漆膜质量检测的重要性与核心内容
漆膜作为工业生产和日常用品表面保护的关键层,其质量直接影响产品的使用寿命、外观表现及功能性。漆膜质量检测是生产过程质量控制的重要环节,通过科学系统的检测手段,可评估涂层的附着力、硬度、耐腐蚀性、抗老化性等关键性能指标。在汽车制造、船舶工业、建筑装饰等领域,未达标的漆膜可能导致涂层脱落、锈蚀扩散或色彩失真等问题,造成经济损失甚至安全隐患。因此,建立完善的漆膜检测体系,对于保障产品质量、提升企业信誉具有不可替代的作用。
核心漆膜质量检测项目
1. 附着力测试
附着力是衡量漆膜与基材结合强度的核心指标,直接影响涂层的耐久性。常用检测方法包括划格法(ASTM D3359)、拉开法(ISO 4624)和划痕试验。通过专业仪器定量分析漆膜剥离时的受力值,判断其是否符合GB/T 9286或行业标准要求。
2. 硬度检测
漆膜硬度反映其抗刮擦和机械损伤能力,主要采用铅笔硬度法(ASTM D3363)和摆杆硬度法(ISO 1522)。测试时需根据涂层类型选择合适硬度等级的铅笔或摆杆仪器,确保数据可比性。
3. 厚度测定
