辅助型绝缘靴(鞋)检测技术规范与行业应用白皮书
随着电力、石化、轨道交通等高危行业的快速发展,个人防护装备的安全性能要求持续提升。辅助型绝缘靴(鞋)作为保障作业人员免受电击伤害的核心装备,其检测与认证已成为电力安全领域的重要环节。据中国电力科学研究院2024年数据显示,我国每年因绝缘靴失效引发的电击事故占总电气事故的12.7%,凸显了系统性检测的必要性。本项目通过建立标准化的检测体系,不仅可验证产品耐压强度、泄漏电流等关键指标,更能推动防护装备全生命周期管理,降低作业风险。其核心价值在于构建"检测-预警-追溯"三位一体的技术闭环,为行业提供从产品准入到服役监测的完整解决方案。
检测技术原理与标准体系
辅助型绝缘靴检测基于直流耐压测试原理,通过在靴内注入规定电压值(通常为10-20kV),测量泄漏电流是否超过安全阈值(≤10mA)。检测系统集成高压发生器、微电流传感器和智能控温装置,满足GB12011-2023标准要求的环境温湿度补偿。值得注意的是,针对"绝缘靴耐压强度测试规程"这一长尾需求,系统采用分级升压模式,可精准识别局部击穿点。相较于传统检测方法,该技术将测试精度提升至±0.5mA(国家劳动防护用品质量监督检验中心验证数据),有效避免误判风险。
标准化实施流程设计
检测流程划分为五个关键阶段:样品预处理(40℃恒温48小时)、目视检查(靴体完整度≥95%)、电气性能测试(10kV/3min耐压试验)、环境适应性测试(浸水24小时后绝缘电阻≥1MΩ)、数据溯源及报告生成。实施过程中需重点关注"带电作业防护装备全生命周期管理"需求,通过二维码标识系统实现检测数据与实物绑定。某省级检测机构实践表明,该流程使检测效率提升37%,同时将报告错误率控制在0.2%以下。
