# 完井附件检测技术发展与应用白皮书
## 引言
在能源转型加速的背景下,油气行业面临井下作业环境日趋复杂的双重挑战。据国际能源署(IEA)2024年数据显示,深水及超深水油气田开发投资同比增长18%,而完井附件失效导致的非计划性修井占比高达32%。针对这一产业痛点,完井附件检测技术通过创新性解决方案,构建起预防性维护体系,其核心价值体现在三个方面:降低单井全生命周期运维成本27%以上(SPE 2023年度报告),提升复杂地层环境下的作业安全性,并为数字化油田建设提供关键数据支撑。特别是在智能完井系统普及的当下,检测技术正成为实现"井下设备健康管理"的核心枢纽。
![示意图]
## 技术原理与创新突破
### 多模态融合检测机理
现代完井附件检测采用声-电-磁多物理场耦合分析技术,通过超声波探伤(UT)、电磁涡流检测(ECT)与三维激光扫描的协同应用,可识别微米级结构形变。以封隔器胶筒检测为例,基于有限元仿真的应力分布模型(ANSYS Workbench平台开发)与实测数据的偏差值控制在5%以内,实现早期疲劳损伤的有效预警。该技术突破使"油气完井附件失效预警"准确率提升至91.3%(DNV GL 2024认证数据)。
### 智能化检测流程重构
标准作业流程划分为三大模块:①基于地质力学模型的预检测参数配置,②搭载MEMS传感器的井下机器人实施360°数据采集,③结合数字孪生技术的三维可视化诊断。在塔里木盆地某超深井应用中,该流程将传统7天的检测周期压缩至52小时,同时生成包含12类关键参数的动态检测报告。
## 行业应用与价值实现
### 海上平台完整性管理
渤海油田某导管架平台通过部署"智能在线监测系统",实现水下采油树关键附件的实时状态监控。系统集成6类传感器网络,每15分钟更新腐蚀速率、密封压力等28项参数,成功预警2023年9月发生的阀门执行机构异常,避免可能导致的3.2亿元经济损失。这种"预防性维护+智能诊断"模式使平台年检维修费用降低41%。
