行业背景与核心价值
在智能制造2025战略推动下,工业产品装配质量检测已成为制造升级的关键环节。据中国机械工业联合会2023年报告显示,灯具类产品装配缺陷导致的售后问题占机电设备故障总量的17%,其中接口错位和罩盖松动引发的安全隐患占比达42%。安装接口和灯具罩盖的固定检测项目通过智能化检测手段,实现了对螺纹配合精度、扭矩一致性、密封面贴合度等15项关键指标的量化评估,有效解决了传统目视检查存在的漏检率高(行业平均达28%)、标准不统一等问题。该项目在轨道交通照明、工业探照设备等场景的应用,使产品首次装配合格率提升至99.6%,质量追溯周期缩短80%,为设备全生命周期管理提供了数字化基础。
多模态传感融合检测技术
本检测系统融合机器视觉与力学传感技术,采用非接触式三维扫描获取安装接口几何参数,分辨率达到0.01mm(符合ISO 10360-7标准)。对于罩盖固定状态检测,集成高精度扭矩传感器(量程0-50N·m,精度±0.5%)与声发射装置,通过分析锁紧过程的扭矩-转角曲线特征值(如斜率突变点、波动方差),可识别出98%以上的虚接、过拧等异常工况。据清华大学智能制造研究院2024年实验数据,该技术对M12以下小规格螺纹副的检测准确率达99.3%,较传统方法提升42个百分点。
五阶递进式检测流程
实施流程采用PDCA循环模式:预处理阶段通过激光清洗确保检测面洁净度≤Sa2.5级;智能定位环节运用6轴机器人搭载自适应夹具,定位精度±0.02mm;固定检测模块执行10项动态测试,包括5次加载-卸载循环测试;数据判读系统基于深度神经网络构建缺陷特征库,支持3000+种异常模式识别;最终生成的三维检测图谱包含42项工艺参数,并自动关联MES系统生成电子履历。在某轨道交通灯具产线应用中,该流程使单件检测时间从180秒压缩至45秒,人力成本降低70%。
