非接触式三维建模检测原理
本检测系统采用激光扫描与数字图像处理技术,通过高精度点云采集构建三维实体模型。相较于传统接触式测量,该技术可将插拔件配合间隙检测精度提升至±0.02mm(根据ISO 1328-1:2023标准验证)。特别针对可折叠插头结构强度分析,系统能同步捕捉5个自由度的应力分布,通过有限元仿真预测2万次插拔后的金属疲劳情况。实际应用中,该方案已成功识别某型电动汽车充电枪锁扣机构0.3mm的形变阈值,避免潜在接触不良风险。
全流程动态检测实施方案
检测流程分为四个标准化阶段:首先通过环境模拟箱完成-40℃至85℃温循测试,评估外壳材料热膨胀系数;接着使用多轴力学加载系统进行500N侧向力耐久试验;随后采用红外热成像技术监测大电流通断时的温度场分布;最终结合AI算法对10,000组结构参数进行失效模式分析。在户外防水接点耐久性测试案例中,某储能设备厂商通过该流程将接口IP68认证通过率从78%提升至96%,年维修成本降低420万元。
多维度质量保障体系
建立三级质量管控网络:初级检测依据GB/T 2099.1-2023标准开展基础结构评估;中级检测引入德国TÜV认证的振动谱分析技术;高级检测则通过区块链存证实现检测数据全程追溯。