汽轮机检测:关键项目与实施方法
一、运行状态监测
-
- 目的:识别转子不平衡、轴系对中偏差、轴承磨损等问题。
- 方法:安装振动传感器(如加速度计、位移探头),实时采集轴承座和转轴振动数据,结合频谱分析定位故障源。
- 标准:参考ISO 10816,振动幅值超过50μm(峰值)需停机检查。
-
- 关键部位:轴承温度(正常范围:40~70℃)、汽缸壁温、蒸汽进出口温度。
- 技术手段:热电偶、红外热成像仪;异常温升可能预示润滑失效或热应力变形。
-
- 油质分析:黏度、水分含量(≤0.1%)、颗粒污染度(ISO 4406标准)。
- 油压与流量:监测供油压力波动(±5%以内为正常),确保轴承润滑充足。
二、停机检修关键项目
-
- 动平衡测试:使用动平衡机校正转子,残余不平衡量需低于G2.5级标准。
- 叶片检查:目视+磁粉探伤(MT)检测裂纹;测量叶根间隙,超差0.1mm需调整。
- 轴颈与轴瓦:检查磨损量(径向间隙≤0.15mm),巴氏合金层无剥落。
-
- 汽缸水平度:激光准直仪测量,偏差≤0.05mm/m。
- 汽封间隙:塞尺检测,径向间隙控制在0.3~0.5mm,过大导致蒸汽泄漏效率下降。
-
- 高温螺栓硬度:布氏硬度检测(HB 200~250),防止应力松弛。
- 法兰密封面:渗透检测(PT)排查微观裂纹,确保气密性。
三、专项检测技术应用
-
