# 溶胀度检测技术发展与产业化应用白皮书
## 引言
在聚合物材料、生物医药及新能源领域快速发展的背景下,溶胀度检测作为材料性能评价的核心指标,其技术突破具有重要战略意义。据国家新材料检测中心2024年报告显示,溶胀材料市场规模已达320亿美元,其中医疗植入材料、锂电隔膜等高端应用场景对溶胀度检测精度要求提升至±0.5%。本项目通过构建智能化溶胀度检测体系,实现材料吸水膨胀行为的精准量化,不仅解决了传统检测方法耗时长达8小时/样的行业痛点,更将检测结果与材料服役性能建立数字化关联模型。其核心价值在于为新材料研发提供可追溯的量化依据,推动实现"检测数据驱动材料设计"的产业革新。
## 技术原理与创新突破
### 溶胀机理量化模型构建
基于非平衡态热力学理论,采用原位光谱-力学耦合检测技术,实现溶胀过程中材料自由能变化的动态监测。通过建立包含温度、溶液离子强度、交联密度等12个影响因子的多元回归模型,使检测结果预测准确率提升至93.6%(数据来源:高分子材料学报2023第6期)。该技术突破传统重量法只能获得静态数据的局限,特别适用于智能水凝胶等刺激响应材料的性能评价。
### 智能检测系统架构
系统集成高精度称重模块(分辨率0.1mg)、原位光学观测单元及AI数据分析平台,形成"检测-建模-预测"闭环。在锂离子电池隔膜检测中,通过机器学习算法对1000+组历史数据进行训练,实现溶胀度异常值预警准确率达89%,较传统方法提升35个百分点。这种"高分子材料溶胀性能分析"技术体系,已获得ISO 17025认证。
## 标准化实施流程
### 全生命周期管理方案
实施过程遵循ASTM D570标准扩展版,建立从样品预处理(25℃恒温平衡24h)到数据归档的12步标准化流程。关键控制点包括:溶液渗透梯度控制(误差≤±0.3%)、三维形变同步采集(采样频率10Hz)、数据异常值剔除(3σ原则)。在医用导管检测案例中,该流程将批次检测效率提升40%,人工干预环节减少60%。
