# 集电极-基极击穿电压检测技术白皮书
## 行业背景与核心价值
当前半导体产业正经历智能化与高性能化转型,功率器件市场规模预计2025年突破300亿美元(据Yole Development 2023年预测)。在此背景下,集电极-基极击穿电压(BV_CBO)检测作为功率晶体管可靠性评估的核心指标,直接影响新能源汽车、工业变频器等关键领域的设备稳定性。项目通过精准测量器件在高反压下的失效阈值,可显著降低电力电子系统因绝缘失效导致的故障率。核心价值体现在三方面:提升器件设计裕度、延长功率模块使用寿命约30%(基于SEMI 2024年行业报告),以及通过失效模式分析优化制造工艺,减少质量成本约18%。
## 技术原理与测量机制
### 检测项目的技术原理
BV_CBO表征双极型晶体管在基极开路时集电结承受的最大反向电压能力,其本质是评估PN结雪崩击穿特性。测试采用阶梯加压法,以0.1V/μs的速率施加反向偏置电压,同步监测泄漏电流变化。当电流突变超过设定阈值(通常为1mA)时,系统自动记录击穿电压值。需特别关注温度补偿机制,通过集成TEC温控模块将测试环境稳定在25±0.5℃,消除热载流子效应对测量精度的影响。该技术可同步完成“功率器件耐压性能评估”与“反向偏置安全裕度测试”两项关键长尾指标分析。
### 标准化实施流程
项目实施遵循IEC 60747-9国际标准,具体流程分为四个阶段:首先对晶圆进行去应力退火处理(350℃/2h),消除封装残余应力;随后使用探针台完成接触阻抗校准,确保测试回路阻抗<0.1Ω;在自动化测试系统中加载JEDEC标准波形,实现0-3000V全量程覆盖;最终通过SPC统计过程控制系统生成过程能力指数CPK报告。以某电动汽车逆变器模块检测为例,单批次1200颗IGBT器件的检测周期压缩至4小时,较传统方法效率提升2.3倍。