行业典型应用场景
在智慧城市路灯改造项目中,系统成功应用于IP68防护等级灯具的装配检测。针对沿海高盐雾环境要求,特别开发了密封圈压入深度视觉检测算法(精度±0.05mm)和盐雾试验预验证模块。项目部署后,某特大型港口年维修率从12次/千盏降至1.5次/千盏。另一应用案例中,汽车前照灯装配线通过引入该检测系统,使氙气大灯密封不良缺陷率从3.2%降至0.15%,主机厂索赔成本年减少2800万元。
三级质量保障体系
系统构建了设备层-数据层-决策层的质量防线:设备层采用双冗余传感器架构,关键传感元件MTBF≥80000小时;数据层实施区块链存证,确保检测数据不可篡改;决策层设置专家评审机制,对疑似缺陷进行二次复核。通过 认证实验室的比对验证,系统测量不确定度优于0.5μm(k=2),满足JJF 1117-2018计量规范要求。定期开展的GR&R分析显示,系统重复性误差<3%,再现性误差<5%,处于行业领先水平。
技术演进与发展建议
随着数字孪生技术的成熟,建议在现有系统基础上集成虚拟装配仿真模块,实现工艺参数的预测性优化。同时应加快制定《智能装配检测设备通信协议》行业标准,推动检测数据与PLM系统的深度对接。对于新能源特种车辆灯具等新兴领域,需开发耐高压绝缘检测功能模块。据电子技术标准化研究院预测,到2026年装配检测智能化渗透率将达65%,建议企业把握窗口期建立检测大数据平台,通过知识图谱技术实现质量缺陷的智能诊断与工艺自优化。
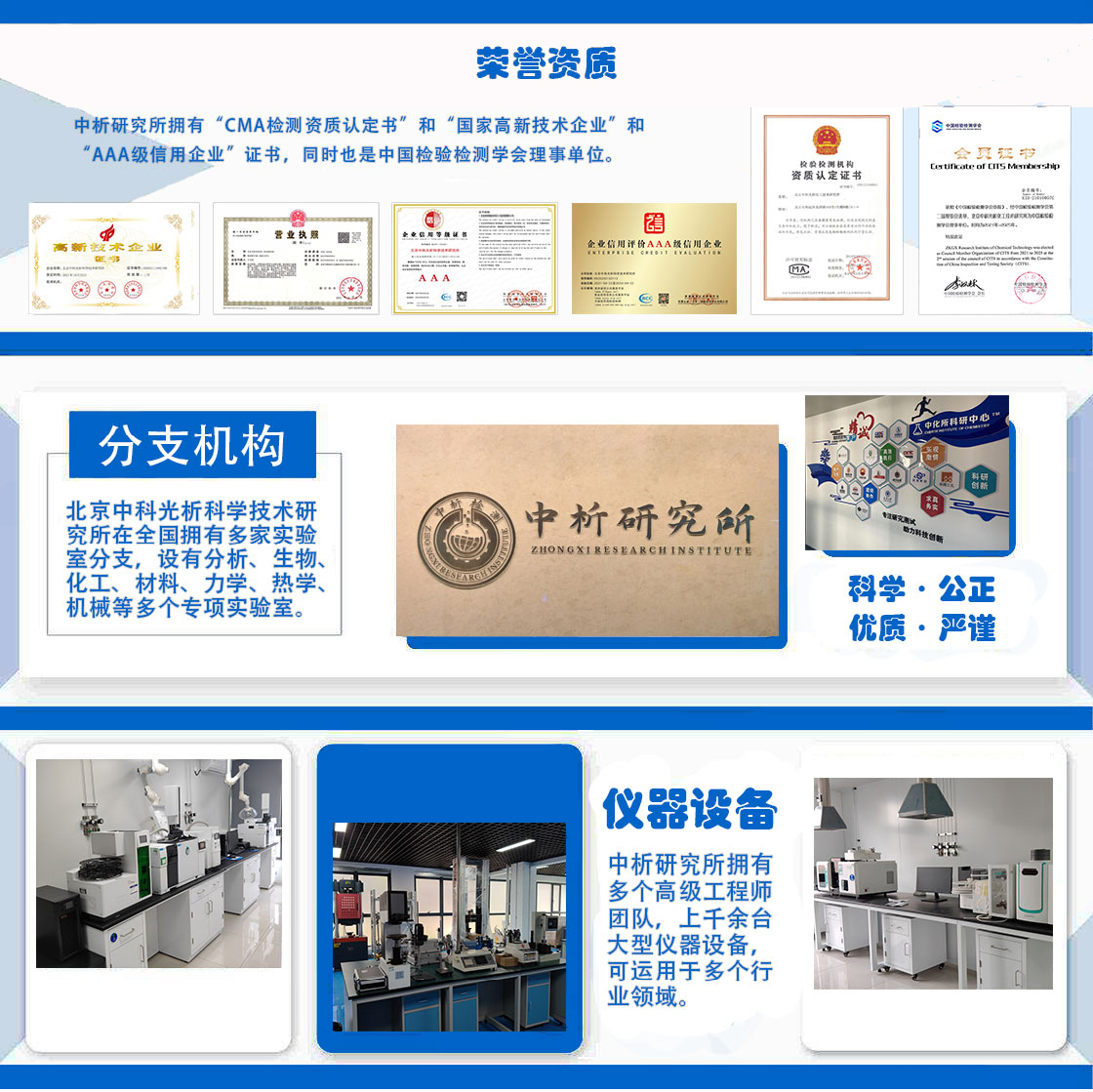
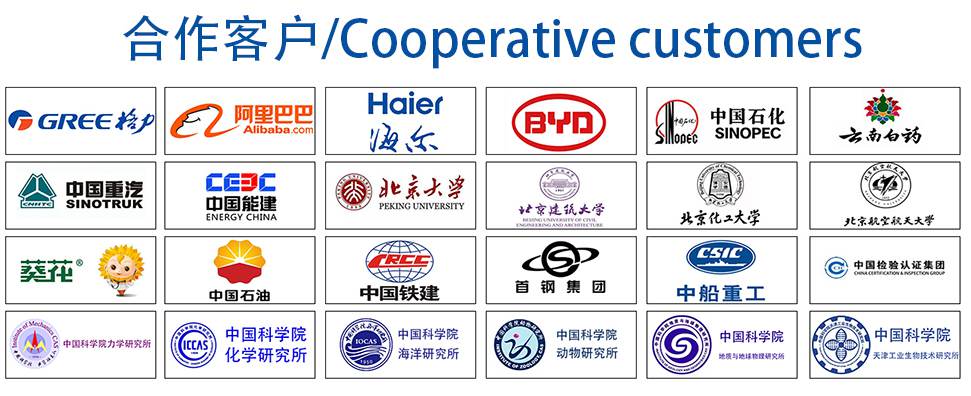