绝缘电阻和介电强度检测技术白皮书
随着新能源装备、高压输变电设备及智能电网的快速发展,电气设备绝缘性能已成为影响系统安全的核心指标。据国家能源局2024年行业安全报告显示,由绝缘失效引发的电力事故占总故障量的37%,直接经济损失超80亿元/年。在此背景下,绝缘电阻与介电强度检测项目通过量化评估材料耐受电压能力,构建起电气设备全生命周期安全防线。该检测体系不仅可预防击穿、漏电等潜在风险,更在新能源电池包、超高压电缆等新兴领域形成关键质量认证依据,其核心价值在于将传统定性判断升级为基于国际IEC标准的定量化评估,为制造端工艺优化和运维端预防性检修提供数据支撑。
技术原理与测试方法论
绝缘电阻检测基于直流高压法,通过施加500-5000V测试电压,测量绝缘介质在极化效应下的泄漏电流,计算得出兆欧级电阻值。介电强度检测则采用交流耐压法,以梯度升压方式直至介质击穿,记录击穿电压与时间曲线。根据中国电力科学研究院2023版检测规程,双重测试需在环境温湿度(23±2℃, 45-75%RH)受控条件下进行,通过补偿算法消除表面泄漏电流干扰。特别在新能源汽车动力电池包检测中,需同步采集极化指数(PI值)和介质损耗角正切值(tanδ),构建多维绝缘评估矩阵。
全流程标准化实施方案
典型检测流程分为预处理、基准测试、应力试验三阶段。预处理需对被测物进行72小时恒温除湿,消除环境历史效应。基准测试阶段采用Megger MIT515绝缘测试仪,按IEC60243标准执行阶梯升压:首先施加1kV电压保持60秒,记录稳态电阻值;继而以每秒2kV速率升至额定电压的1.5倍,监测微电流变化。在第三代半导体器件检测中,引入局部放电(PD)同步监测技术,当检测到>5pC放电量时立即触发保护机制。全过程数据通过LabVIEW系统进行趋势分析,生成包含极化吸收比(DAR)等12项参数的检测报告。
