电厂运行中矿物涡轮机油质量检测的重要性
在火力发电、核能发电等大型电厂中,矿物涡轮机油作为汽轮机组的关键润滑介质,承担着润滑轴承、冷却设备、防锈防腐蚀等重要功能。其性能的稳定性直接影响机组运行效率、设备寿命及安全性。长期高温、高压、高转速的工况环境会导致油品氧化、污染、添加剂损耗等问题,若未及时检测和处理,可能引发设备异常磨损、振动加剧甚至停机事故。因此,建立系统化的油品质量检测体系是电厂运维管理中不可或缺的环节。
核心检测项目及技术要求
1. 理化指标检测
包括粘度、酸值、水分、闪点、倾点等基础参数: • 粘度(ISO 3104标准):反映油品流动性,直接影响润滑效果。40℃运动粘度偏差超过±10%需换油; • 酸值(ASTM D664):检测氧化产物,酸值>0.3mgKOH/g表明严重劣化; • 水分含量(ASTM D6304):水分>500ppm会引发乳化,需采用真空脱水处理。
2. 污染度分析
通过颗粒计数器(ISO 4406标准)监测固体颗粒污染: • 汽轮机油NAS清洁度需≤8级; • 金属磨屑(如铁、铜)含量异常需排查设备磨损点。
3. 氧化安定性评估
采用旋转氧弹试验(ASTM D2272)检测抗氧化能力: • 新油氧化诱导期应>1000分钟; • 运行油若下降至初始值30%以下,需补充抗氧化剂。