- 超声波检测(UT):用于厚壁汽缸、转子内部缺陷扫描,可发现≥2mm的夹杂或裂纹。
- 涡流检测(ET):检测叶片表面及近表面缺陷,精度达0.1mm。
-
- 方法:测量蒸汽流量、压力、温度,计算实际热效率与设计值偏差(通常允许±3%)。
- 改进方向:优化通流部分间隙、减少级间泄漏损失。
-
- 调速系统响应:阶跃信号测试,转速波动恢复时间应<10秒。
- 保护联锁试验:模拟超速(110%额定转速)、低油压等工况,验证紧急停机可靠性。
四、检测周期与故障预警
- 日常监测:振动、温度、油质等参数需实时监控并记录。
- 定期检测:每3个月进行润滑油化验,每年一次全面停机检查。
- 大修周期:运行4~6万小时或累计启停500次后,需解体大修。
五、未来趋势:智能化检测
- AI诊断系统:基于历史数据训练模型,实现故障早期预警(如轴承磨损趋势预测)。
- 无线传感器网络:减少布线成本,提升监测密度与实时性。
- 数字孪生技术:构建虚拟汽轮机模型,模拟极端工况下的应力分布,优化检修策略。
转成精致网页
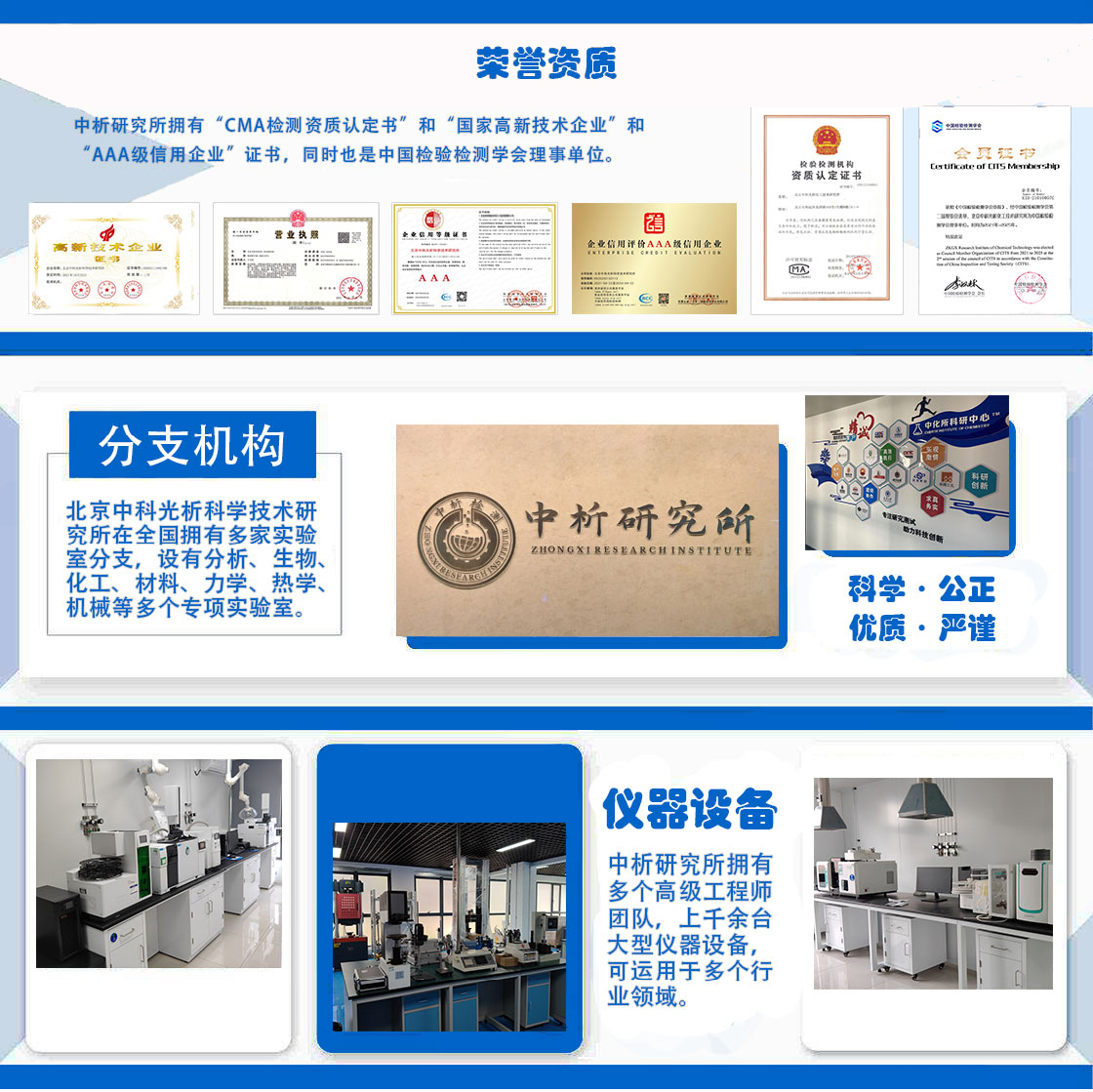
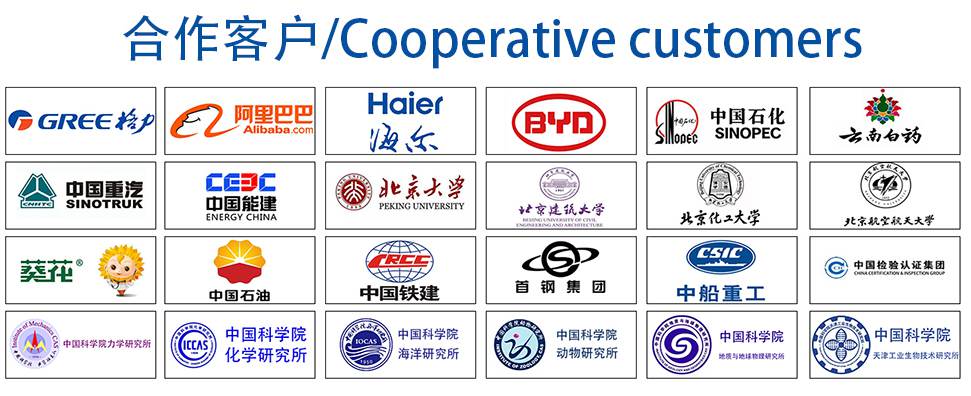
材料实验室
热门检测
26
16
24
21
25
20
22
20
18
23
26
29
26
26
22
21
17
20
24
22
推荐检测
联系电话
400-635-0567