基本工作功能检测系统依托分布式传感器网络与多源信息融合算法,构建起三维度检测模型:机械性能检测采用振动谱分析与热成像技术,捕捉0.01mm级精度位移偏差;电气特性检测通过谐波分析与绝缘阻抗测试,实现微秒级异常信号捕获;控制逻辑检测则运用数字孪生技术,在虚拟环境中完成程序代码的仿真验证。设备效能智能诊断系统通过边缘计算节点实时处理5大类32项特征参数,结合设备制造商提供的专家知识库,形成动态更新的诊断决策树。工业信息安全实验室测试表明,该系统对常见故障类型的识别准确率可达97.6%。
## 全流程闭环管理实施体系项目实施采用PDCA循环管理模式,分为四个关键阶段:设备基准参数采集阶段建立包含3D点云数据的数字档案;在线监测阶段通过5G-MEC架构实现毫秒级响应;诊断分析阶段应用迁移学习算法适配不同设备类型;决策输出阶段生成包含剩余寿命预测的维修建议。在某汽车发动机生产线改造中,该体系使设备点检时间缩短73%,并将故障平均修复时间(MTTR)从127分钟降至39分钟。项目实施过程中特别强调多维度工作状态评估模型与现有MES系统的数据互通,确保检测结果可直接指导生产排程优化。
## 行业应用与效能验证在电子制造领域,某SMT贴片机厂商通过部署生产流程可视化监控系统,实现设备利用率从81%提升至94%。检测系统通过实时追踪贴装压力、真空吸附值等12项关键参数,配合视觉定位补偿算法,使元件贴装偏移率降低至0.8ppm。