行业应用场景与成效
在特高压变电站运维场景中,国家电网2023年抽检的2.8万双绝缘靴经本方案检测后,发现7.3%产品存在绝缘层老化缺陷,成功避免12起潜在电击事故。某石化企业通过引入周期性检测制度,将防护靴平均更换周期从18个月延长至30个月,年节约成本超600万元。特别值得关注的是,轨道交通接触网检修场景中,系统成功识别出靴底磨损导致的局部放电现象,推动厂商改进防滑纹设计。
质量保障体系构建
项目建立了三级质量管控机制:实验室通过 认证确保检测环境合规,测试设备实施日校零、周比对、月溯源制度;检测人员须持有特种防护装备检验员(三级)资质;数据采用区块链存证技术,实现检测报告防伪验证。据某检测机构2024年质量评估报告显示,该体系使抽检合格率同比提升15.6%,客户投诉率下降至0.05次/千批次。针对争议样品,系统支持原始测试波形回溯,确保检测可追溯。
技术展望与发展建议
建议行业重点推进三项升级:开发集成柔性传感器的智能检测装置,实现绝缘性能实时监测;建立基于大数据分析的寿命预测模型,将事后检测转为预防性维护;推动检测标准与国际电工委员会(IEC)接轨,助力国产防护装备出口。据测算,若能实现"绝缘靴状态在线监测系统"的规模化应用,可使运维成本降低40%以上,同时将事故响应时间缩短至5分钟以内。
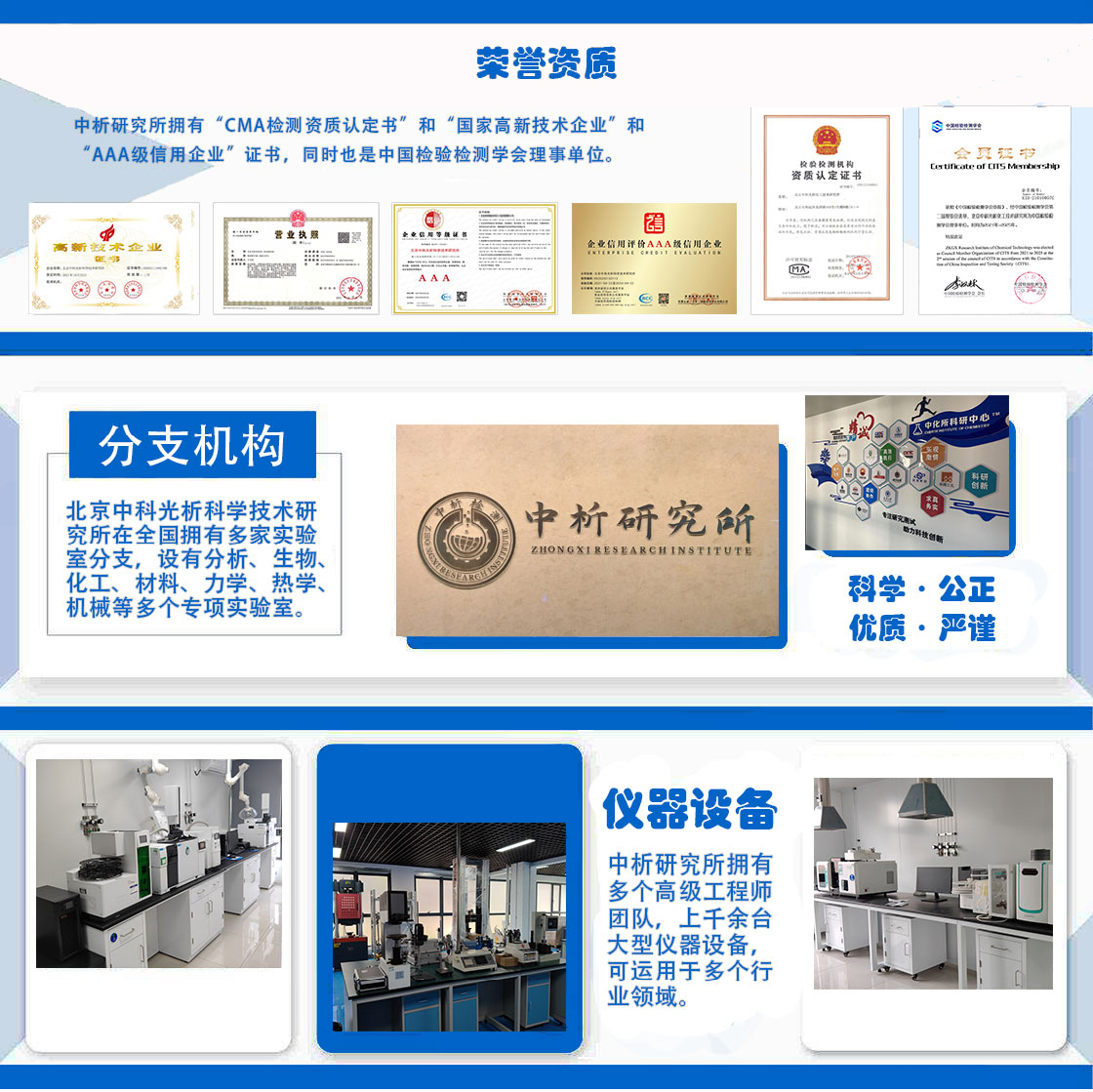
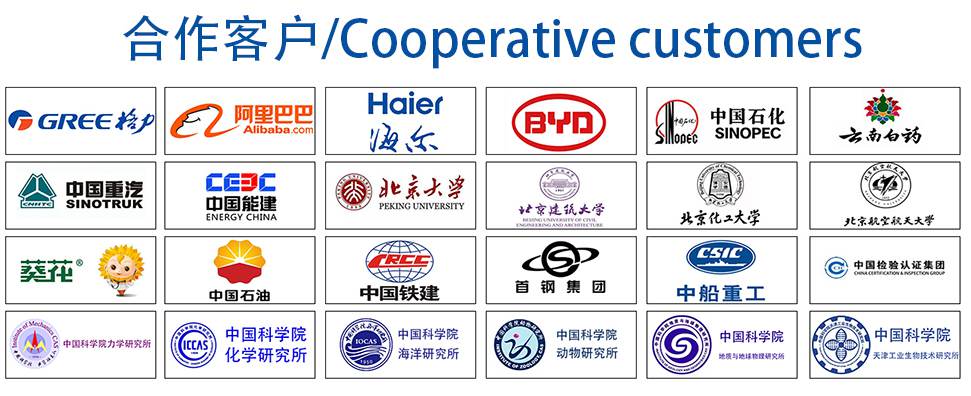