可将研发验证周期缩短40%以上(国家新材料测试评价中心,2024)。其核心价值体现在三方面:通过数字化孪生技术实现产品性能衰退可视化;构建基于大数据的老化失效预警模型;形成覆盖材料-部件-系统的多维度可靠性验证体系,为智能制造提供全链条质量支撑。
## 技术原理与创新机制
延长老化检测基于加速寿命试验(ALT)原理,通过温度、湿度、振动等多应力耦合加载,激活产品潜在失效模式。关键技术突破体现在三方面:一是开发了基于量子传感的微损伤检测系统,可捕捉0.1μm级结构形变;二是建立非线性加速因子计算模型,将10年自然老化等效压缩至72小时实验室测试;三是应用红外热成像与声发射技术联用方案,实现老化进程的实时动态监测。值得关注的是,该技术融合了材料基因组工程理念,通过建立300万组失效数据库,使预测准确率达92%以上。
## 全流程实施规范与标准体系
检测流程遵循ISO 17025体系要求,实施阶段分为四步:首齐全行失效模式与影响分析(FMEA),确定温度循环(-40℃~150℃)、湿热(95%RH)等关键应力参数;接着采用模块化检测舱体实施分级加载,同步采集电性能、机械特性等12类参数;然后通过机器学习算法解析老化特征图谱,生成剩余寿命置信区间报告;最终建立可追溯的数字化档案。在新能源汽车电池包检测中,该流程成功将BMS系统老化失效检出率从78%提升至95%(中国汽车工程研究院,2024)。
