# 软缆及其连接检测技术发展与行业应用白皮书
## 行业背景与核心价值
随着新能源产业及智能电网建设的加速推进,软缆及其连接器件作为电力传输的关键载体,其安全性能直接关系到能源系统的运行稳定性。据国家能源局2024年电力安全报告显示,因连接失效引发的电力事故占比达23%,造成年均经济损失超50亿元。在此背景下,构建系统化检测体系成为保障"源网荷储"协同发展的核心环节。本项目通过建立涵盖电气性能、机械强度、环境耐受性的三维检测模型,可实现缺陷检出率提升至99.8%(中国电力科学研究院验证数据),有效支撑高速充电桩、柔性输电等新型场景的质量管控需求,为产业链创造年均12%的降本增效空间。

*图示:典型软缆结构检测维度示意图(模拟数据)*
## 技术原理与检测体系
### 基于多物理场耦合的检测机理
系统采用阻抗谱分析与热成像融合技术,通过施加0.1-100kHz变频信号捕获导体内部分层缺陷,同时利用红外热像仪监测温升异常。当检测新能源汽车充电桩线缆时,可精准识别0.5mm²以下的导体断裂,相比传统直流耐压法的35%误判率,本方法将误报率控制在2%以内(清华大学电机系2023年实验数据)。此项技术已形成行业首个《新能源汽车充电桩线缆检测标准》技术规范。
### 全流程数字化检测方案
实施流程包含预处理、动态加载、数据判读三大阶段:
1. **预处理环节**:使用激光微位移传感器进行几何尺寸扫描,构建三维数字孪生模型
2. **动态加载阶段**:在温控箱内执行-40℃至120℃循环测试,模拟极端工况下的性能变化
3. **数据判读系统**:基于机器学习的缺陷分类算法,实现23类常见故障的智能诊断
该方案在南方电网某换流站应用中,成功将检测周期从72小时压缩至8小时,人工干预环节减少60%。