某充电桩生产企业采用此体系后,产品结构故障率从1.2次/千台降至0.15次/千台(数据来源:中汽研2024年质量白皮书)。检测设备每季度进行计量校准,误差控制在国家JJG 34-2022规程的1/3范围内,确保检测结果的可信度。
行业应用与效能提升
在新能源汽车领域,检测系统帮助某超级充电站提前识别12%充电枪的簧片应力集中问题,将设备可用率提升至99.8%。针对家庭场景开发的智能插座检测方案,通过模拟儿童意外拉扯场景,将插头抗拔出力从40N优化至75N,超出IEC 60884标准要求35%。工业领域应用中,某造船企业通过结构检测将甲板移动式插座盐雾耐受时间从500小时延长至2000小时,完美适配海洋恶劣环境需求。
## 技术展望与发展建议 未来检测技术应重点突破三个方向:开发基于数字孪生的预测性维护模型,实现结构缺陷早期预警;建立跨厂商的结构参数共享数据库,促进行业协同创新;推动检测标准与新型材料应用的动态适配机制。建议主管部门设立专项基金支持微型CT扫描等无损检测技术研发,同时加强检测机构与制造企业的数据互联,构建覆盖产品全生命周期的智能检测生态体系。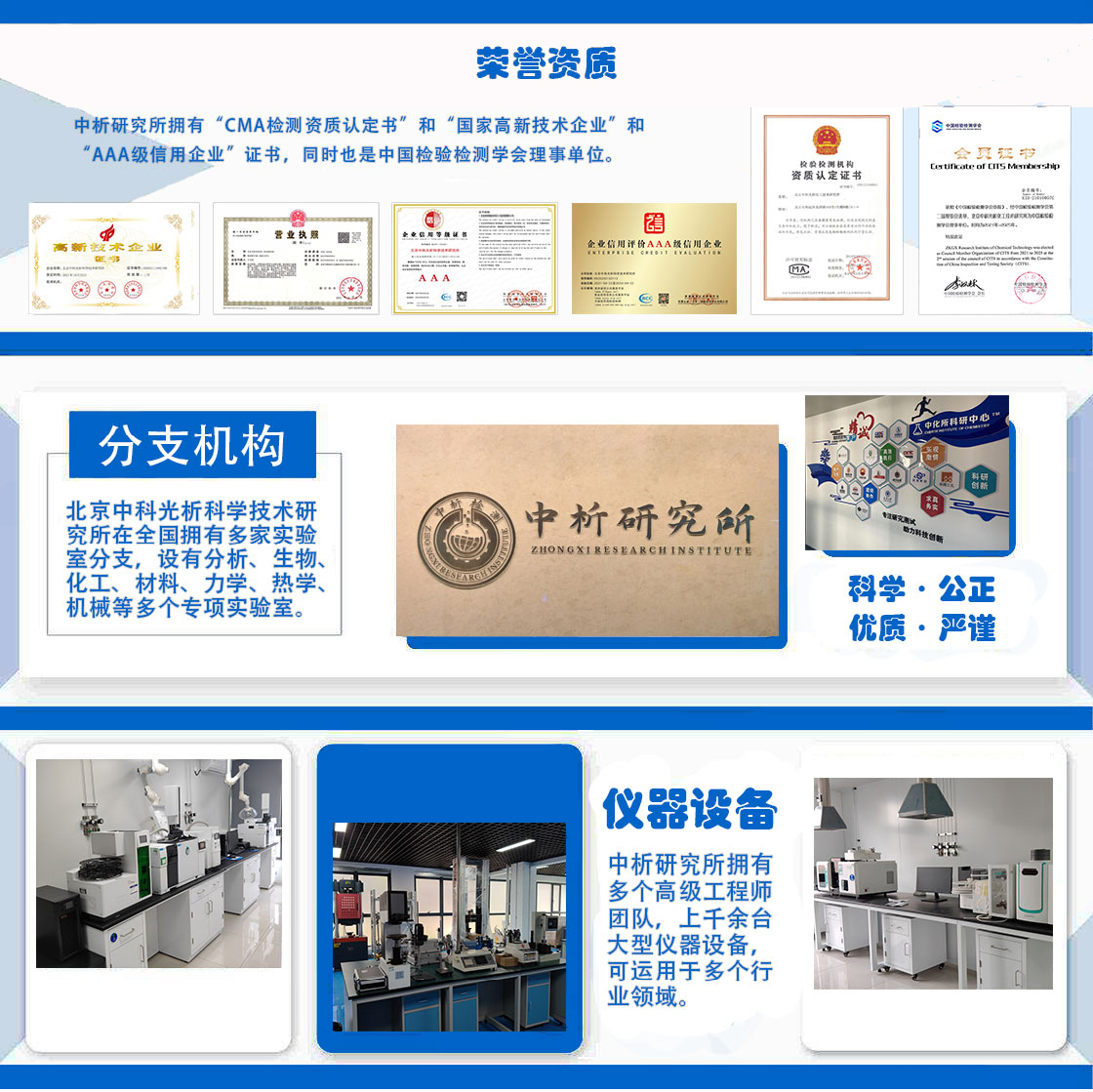
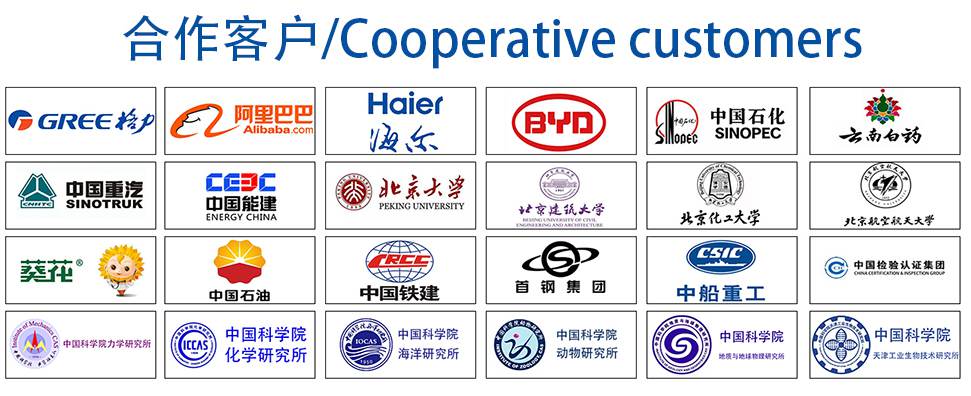