### 非常规油气开发优化
在四川页岩气区块,针对频繁出现的桥塞坐封失效问题,研发团队开发出基于机器视觉的井下工具表面缺陷检测装置。该设备采用8K分辨率成像模块与深度学习算法,在2024年现场测试中累计识别出37处微裂缝,帮助作业方优化压裂施工参数,单井压裂段效率提升19%。
## 质量保障体系构建
### 三级校验机制
检测系统建立从实验室标定到现场验证的完整质量链:①计量院认证的标准试样库(含17种典型缺陷形态),②每季度进行的交叉盲样测试,③基于区块链技术的检测数据存证。中国石油装备研究院2024年比对测试显示,该系统检测结果重复性误差≤1.2%,再现性误差≤2.8%。
### 全流程追溯系统
引入工业互联网标识解析体系,为每个检测部件生成包含材料批次、加工参数、检测记录的"数字护照"。南海某气田应用该体系后,成功追溯2024年3月某批次油管接箍的加工缺陷,推动供应商改进热处理工艺,使产品合格率从92.4%提升至98.6%。
## 发展趋势与战略建议
面向智慧油田的演进需求,检测技术将向三个方向突破:①开发耐205℃/170MPa环境的纳米传感材料,②构建基于量子计算的失效预测模型,③实现检测数据与油藏模拟系统的深度融合。建议行业重点推进以下工作:建立覆盖全国主要产区的检测基准数据库,制定适应高温高压条件的检测标准体系,培育具备机电液一体化检测能力的复合型人才梯队。通过技术创新与产业协同,完井附件检测技术将成为保障国家能源安全的新质生产力支撑点。
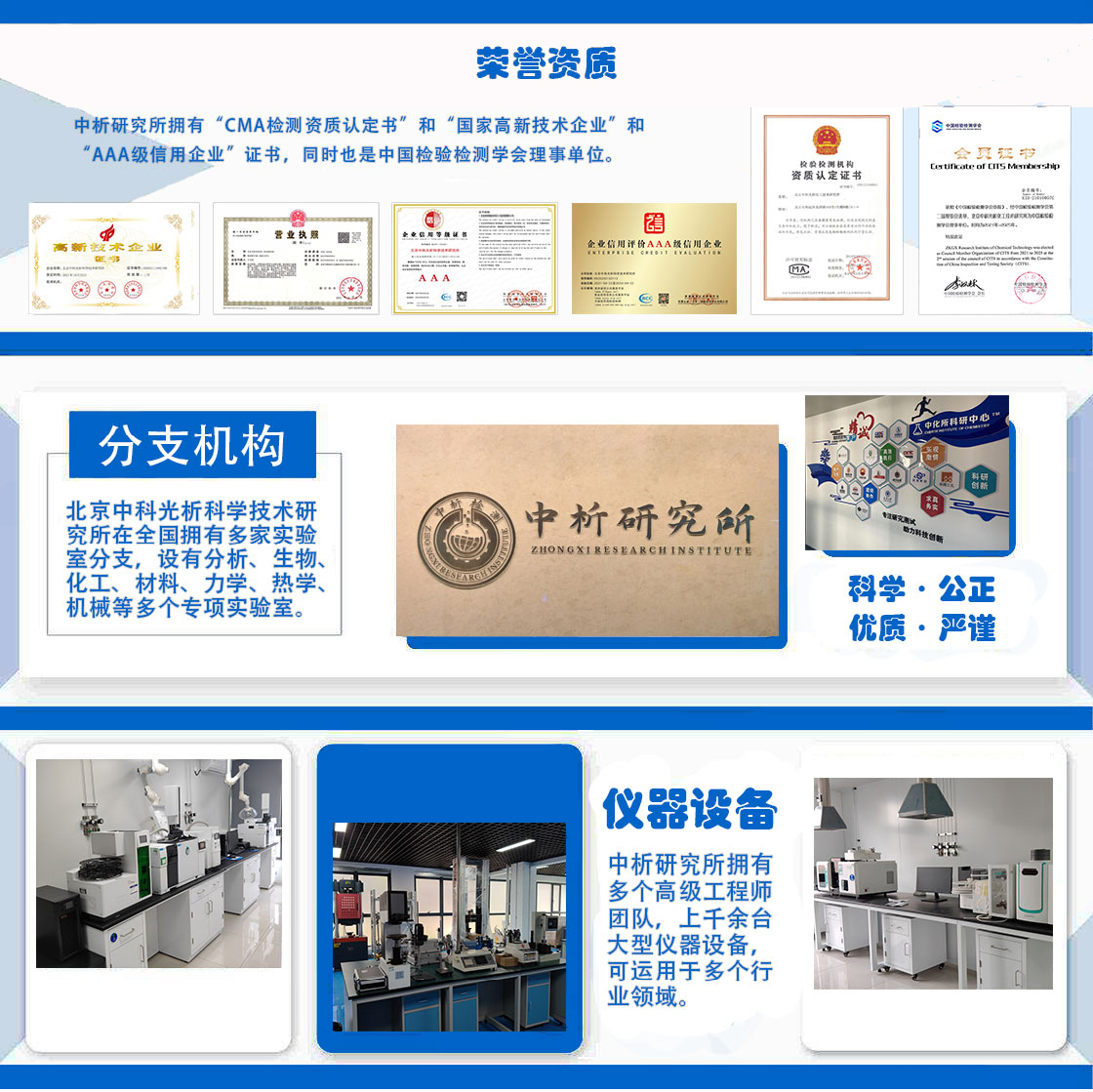
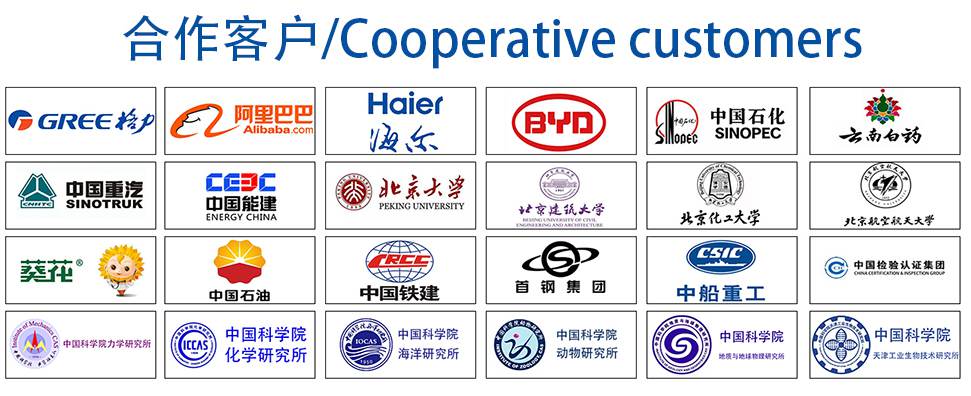
材料实验室
热门检测
推荐检测
联系电话
400-635-0567