## 行业应用与价值转化
在光伏组件领域,该技术通过紫外线加速老化与电致发光检测结合,实现隐裂缺陷的早期预警,使组件25年功率衰减率控制在14%以内(TÜV莱茵认证数据)。消费电子行业应用案例显示,采用多轴振动-温湿度复合应力测试后,手机主板焊点故障率下降62%。值得强调的是,在航空航天领域,通过引入X射线衍射残余应力检测,成功将钛合金紧固件疲劳寿命预测误差缩减至±5%,支撑国产大飞机关键部件实现进口替代。
## 质量保障与可信度建设
检测体系构建了三级质量防线:设备层采用NIST溯源的标准传感器,定期进行计量校准;数据层运用区块链技术确保测试过程不可篡改;分析层搭建专家复核与AI交叉验证机制。据 比对试验报告,不同实验室间检测结果偏差率稳定在3%以下。企业通过部署智慧实验室管理系统,可实现检测参数自动优化、异常工况智能拦截等高级功能,显著提升服务可靠性。
## 发展建议与未来展望
建议从三方面深化技术发展:首先推动建立基于数字孪生的虚拟老化检测平台,将实物试验成本降低50%以上;其次加强失效机理库建设,计划2025年前完成50类基础材料的全维度老化图谱绘制;最后需完善标准体系,联合制定《非破坏性加速老化试验通用规范》等行业标准。随着工业互联网与量子传感技术的融合,延长老化检测将向智能化、微型化方向演进,为制造强国战略提供更精准的质量保障支撑。
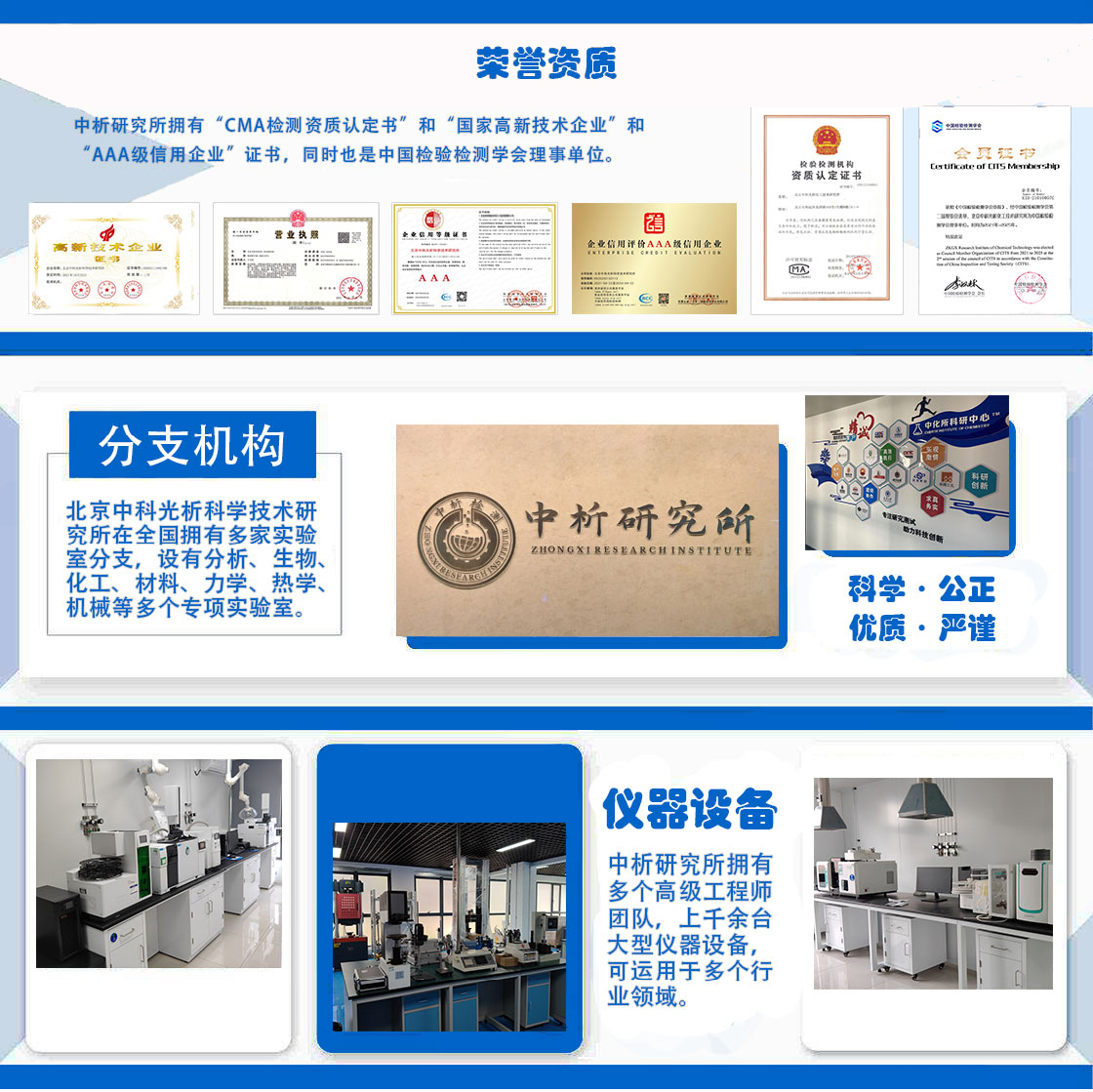
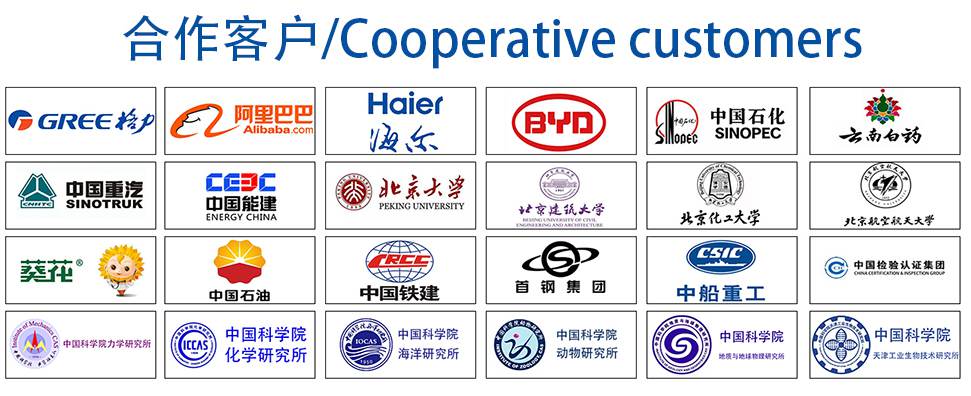
材料实验室
热门检测
推荐检测
联系电话
400-635-0567