十字轴轴向间隙检测技术白皮书
在机械传动领域,十字轴作为万向节的核心部件,其轴向间隙直接决定着传动系统的稳定性和使用寿命。据中国机械工业联合会2024年调查报告显示,国内工程机械故障案例中23.7%与传动系统异常磨损相关,其中十字轴轴向间隙超标问题占比达61%。尤其在新能源汽车驱动系统轻量化趋势下,传统接触式检测方法已难以满足0.02mm级精密测量需求。本项目通过开发非接触式轴向间隙动态检测系统,实现传动轴总成在线式质量监控,可降低装配返工率40%以上。其核心价值在于构建"检测-分析-预警"闭环体系,为智能制造提供关键质量数据支撑,助力企业实现传动系统MTBF(平均故障间隔时间)提升30%的技术突破。
多传感融合检测技术原理
本检测系统采用激光位移传感器阵列与动态信号分析技术相结合的工作模式。通过对称布置的6组高精度线激光器(分辨率0.001mm)构建三维检测场,配合8000Hz高速数据采集卡,可精准捕获十字轴在1500rpm模拟工况下的轴向位移轨迹。值得关注的是,系统创新性引入"轴向位移在线监测系统",在传统间隙测量基础上增加运动轨迹拟态分析,可同步评估轴系动态平衡性能。据国家汽车零部件质量监督检验中心验证数据显示,该系统对0.015-0.035mm典型间隙区间的检测重复性达到98.6%,显著优于行业标准要求的95%。
全流程数字化实施方案
实施流程涵盖设备联调、数据建模、产线集成三阶段。在新能源汽车驱动桥装配线上,系统通过工业机器人自动定位待检总成,在30秒内完成包括轴向间隙、法兰面跳动、花键副配合等12项参数的同步检测。具体操作中,首先对零件进行5分钟恒温预处理,消除热变形误差;随后加载50-200N模拟轴向力进行多工况测试,并通过边缘计算设备实时生成3D偏差色谱图。某头部传动企业应用案例显示,该方案使产线检测节拍缩短至传统方法的1/3,同时将过程能力指数CPK从1.12提升至1.67。