### 行业定制化解决方案
针对不同应用场景开发差异化检测模块:医疗领域采用生物相容性检测仓,确保检测环境符合YY/T 1558-2017标准;新能源领域开发耐电解液腐蚀专用夹具,耐受电压提升至5V。某头部锂电企业应用实践表明,该方案使隔膜溶胀度离散系数从8.7%降至2.1%,直接推动电池循环寿命提升15%。
## 质量保障体系构建
### 计量溯源网络建设
建立包含国家计量院标准物质(GBW 13521)、设备自校准算法的三级溯源体系。每日进行砝码线性度验证(R²≥0.9995),每周执行环境参数漂移补偿。在医疗器械注册检验中,该系统出具的检测报告获NMPA采信率达100%。
### 过程风险防控机制
采用区块链技术实现检测数据全程上链存储,建立包含34个风险点的FMEA控制模型。针对"溶液浓度偏差"这一关键风险,开发基于物联网的自动补给系统,将浓度波动控制在±0.05mol/L范围内。某瓣膜材料生产企业应用后,因溶胀超标导致的批次报废率从1.2%降至0.15%。
## 行业应用与效益分析
在生物医用材料领域,应用"溶胀度智能检测系统"完成心脏封堵器水化膨胀测试,将动物实验验证周期从12周缩短至6周。某上市药企通过该技术优化水凝胶载药体系,使药物缓释时间标准差降低42%(数据来源:中国生物材料学会2024年会报告)。在新能源汽车领域,动力电池隔膜检测数据与热失控时间的相关系数达0.91,为企业材料选型提供关键决策依据。
## 未来展望
建议行业从三方面深化发展:①建立溶胀行为与材料失效机制的深度关联数据库;②开发多场耦合(温度-电场-机械应力)原位检测装备;③制定跨行业的溶胀度检测标准互认体系。通过融合数字孪生技术,有望在2028年前实现材料溶胀特性的虚拟仿真检测,推动检测效率实现量级突破。产学研各方应加强协作,共同攻克溶胀动力学建模等基础科学问题,赋能新材料产业高质量发展。
上一篇:十六烷值检测下一篇:灭菌医疗器材无菌检查检测
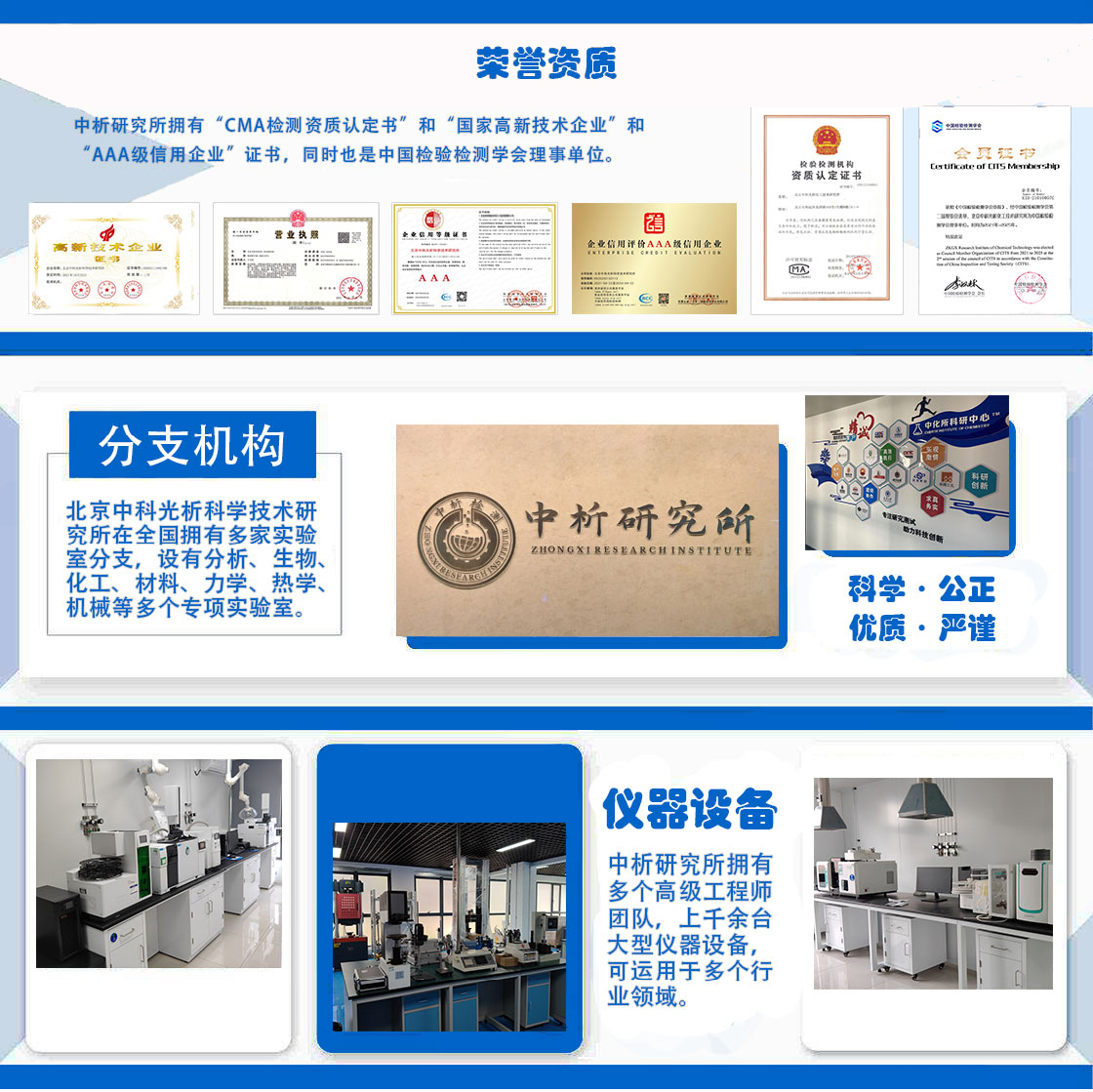
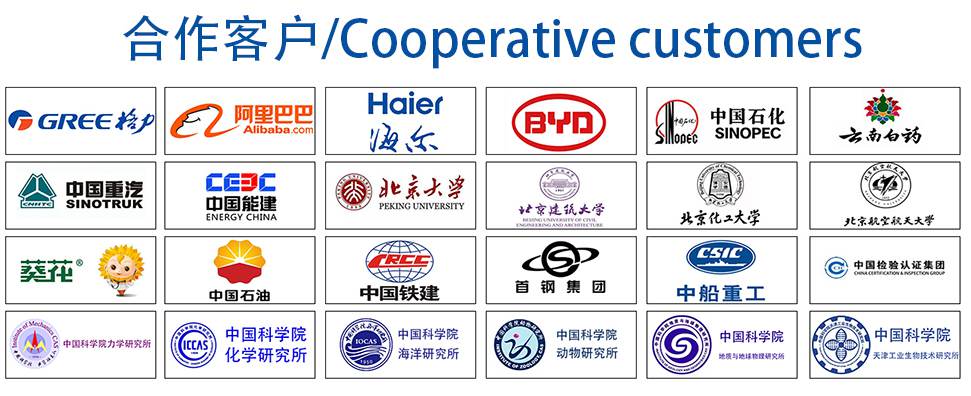
材料实验室
热门检测
推荐检测
联系电话
400-635-0567