4. 添加剂损耗监测
通过红外光谱(FTIR)分析抗氧剂、防锈剂等关键成分浓度: • 抗氧剂(如T501)损耗>40%需补加; • 检测ZDDP类极压剂是否降解产生硫酸盐。
5. 泡沫特性与空气释放性
依据ASTM D892标准: • 泡沫倾向性(序列I)应<450/0mL; • 空气释放值(ASTM D3427)需<5分钟,避免形成气穴腐蚀。
检测周期与预警机制
新建机组应每周取样,稳定运行后延长至每月检测。当出现酸值突增、粘度变化>5%、金属颗粒激增等情况时,需启动二级预警并缩短检测频率。建议结合在线监测(如水分传感器)与实验室分析,构建多维度的油品健康管理系统。
结语
矿物涡轮机油的质量管控是预防性维护的重要手段。通过规范执行检测项目,电厂可有效延长换油周期(从传统1年延长至3-5年),降低运维成本约25%,同时减少非计划停机风险。建议采用ASTM/IEC标准体系,并定期与设备制造商、油品供应商开展技术联评,持续优化检测方案。
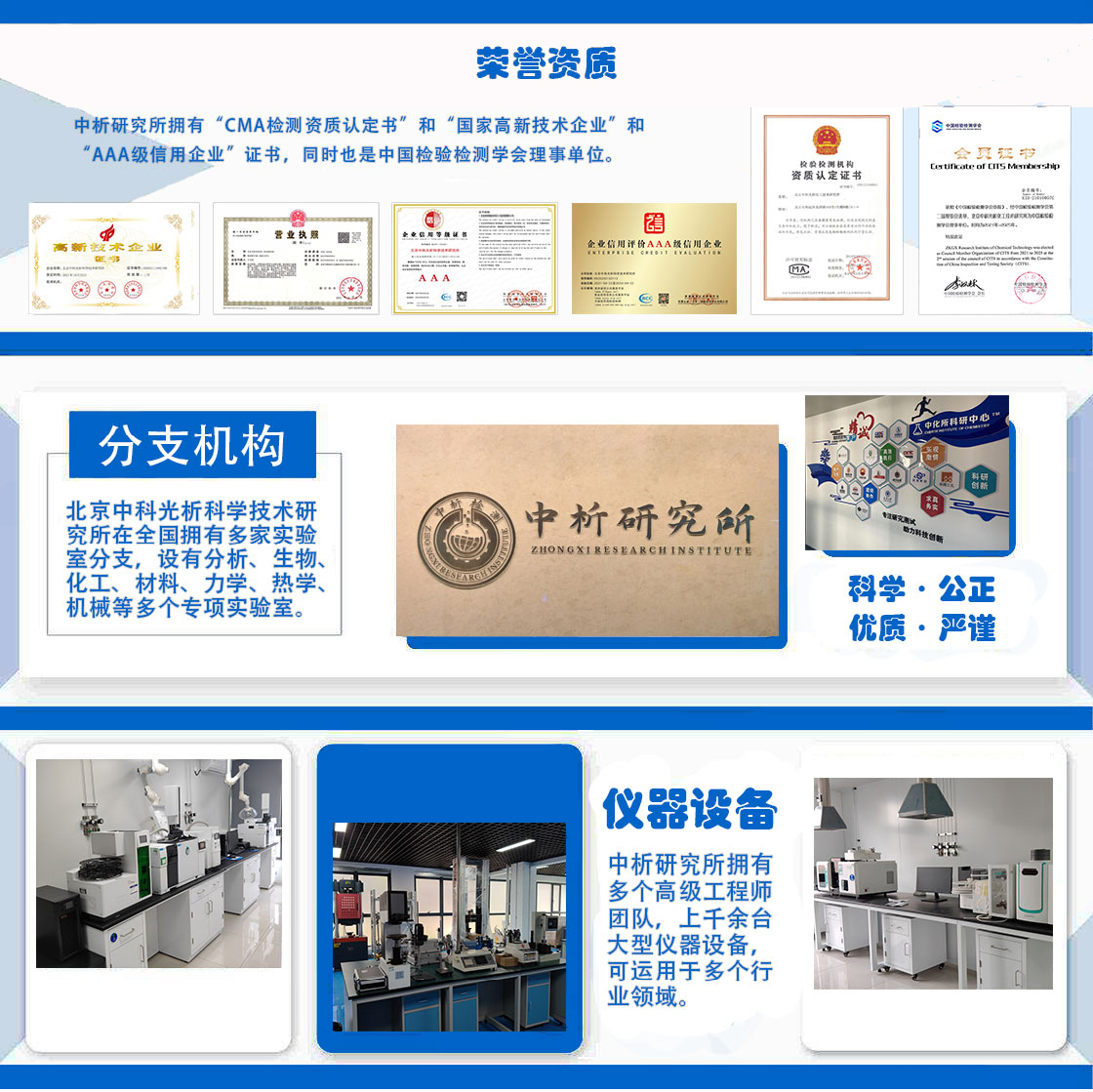
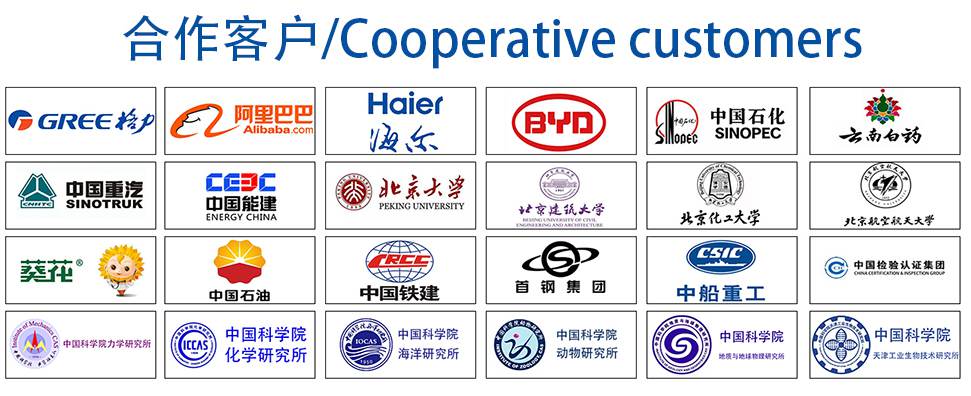