整体加重钻杆检测的重要性与技术要求
整体加重钻杆作为石油天然气钻井作业中的关键部件,承担着传递扭矩、承受轴向载荷及维持井眼轨迹的重要任务。由于其长期处于高强度、高磨损、高腐蚀的复杂工况下,任何微小的缺陷都可能导致钻杆断裂、钻井效率下降甚至安全事故。因此,对整体加重钻杆进行系统化、标准化的检测,是保障钻井作业安全性和经济性的核心环节。检测工作需覆盖材料性能、结构完整性、表面状态及连接可靠性等多个维度,并严格遵循API SPEC 7-1、ISO 11961等国际标准要求。
检测项目及内容详解
1. 外观与尺寸检测
通过目视检查、卡尺测量及三维扫描技术,评估钻杆表面是否存在裂纹、凹坑、锈蚀等缺陷,并验证外径、壁厚、长度等关键尺寸是否符合公差要求。重点关注接头螺纹区域的磨损程度,确保其与工具接头的匹配性。
2. 材料成分与力学性能分析
采用光谱仪、拉伸试验机、冲击试验机等设备,检测钻杆材料的化学成分(如C、Mn、Cr、Mo含量)、抗拉强度、屈服强度、延伸率及冲击韧性。需确保材料性能满足API标准中对高强度低合金钢的特定要求,同时验证热处理工艺的均匀性。
3. 无损探伤检测
综合应用超声波检测(UT)、磁粉检测(MT)和渗透检测(PT):
- 超声波检测:识别钻杆内部缺陷(如夹杂、气孔)及壁厚减薄区域;
- 磁粉检测:检测表面及近表面裂纹等线性缺陷;
