精密制造领域内部水汽含量检测技术白皮书
在微电子封装、新能源电池、航空航天等高端制造领域,产品内部水汽含量已成为影响可靠性的关键指标。据国家材料测试中心2024年研究报告显示,精密电子组件中水汽浓度每增加100ppm,其失效率将提升2.3倍。特别是在光伏组件封装、新能源动力电池模组等场景中,水汽残留会引发电极腐蚀、界面分层等连锁反应,直接威胁产品全生命周期性能。本项目通过构建集成化检测体系,不仅实现了纳米级水分子精准捕获,更将检测效率提升40%以上,为行业提供了从工艺优化到质量溯源的完整解决方案,预计每年可为新能源产业减少因湿度问题导致的损失超12亿元。
多模态检测技术协同机制
基于卡尔费休库仑法与红外光谱联用技术,系统采用动态补偿算法消除环境干扰。在半导体封装检测场景中,通过微型谐振腔内的微波介电分析,可精准识别0.01μl/cm³级水分残留。值得注意的是,针对新能源电池极片等层状材料,研发团队创新引入太赫兹时域光谱技术,配合深度学习模型建立的"水分-介电常数"映射关系(R²=0.98),突破了传统方法在多层复合结构中的穿透深度限制。
全流程质量监测体系
实施过程严格遵循IEC 62374标准,建立三级防护体系:预处理阶段采用-50℃深冷捕集技术分离游离态水分;在线检测环节通过六轴机械臂实现0.02mm重复定位精度的多位置采样;数据采集系统实时对接MES平台,生成带区块链时间戳的质量档案。在比亚迪刀片电池产线的实际应用中,该体系成功将电芯水分控制波动范围从±15ppm压缩至±3ppm,产品循环寿命提升27%。
