主蒸汽管道、再热蒸汽管道及导汽管检测的重要性
在火力发电厂、化工装置等高温高压设备系统中,主蒸汽管道、再热蒸汽管道及导汽管作为能量传输的核心通道,长期承受高温(500-600℃)、高压(10-30MPa)及交变应力作用。其工作状态直接关系到机组安全运行和能源转换效率。随着设备服役时间的延长,管道材料易发生蠕变损伤、氧化腐蚀、应力裂纹等缺陷,严重时可能引发爆管事故。因此,通过系统化的检测手段评估管道健康状态,已成为预防性维护及寿命管理的关键环节。
核心检测项目与技术方法
1. 外观与几何尺寸检测
采用目视检查、内窥镜探查与激光扫描技术,重点检测管道外表面锈蚀、氧化皮剥落、鼓包变形等异常现象。使用超声波测厚仪进行壁厚多点测量(间隔≤500mm),对比原始设计数据评估减薄量。对弯头、三通等应力集中区域实施椭圆度测量,控制椭圆变形率≤5%。
2. 无损探伤检测
通过组合式无损检测技术进行缺陷识别:
- 磁粉检测(MT):检测表面及近表面裂纹(灵敏度0.1mm)
- 渗透检测(PT):验证非磁性材料表面开口缺陷
- 超声波检测(UT):采用相控阵技术识别内部裂纹、分层缺陷,最小检出尺寸Φ2mm
- 射线检测(RT):对焊缝实施数字射线成像(DR),缺陷检出率≥95%
3. 材料性能退化评估
通过现场取样或原位测试手段:
- 金相分析:评估珠光体球化等级(按DL/T 674标准分级)
- 硬度测试:采用里氏硬度计检测硬度变化(偏差>30HB需预警)