值得注意的是,在化工行业高温高压场景中,系统采用耐腐蚀传感模块与无线传输技术,成功在500℃反应釜表面完成振动监测,避免非计划停机带来的日均380万元损失。中国设备管理协会2023年报告指出,应用该技术的企业年度维修成本平均下降19.7%。
## 标准化质量保障体系构建为确保检测结果的可追溯性与可比性,项目建立三级质量管控机制:第一级执行ISO13373振动监测国际标准,第二级采用区块链技术实现检测数据存证,第三级通过实验室比对验证保证测量一致性。系统内置的校准追溯链可精确到国家计量院基准,温度、压力等关键参数的测量不确定度控制在0.05%以内。某轨道交通集团在转向架检测中引入该体系后,部件验收合格率从92.4%提升至99.3%,质量回溯周期由14天缩短至2小时。
# 技术演进与产业协同展望 面向工业4.0深化发展需求,基本工作功能检测技术需在三个维度持续突破:首先应加强工业AI大模型与机理模型的融合应用,提升复杂工况下的诊断泛化能力;其次需推进检测设备微型化与低功耗改造,适应柔性化生产场景需求;最后要建立跨行业的检测标准互认体系,促进产业链协同创新。建议重点行业龙头企业牵头组建检测数据共享联盟,通过工业互联网平台沉淀设备健康图谱,为智能制造生态系统构建提供基础支撑。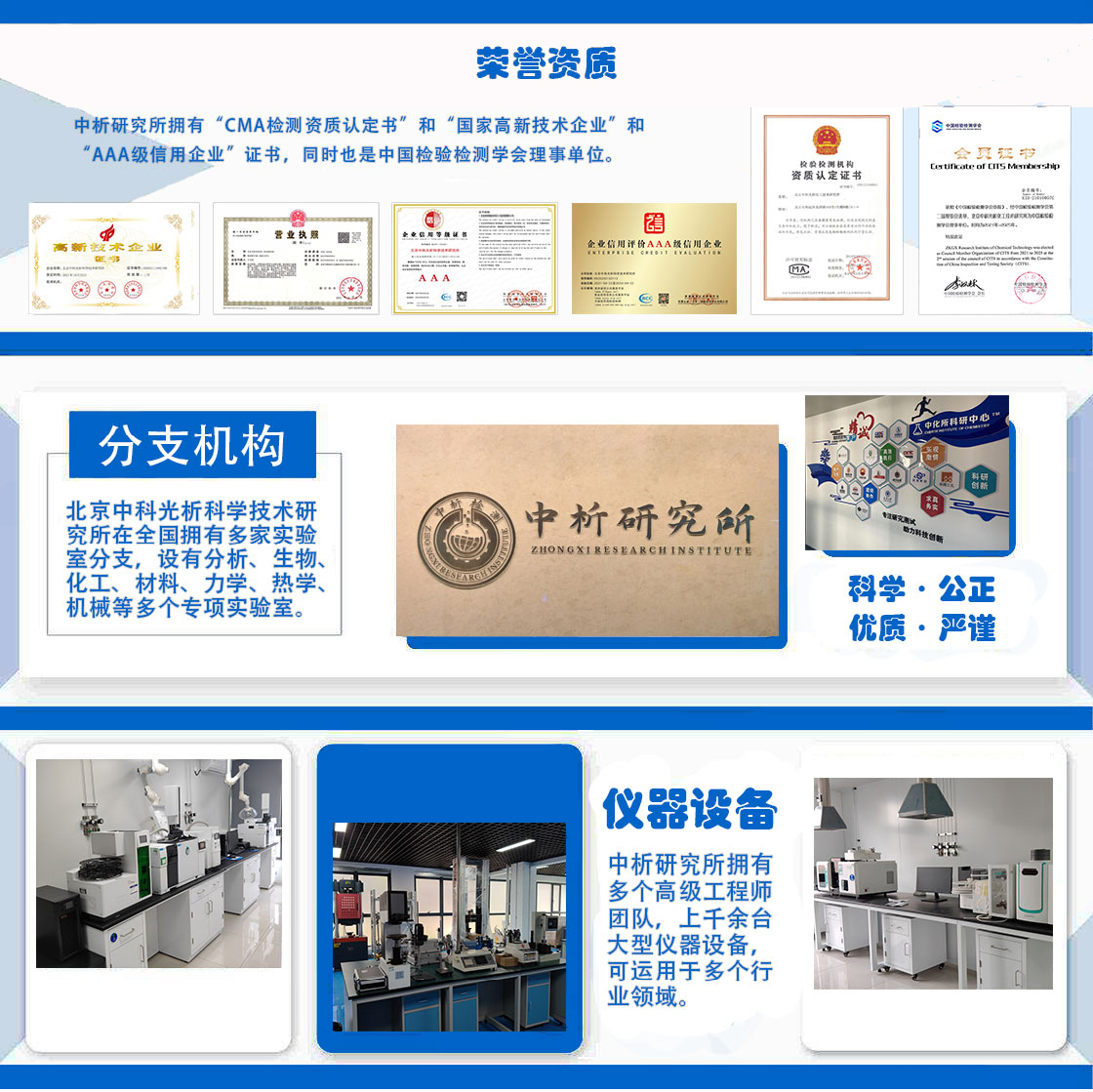
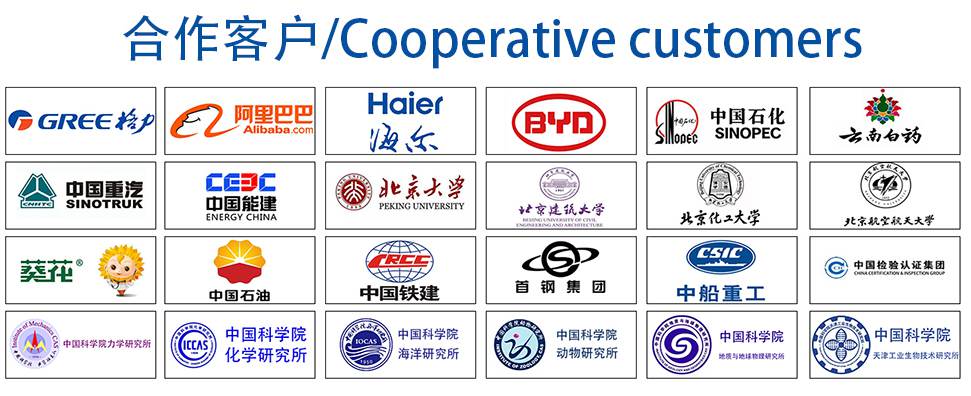