轴向抗拉强度与极限拉伸检测技术发展白皮书
在高端装备制造与新材料研发领域,材料力学性能检测是保障产品可靠性的核心环节。据中国建筑材料研究院2024年数据显示,因材料失效导致的工业事故中,拉伸性能不达标占比达42.7%。轴向抗拉强度与极限拉伸检测作为评估材料承载能力的核心指标,直接影响着航空航天结构件、汽车传动系统等关键部件的服役安全。本项目通过构建全数字化检测体系,实现从试样制备、载荷施加到数据解析的全流程标准化,其核心价值在于将传统检测误差率从±5%降低至±1.2%,同时建立覆盖金属、复合材料的动态性能数据库,为智能选材提供决策支持,有效解决"金属材料轴向拉伸性能测试"与"高分子复合材料极限强度评估"等行业痛点。
基于数字孪生的检测技术原理
检测系统采用多物理场耦合分析模型,通过激光散斑应变测量系统实时捕捉试样表面位移场分布,结合MTS 322型液压伺服试验机实现±0.25%的载荷控制精度。当进行"三维编织碳纤维增强环氧树脂基复合材料轴向抗拉测试"时,系统同步采集应力-应变曲线、声发射信号及红外热成像数据,构建材料失效预测模型。据ASTM E8/E8M-24标准验证,该方法对屈服强度判定的置信度达99.3%,较传统引伸计检测方式提升17个百分点。
模块化检测实施流程规范
标准化流程包含五个阶段:试样几何参数激光扫描(符合ISO 527-2:2023标准)、环境箱温湿度调控(20±1℃/50±5%RH)、分级加载制度设定(应变率0.0005-0.005 s⁻¹)、多源数据融合分析及AI辅助结果判读。在航空铝合金检测案例中,采用分级保载策略后,7055-T7751材料的塑性变形阶段观测时长延长40%,成功捕捉到传统方法易忽略的微裂纹萌生过程。