- 蠕变损伤评估:通过复膜金相法测定蠕变孔洞密度(临界值≥1000个/mm²)
- 碳迁移检测:使用光谱分析仪测定脱碳层深度(允许值<0.5mm)
4. 支吊架系统检测
采用三维激光位移传感器检测支吊架偏移量(垂直方向>5mm需调整),通过液压测力装置校验弹簧支吊架载荷偏差(允许±10%)。检查恒力吊架转体卡涩情况,确保位移补偿功能正常。
5. 焊缝质量综合评价
对安装焊缝和修复焊缝实施100%检测:
- 超声TOFD检测焊缝内部缺陷
- 硬度梯度测试评估焊后热处理效果
- 宏观腐蚀检查焊缝区域氧化状况
- 错边量测量控制不超过壁厚的10%
检测周期与标准依据
根据DL/T 438《火力发电厂金属技术监督规程》要求:
- 主蒸汽管道首次检验在投运5万小时后进行
- 超期机组每年至少开展1次重点部位检测
- 导汽管弯头部位每2个大修周期进行蠕变测量
检测数据需参照ASME B31.1、GB/T 30582等标准进行安全等级评定。
智能检测技术发展
当前行业正推进基于MFL漏磁检测的智能爬行机器人应用,实现Φ508mm以上管道的自动化壁厚测绘。同时,结合FBG光纤传感技术建立管道应变实时监测系统,配合大数据分析平台实现寿命预测精度提升至88%以上。
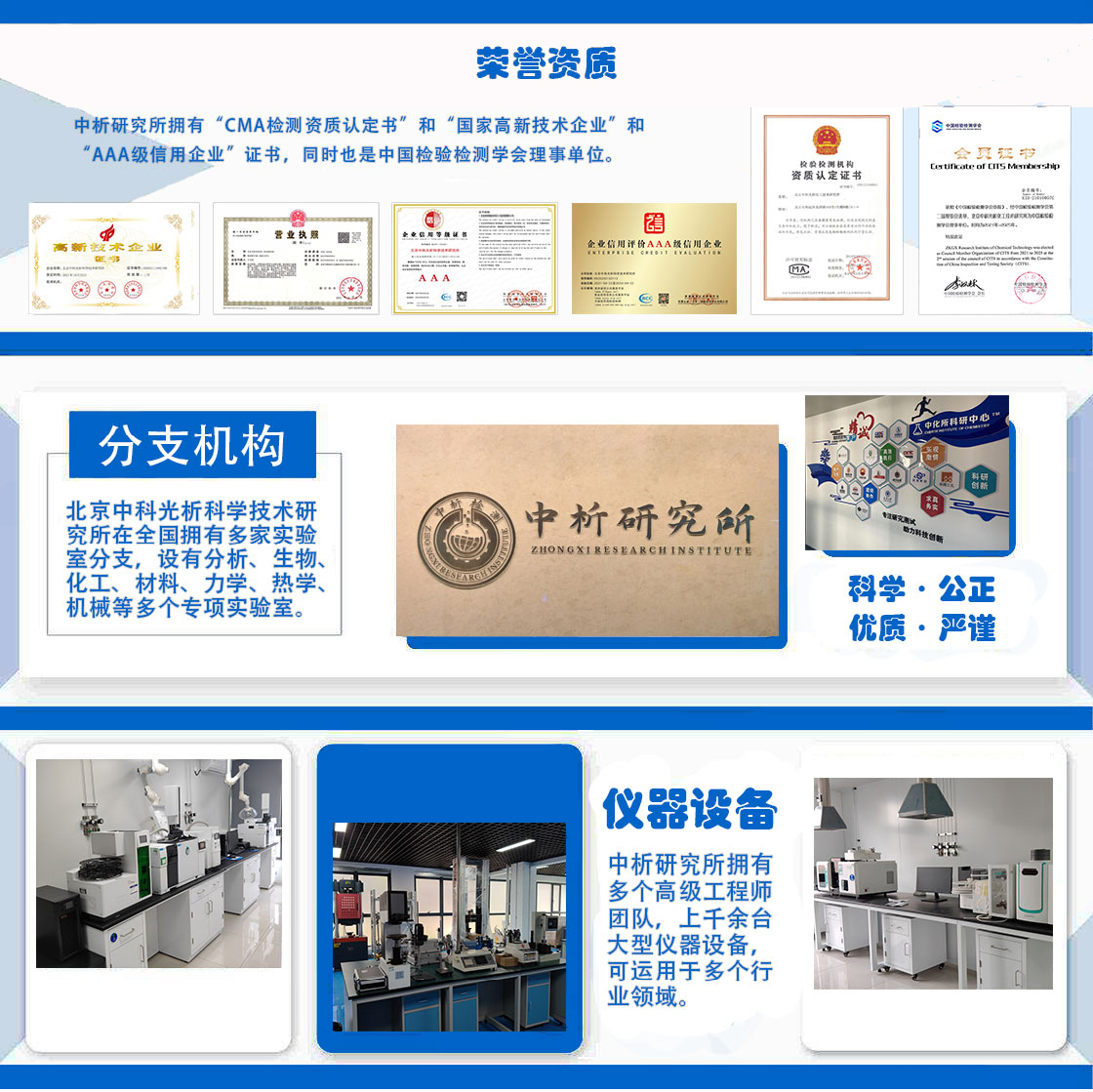
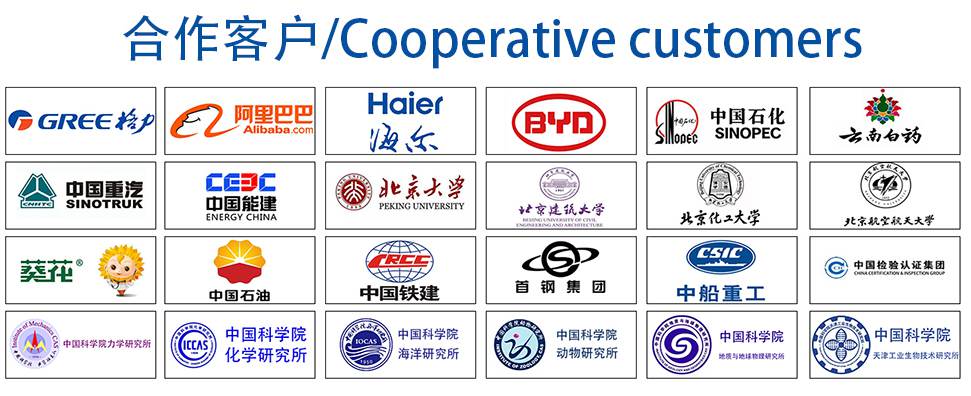