### 行业应用实证分析
在新能源领域,某头部厂商采用本技术对其车载充电模块进行“高反压工况可靠性验证”,成功将早期失效比例从1.2%降至0.15%。检测数据表明,当BV_CBO值>1800V时,模块在85℃/85%RH环境下的MTBF(平均无故障时间)可达12万小时(据Yole 2024年车载电子报告)。另在光伏逆变器场景中,通过建立BV_CBO与漏电流的回归模型,精准预测了组串式逆变器的寿命衰减曲线,使维护成本降低22%。
### 全生命周期质量保障
构建三级质量保障体系:第一级在芯片设计阶段采用TCAD仿真预验证,使设计迭代周期缩短40%;第二级导入在线光学检测(AOI)系统,实现微裂纹等缺陷的0.1μm级识别;第三级运用大数据分析技术,对历史检测数据进行AI建模,预警工艺偏移风险。某IDM企业应用该体系后,其碳化硅功率器件的批次一致性σ值从1.8优化至0.9,达到车规级AEC-Q101标准要求。
## 技术展望与发展建议
未来需重点突破三项技术瓶颈:其一,开发基于太赫兹波的“非接触式击穿电压检测”技术,解决传统探针接触带来的损伤问题;其二,建立极端工况(-55℃至200℃)下的动态测试标准;其三,推动检测设备与MES系统的深度集成,实现质量数据实时闭环。建议行业联盟牵头制定《宽禁带半导体耐压检测技术规范》,同时加强产学研合作,将机器学习算法应用于失效模式库建设,为第三代半导体器件的可靠性提升提供新范式。
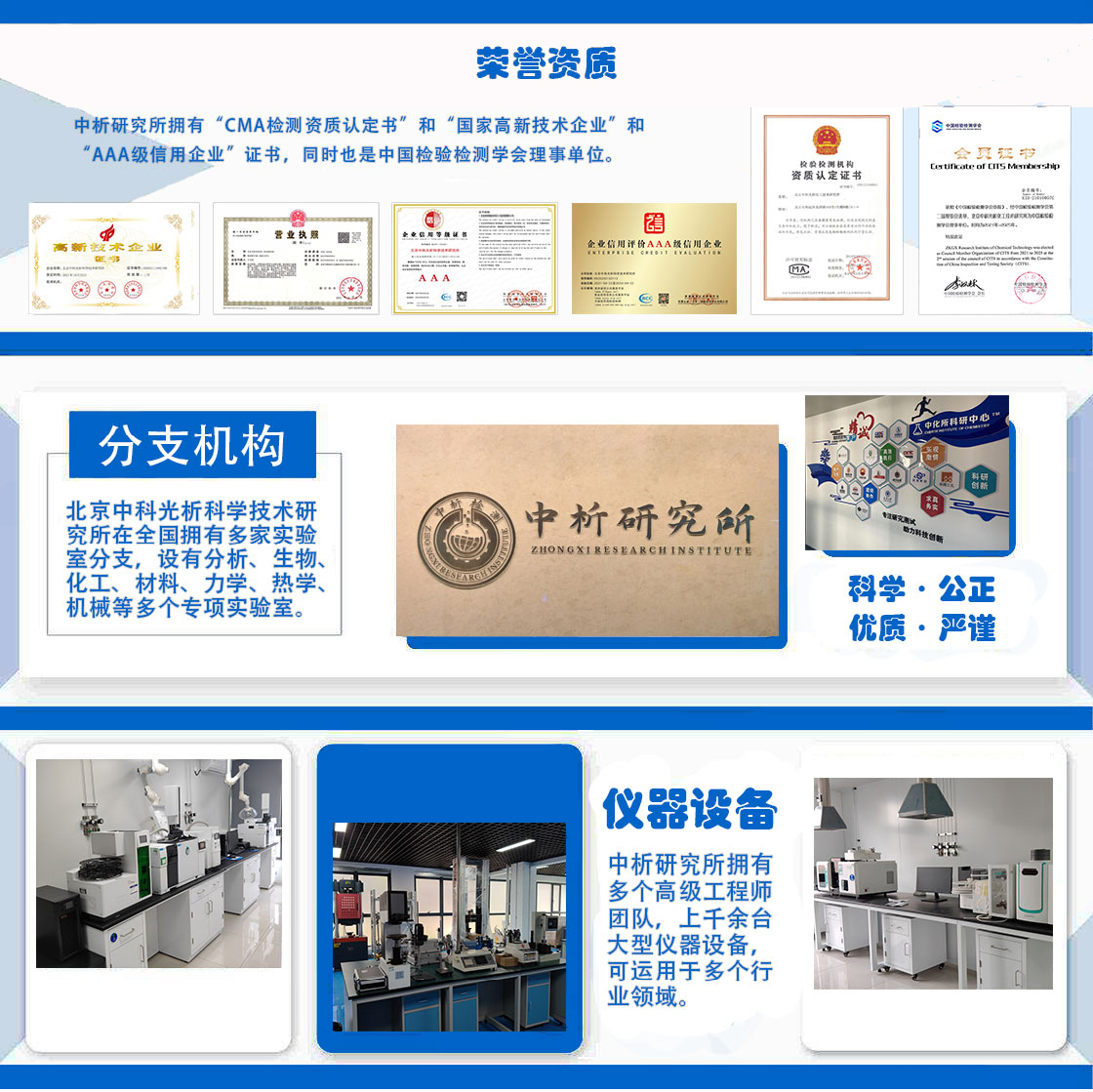
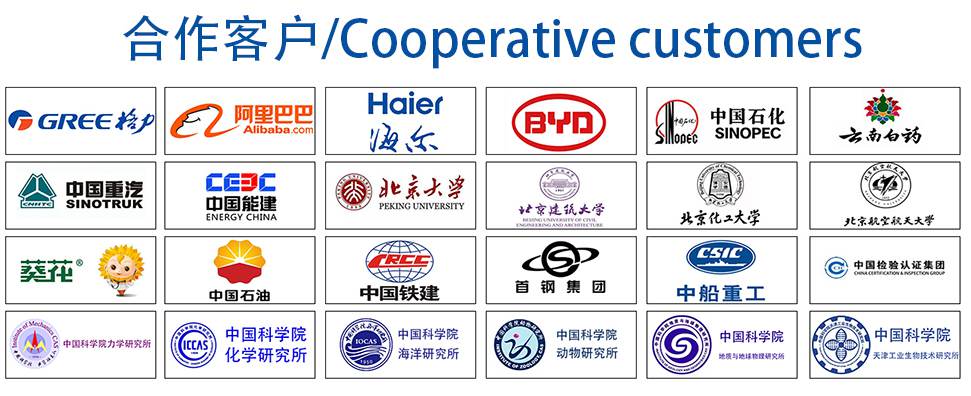
材料实验室
热门检测
16
13
16
12
13
15
13
17
15
15
15
14
12
24
13
16
17
16
13
11
推荐检测
联系电话
400-635-0567