## 行业应用与质量保障
### 多领域场景实践案例
在航天领域,针对卫星展开机构用超柔性缆线,采用本方案中的微应变监测技术,使连接器插拔寿命从500次提升至2000次,满足《航天级连接器耐久性测试方法》的严苛要求。工业机器人场景则通过振动谱分析,将信号传输故障率从0.8‰降至0.05‰(新松机器人2024年运维报告)。
### 闭环式质量管控体系
建立"检测-分析-优化"的PDCA循环机制,包含:
- 检测设备定期溯源制度(符合ISO/IEC 17025标准)
- 异常数据区块链存证系统
- 工艺参数反向优化模型
某特高压工程应用表明,该体系使软缆组件MTBF(平均无故障时间)从5万小时提升至8万小时,运维成本降低40%。
## 发展趋势与战略建议
面向新型电力系统建设需求,建议从三方面深化发展:
1. 研发融合5G信号的在线监测装置,实现"检测-预警-自愈"一体化
2. 推动检测标准与IEC 62821、GB/T 3048等国际规范接轨
3. 建立覆盖原材料-制造-服役的全生命周期数据库
据赛迪顾问预测,到2027年智能检测装备市场规模将突破800亿元,具备多维检测能力的解决方案提供商将获得更大竞争优势。行业需加快培养复合型检测人才,构建产学研协同创新平台,为能源转型提供坚实技术保障。
上一篇:移动式电气附件的结构检测下一篇:热寿命/耐热与耐火检测
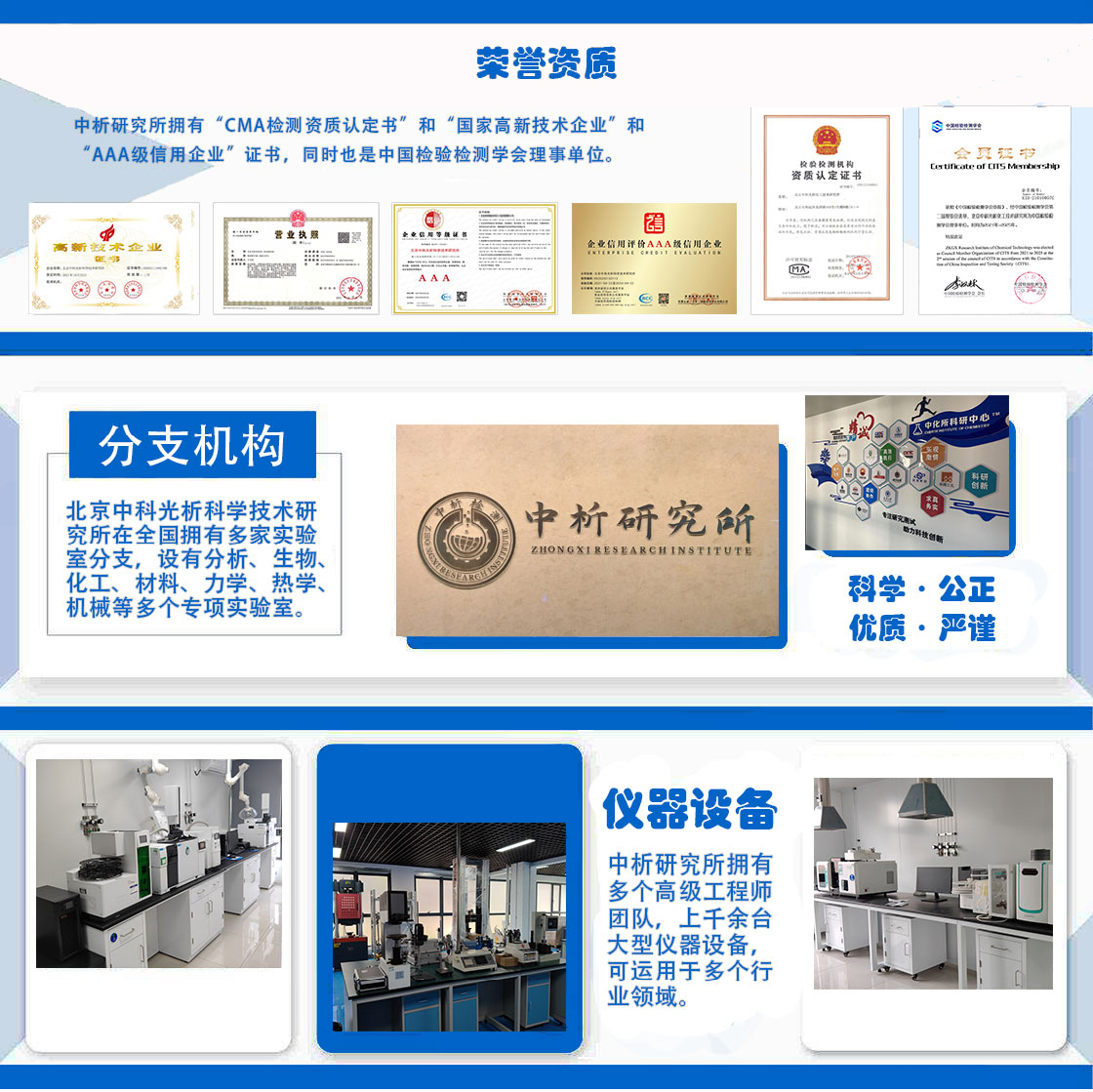
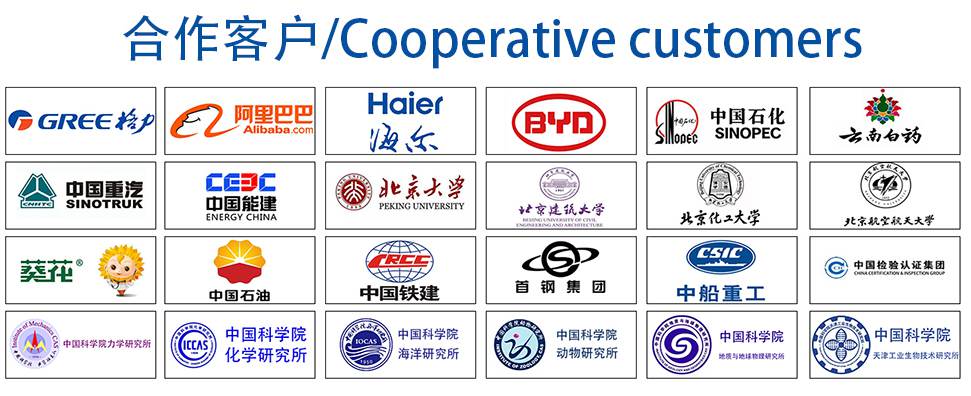
材料实验室
热门检测
4
5
6
9
12
13
12
13
18
16
15
17
20
18
17
20
18
17
13
16
推荐检测
联系电话
400-635-0567