- 渗透检测:辅助验证非磁性材料表面开口型缺陷。
4. 螺纹连接检测
使用专用螺纹规、投影仪及扭矩测试仪,评估API标准螺纹(如NC50、FH等)的齿形精度、啮合间隙及抗扭性能。重点检查螺纹根部应力集中区域的疲劳裂纹,并通过上卸扣试验模拟实际工况下的密封性和耐久性。
5. 静水压试验
在1.5倍额定工作压力下进行保压测试,持续5分钟以上,验证钻杆本体及接头的抗压强度和密封性能。试验过程中需监测是否出现渗漏或塑性变形现象,压力曲线需完整记录。
6. 残余应力分析
采用X射线衍射法或盲孔法,评估制造过程中产生的残余应力分布,尤其关注过渡带和加厚端区域。残余应力值需控制在材料屈服强度的20%以内,以避免应力腐蚀开裂风险。
7. 疲劳寿命评估
通过旋转弯曲疲劳试验机模拟实际交变载荷工况,结合有限元应力分析,预测钻杆在复杂应力状态下的疲劳寿命。测试结果需与API RP 7G推荐的疲劳强度曲线进行对比验证。
检测周期与质量控制
新出厂钻杆需执行全项目检测,在役钻杆每3年或累计钻井深度达50,000米时应进行复检。检测数据应建立数字化档案,利用大数据分析实现寿命预测与失效预警,为钻井方案优化提供科学依据。
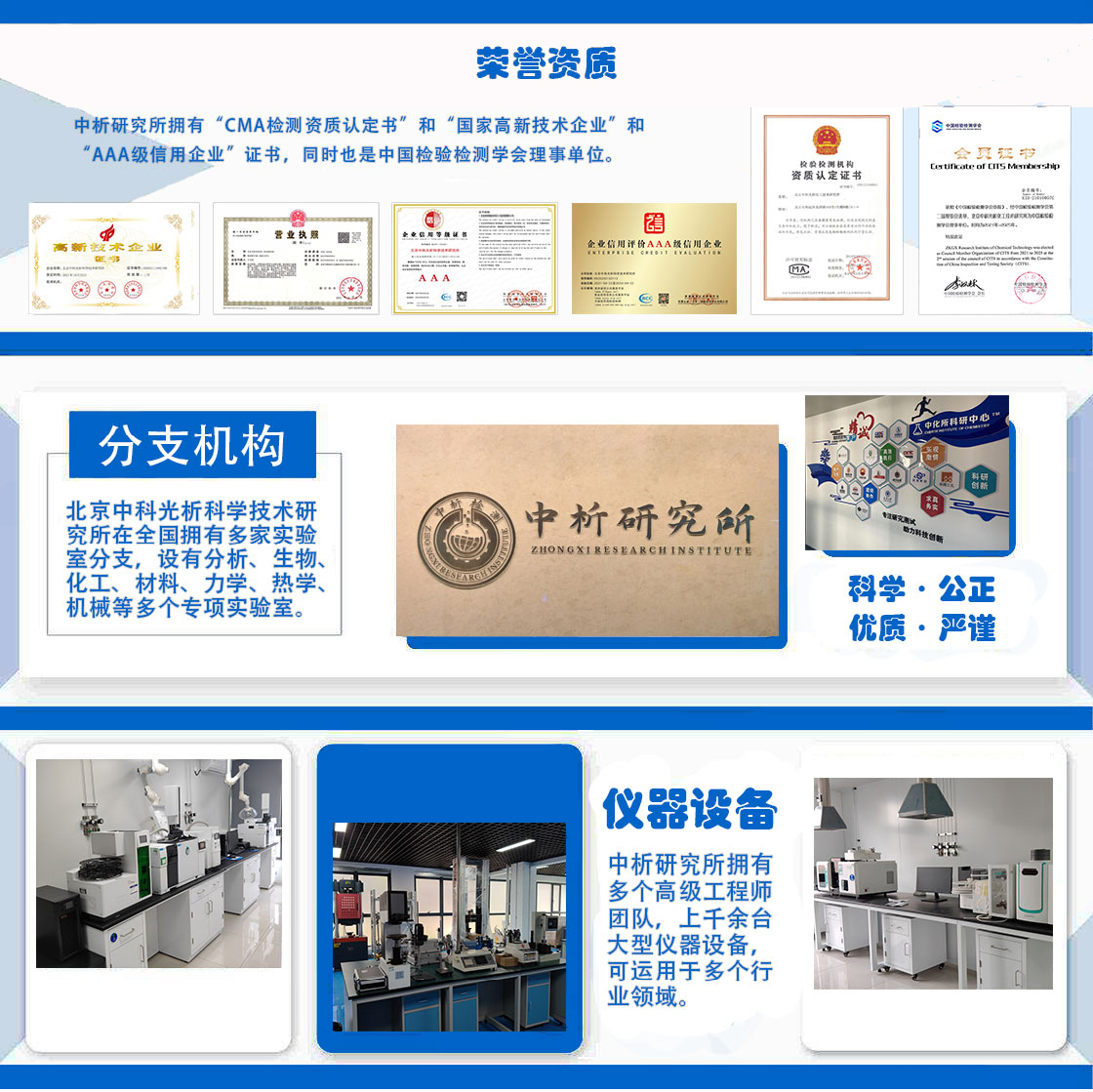
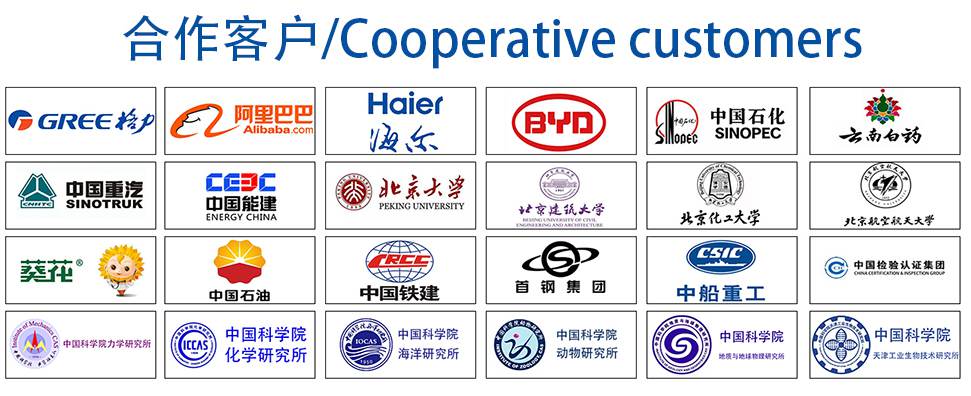