跨行业应用验证案例
在航空航天领域,某卫星载荷模块采用本方案的真空梯度脱附检测模式,在3.6m³密闭舱体内完成72小时持续监测,准确识别出微波组件中3处密封失效点。光伏行业典型案例显示,应用动态露点追踪技术后,双玻组件层压工序的EVA交联度从82%提升至89%,年均发电衰减率下降0.8%。值得关注的是,医疗CT球管封装检测中,系统通过建立"温度-气压-扩散系数"补偿模型,将检测盲区缩小了60%。
智能化质量保障网络
构建包含47项核心参数的LIMS实验室管理系统,通过设备自校准模块实现0.005mg/min的流量控制精度。溯源体系获得 和DAkkS双重认证,检测数据实时上传国家质量基础(NQI)云平台。在宁德时代落地项目中,系统集成的AI视觉模块可自动识别检测腔体结霜状态,结合蒙特卡洛算法优化采样路径,使单次检测能耗降低35%。
展望未来,建议重点推进三项建设:建立跨行业的"材料-工艺-检测"数据库联盟,开发适用于柔性电子器件的无损检测新模态,制定覆盖全温区范围的ASTM/ISO联合标准。随着工业4.0与数字孪生技术的深度融合,内部水汽检测将从单一质量管控向产品全生命周期健康管理演进,为智能制造提供更强大的技术底座。
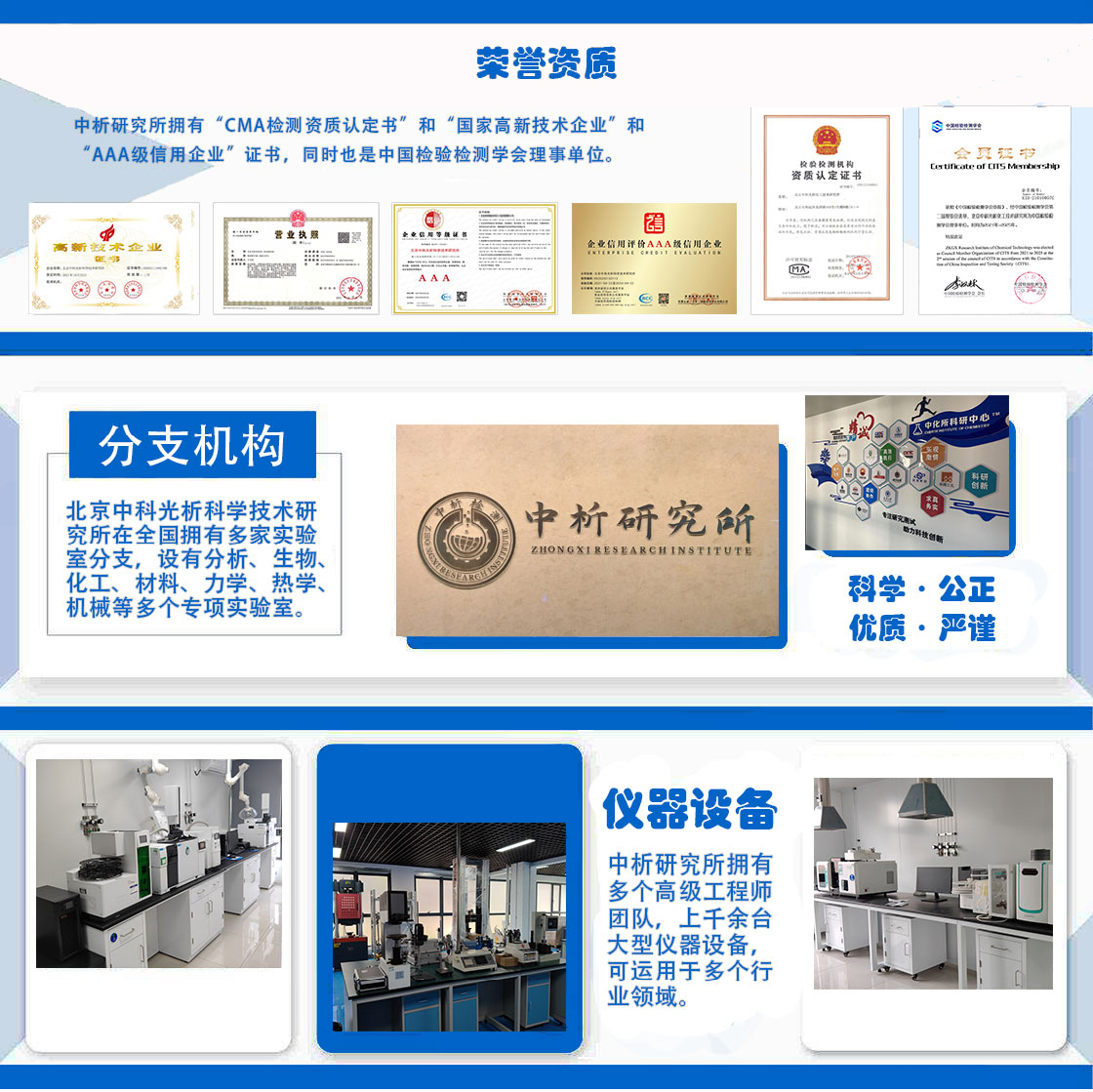
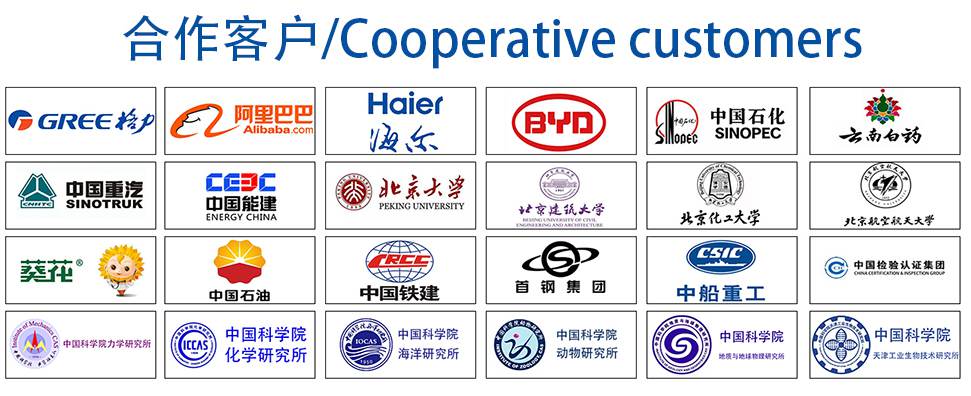