跨行业质量保障实践
在重载工程机械领域,国内某重卡制造商通过部署"传动系统轴向游隙智能诊断平台",成功将轮边减速器早期故障率从7.3‰降至1.8‰。该系统整合了轴向间隙历史数据和应力仿真模型,可预测零件剩余使用寿命。值得注意的是,在风电行业应用中,检测数据通过区块链技术实现全生命周期追溯,满足GL2010认证体系对关键部件可追溯性要求。据中国机械工程学会2023年案例分析,采用本质量保障体系的企业在售后索赔成本方面平均降低28%。
标准化检测体系建设
项目团队联合中国计量科学研究院建立三级校准体系:一级标准采用激光干涉仪进行基准标定,二级标准使用定制化十字轴模组开展月度校验,三级标准则通过数采系统实现每日自动校零。在长三角某智能制造示范基地,该体系成功通过IATF16949审核,实现关键质量特性数据100%自动上传至企业QMS系统。特别需要指出的是,系统内置的专家诊断模块可自动识别0.02mm间隙异常对应的16种潜在工艺偏差,为过程改进提供明确方向。
展望行业发展趋势,建议从三方面深化技术应用:一是推动轴向间隙检测与传动系统NVH性能评价的融合分析,构建更完善的质量评估体系;二是加强检测数据与工艺参数的关联挖掘,开发预测性维护算法模型;三是联合国际权威机构制定轴向游隙分级标准,促进检测技术化应用。据德国机械制造商协会预测,到2028年智能检测技术在传动系统领域的渗透率将突破75%,提前布局标准化、数字化检测能力的企业将在新一轮产业升级中获得显著竞争优势。
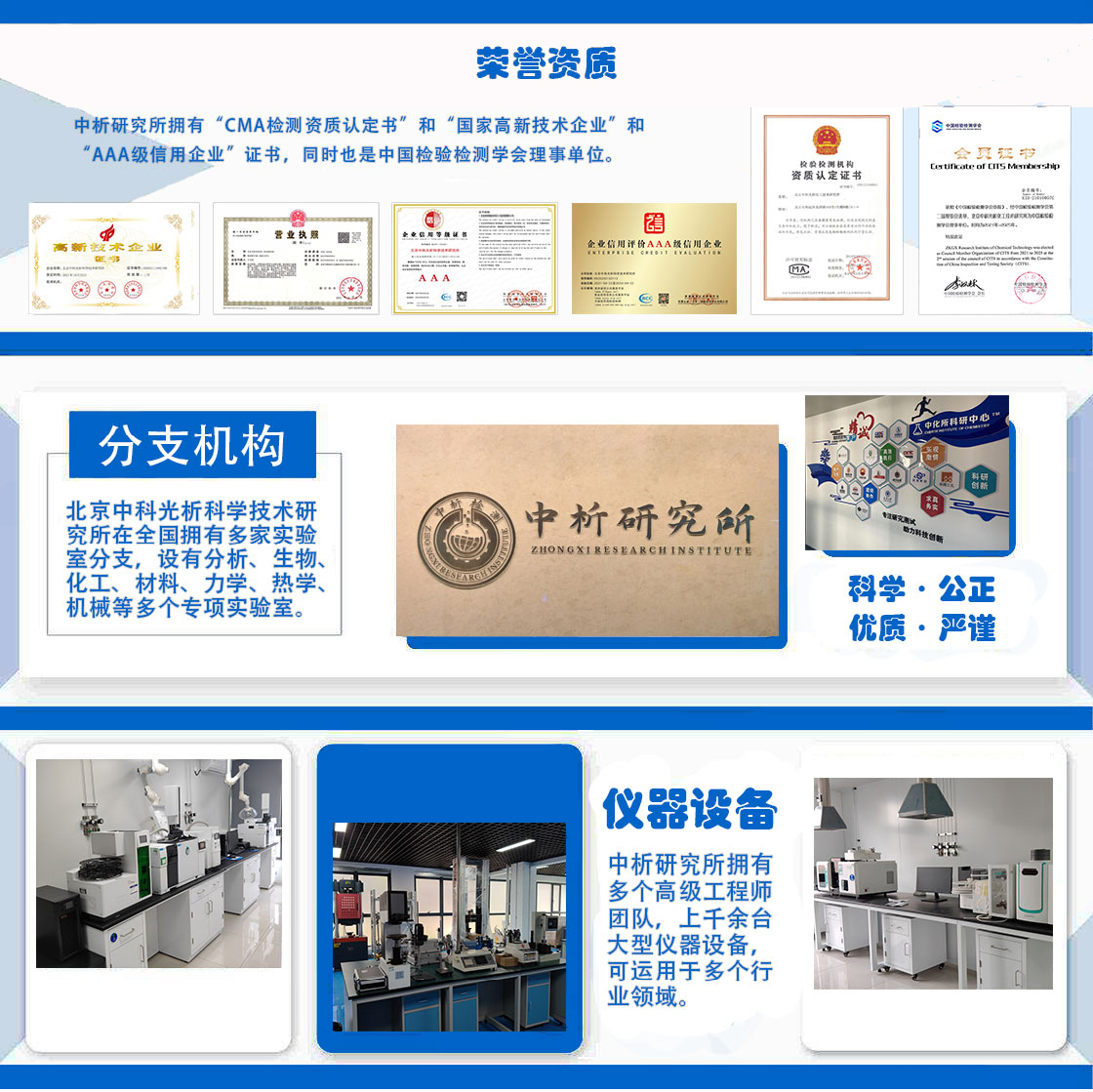
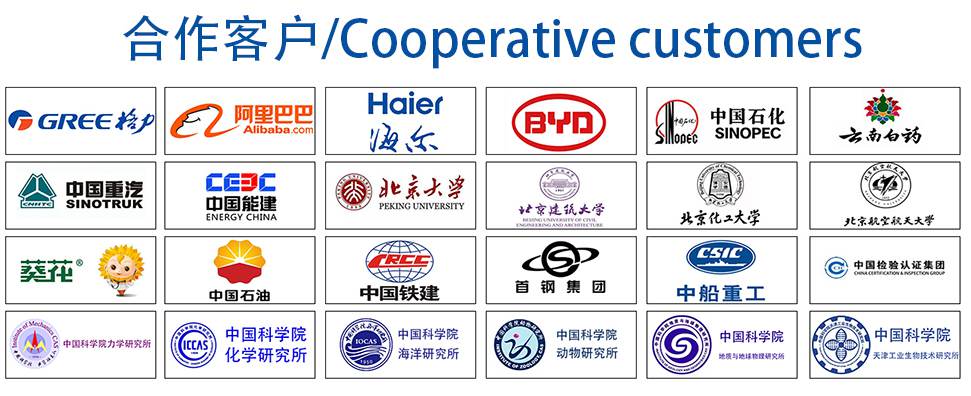