漆膜厚度直接关联防护效果与成本控制。磁性测厚仪(铁基材)和涡流测厚仪(非铁基材)是常用工具,检测需遵循ISO 2808标准,测量点应覆盖工件表面各区域以避免局部过厚/过薄。
4. 耐腐蚀性评估
通过盐雾试验(ASTM B117)、湿热试验(GB/T 1740)模拟极端环境,检测漆膜抗腐蚀能力。测试周期结束后,需量化评估起泡、锈斑面积及腐蚀深度等参数。
5. 光泽度与色差分析
使用60度角光泽度仪(ASTM D523)和色差仪(CIE Lab体系)检测表面光学性能。色差ΔE值需≤1.5(工业级)或≤0.5(高端消费品),光泽度偏差需控制在±5GU以内。
6. 耐候性测试
通过氙灯老化试验(ISO 11341)、紫外加速老化试验(ASTM G154)模拟长期光照影响,评估漆膜黄变、粉化等老化现象,测试周期通常为500-2000小时。
检测结果的应用与改进
检测数据需与工艺参数(如喷涂压力、固化温度)进行关联分析,指导生产工艺优化。例如:当附着力不足时,可调整基材前处理流程;耐候性差则需改进树脂配方。建立检测数据库,还可为产品质保提供追溯依据。
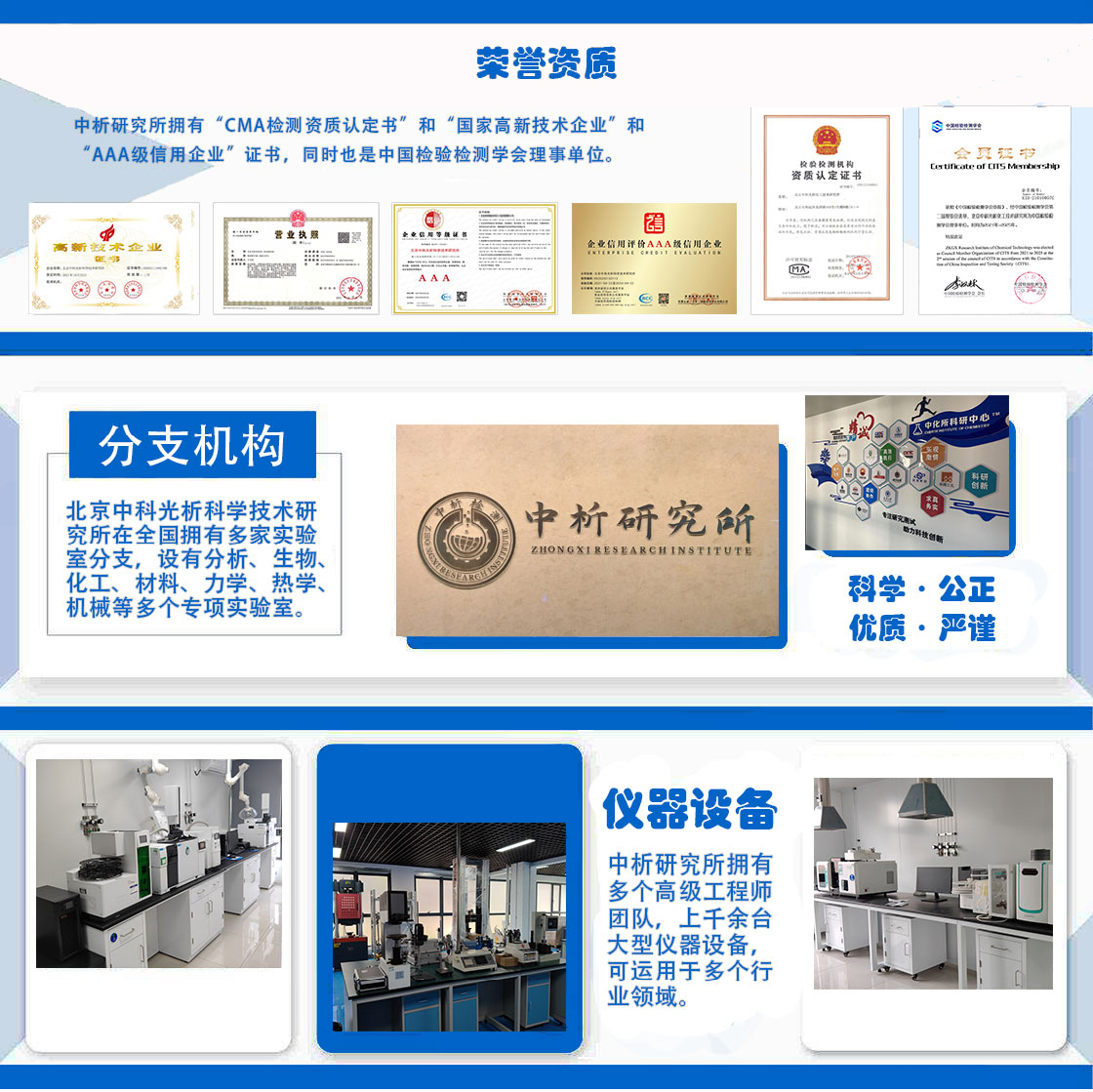
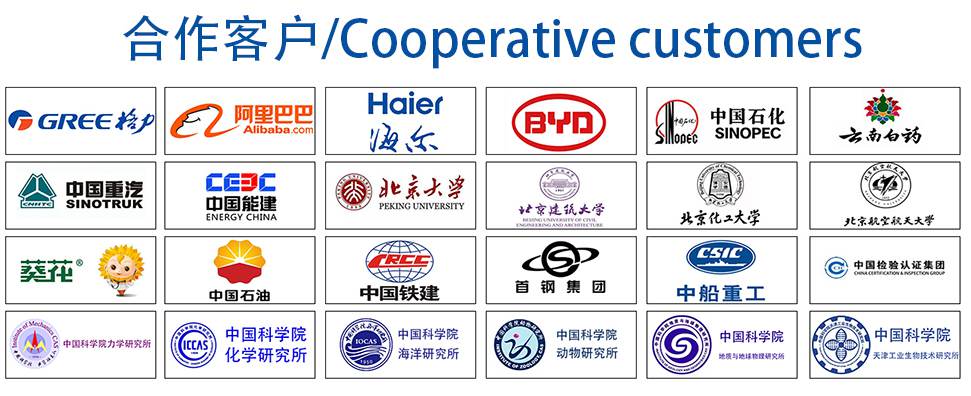