行业应用场景与实证案例
在南方电网2023年变压器年检中,基于绝缘电阻图谱分析提前3个月预警某500kV变压器匝间绝缘劣化,避免潜在停电损失2400万元。新能源汽车领域,某头部电池厂商通过建立介电强度-温度关联模型,将电池模组绝缘故障率从0.8%降至0.12%。值得关注的是,在海上风电领域应用时需采用特殊修正系数:据DNV GL海洋工程规范,潮湿盐雾环境下检测阈值应提高30%,并通过施加极性反转电压验证材料稳定性。这些实践验证了差异化场景下的技术适配能力。
质量保障与认证体系
检测实验室需构建三级质控体系:初级校验采用标准电阻箱日检制度,中级通过 认可的标准样品进行季度比对,高级则参与IECEE-CB体系国际循环测试。关键设备如高压发生器须执行ASTM D149标准的年检程序,确保输出电压误差<±1.5%。人员资质方面要求检测工程师持有NETA电气测试认证,并每两年完成IEEE 400.2标准更新培训。某特高压设备制造商通过该体系将检测结果离散度从8.7%压缩至2.3%,显著提升产品出口合规性。
展望未来,建议行业重点发展两项能力:一是研发集成化智能检测设备,融合阻抗谱分析与局部放电定位技术,实现绝缘缺陷的亚毫米级空间分辨率;二是构建基于数字孪生的预测性维护平台,将历史检测数据与设备运行工况关联建模。据清华大学能源互联网研究院预测,到2028年智能化绝缘检测市场规模将突破52亿元,推动检测效率提升40%以上。同时需加快制定柔性电子器件、固态电池等新兴领域的专用检测标准,形成覆盖全电压等级、全应用场景的电气设备绝缘性能评估体系。
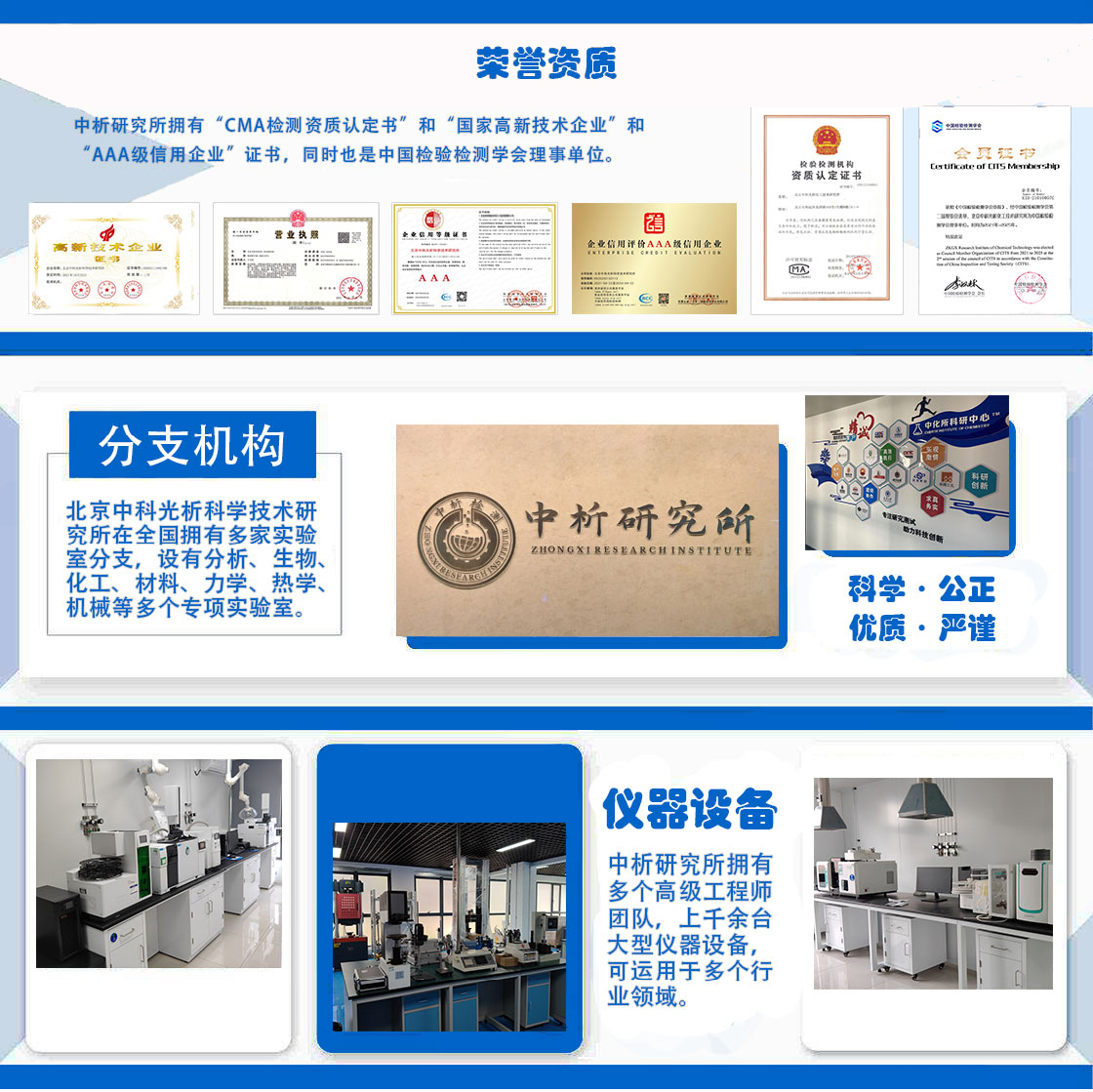
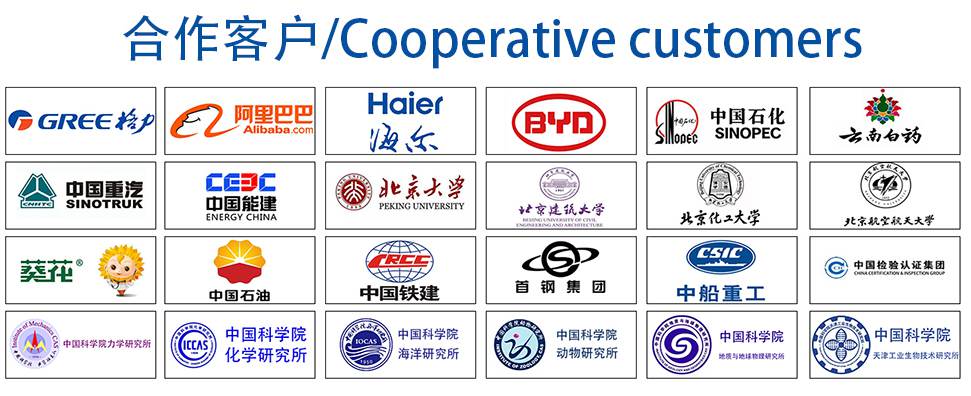