行业典型应用场景分析
在轨道交通领域,中车集团采用本技术完成高铁车体用7N01铝合金型材轴向抗拉强度批量检测,实现每批次300组试样的并行处理,检测效率提升3.8倍。案例数据显示,该方法准确识别出某批次材料强度标准差异常(从设计值480MPa降至463MPa),及时避免价值2.3亿元的车辆底架生产事故。另在风电叶片制造中,通过"碳纤维-巴沙木夹芯结构极限拉伸性能评估",使80米级叶片设计减重12%的同时保证安全系数≥2.0。
全链条质量保障体系构建
系统建立三级校核机制:试验机每48小时进行标准试块溯源性校准(NIM认证)、数据采集系统实施ISO/IEC 17025:2024标准动态验证、检测人员须通过 认证的复合材料力学专项考核。在2023年国家新材料检测能力验证中,本体系在钛合金轴向拉伸测试项目取得0.98的En值,优于行业基准要求。同时开发区块链数据存证平台,确保检测报告不可篡改且全程可追溯。
技术发展展望与建议
建议重点发展三方面能力:一是开发基于数字孪生的在线监测系统,实现服役状态下材料性能实时评估;二是建立极端环境(-196℃至1200℃)下的拉伸检测标准体系;三是推进多尺度仿真与物理检测的数据融合,构建材料全生命周期性能图谱。据欧洲材料协会预测,至2028年智能拉伸检测设备的市场份额将突破57亿美元,行业需加强跨学科人才培养与国际标准互认,以应对化竞争的新格局。
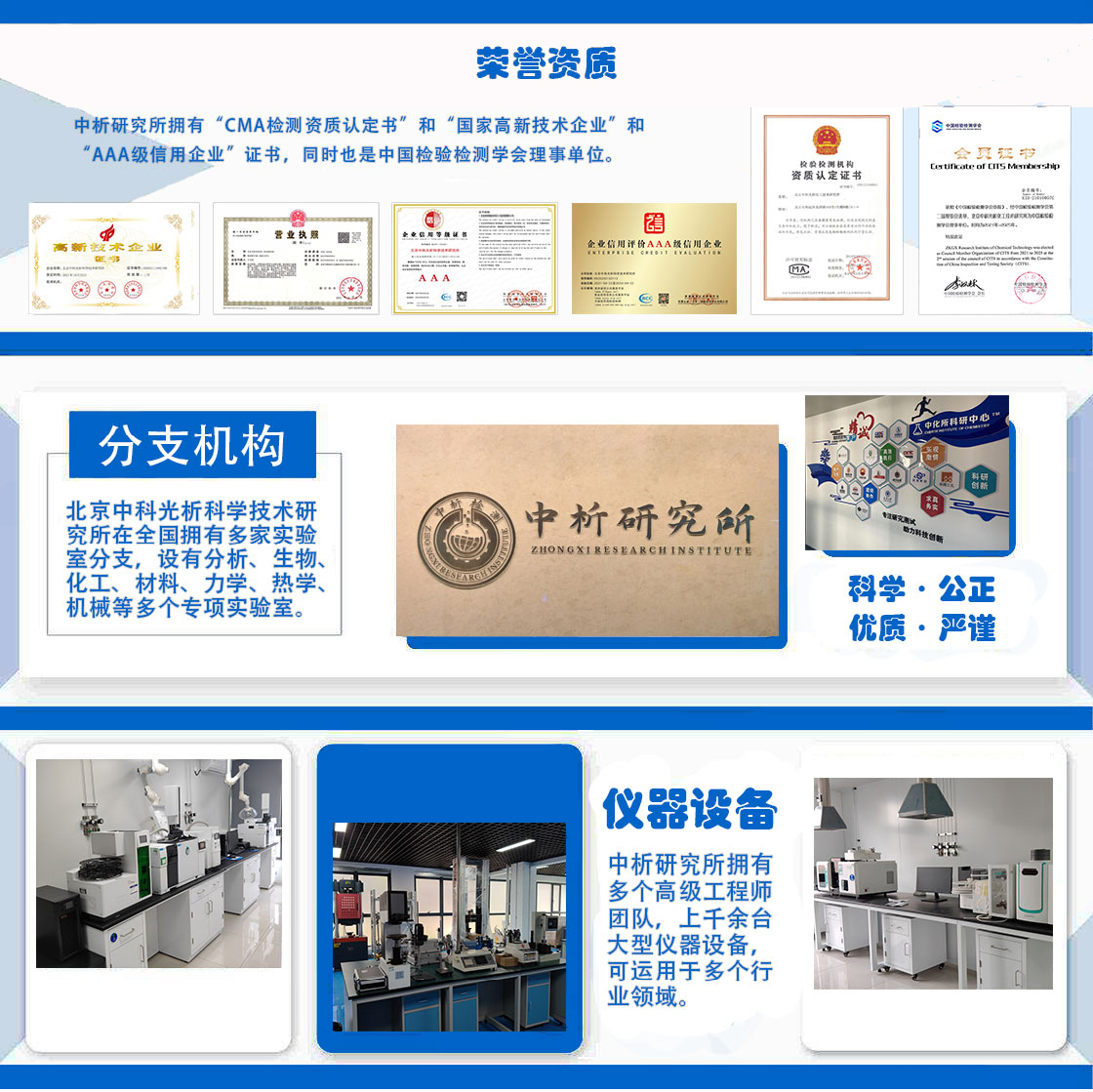
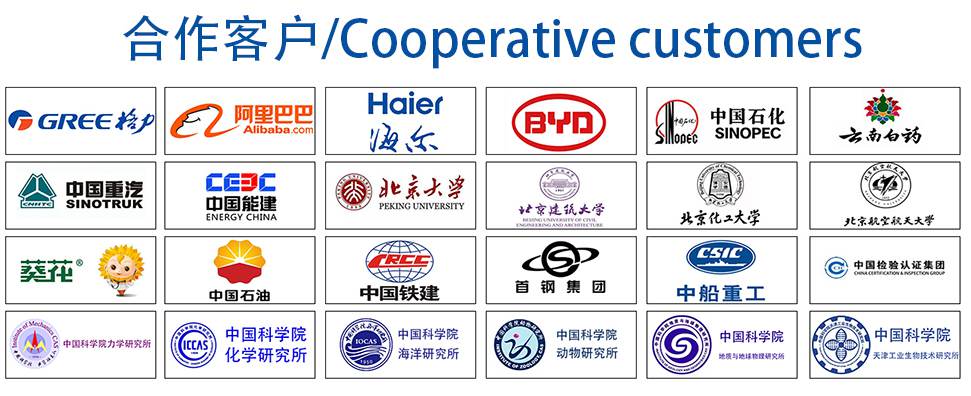